CNC Machining Determine Cutting Amount
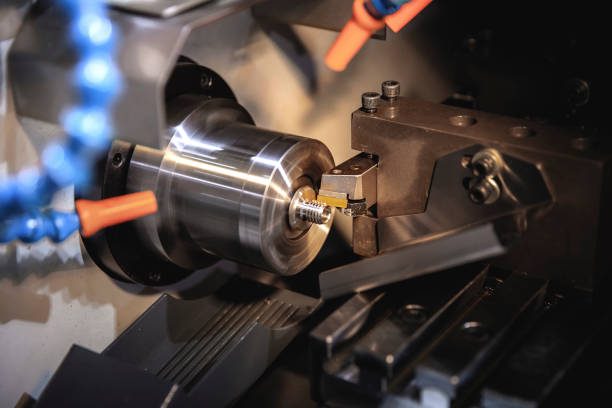
In NC programming, the programmer must determine the cutting amount of each process and write it in the program in the form of instructions. Cutting parameters include spindle speed, back-cutting amount and feed speed. For different processing methods, different cutting parameters need to be selected. The selection principle of the cutting amount is to ensure the machining accuracy and surface roughness of the parts, give full play to the cutting performance of the tool, ensure reasonable tool durability, and give full play to the performance of the machine tool to maximize productivity and reduce costs.
1. Determine the Spindle Speed
The spindle speed should be selected according to the allowable cutting speed and the diameter of the workpiece (or tool). The calculation formula is: n=1000 v/7 1D where: v? cutting speed, the unit is m/m movement, which is determined by the durability of the tool; n is the spindle speed, the unit is r/min, and D is the diameter of the workpiece Or tool diameter, in mm. For the calculated spindle speed n, the speed that the machine tool has or is close to should be selected at the end.
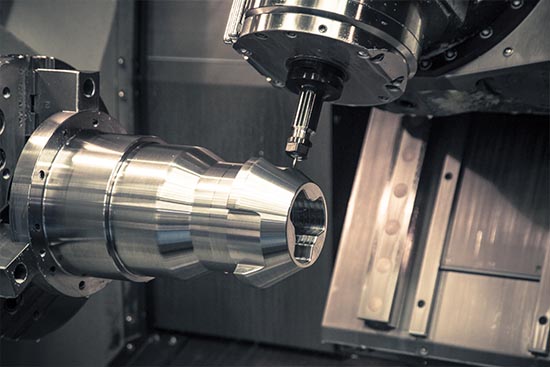
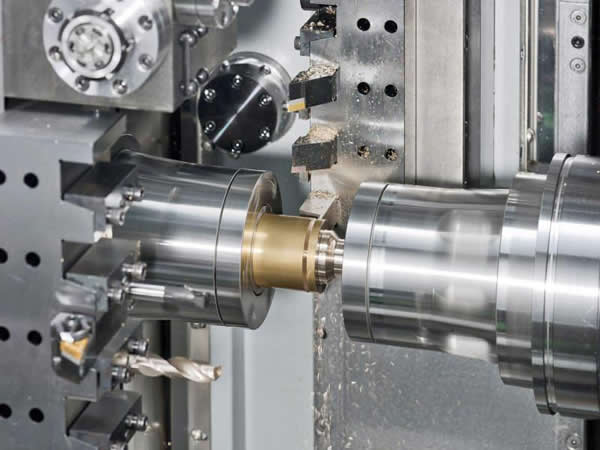
2. Determine the Feed Rate
Feed speed is an important parameter in the cutting parameters of CNC machine tools, which is mainly selected according to the machining accuracy and surface roughness requirements of the parts and the material properties of the tools and workpieces. The maximum feed rate is limited by the rigidity of the machine tool and the performance of the feed system. The principle of determining the feed rate: When the quality requirements of the workpiece can be guaranteed, in order to improve the production efficiency, a higher feed rate can be selected. Generally selected in the range of 100-200mm/min; when cutting, processing deep holes or processing with high-speed steel tools, it is advisable to choose a lower feed speed, generally selected in the range of 20-50mm/min; when the processing accuracy, the surface When the roughness requirement is high, the feed speed should be selected smaller, generally in the range of 20-50mm/min; when the tool is empty, especially when the long distance "return to zero", you can set the CNC system settings of the machine tool The highest feed rate.
3. Determine the amount of Rear Tools
The amount of back-grabbing is determined by the rigidity of the machine tool, workpiece and cutting tool. When the rigidity allows, the amount of back-grabbing should be equal to the machining allowance of the workpiece as much as possible, which can reduce the number of passes and improve production efficiency. In order to ensure the quality of the machined surface, a small amount of finishing allowance can be left, generally 0.2-0.5mm. In short, the specific value of the cutting amount should be determined by analogy based on the performance of the machine tool, related manuals and actual experience.
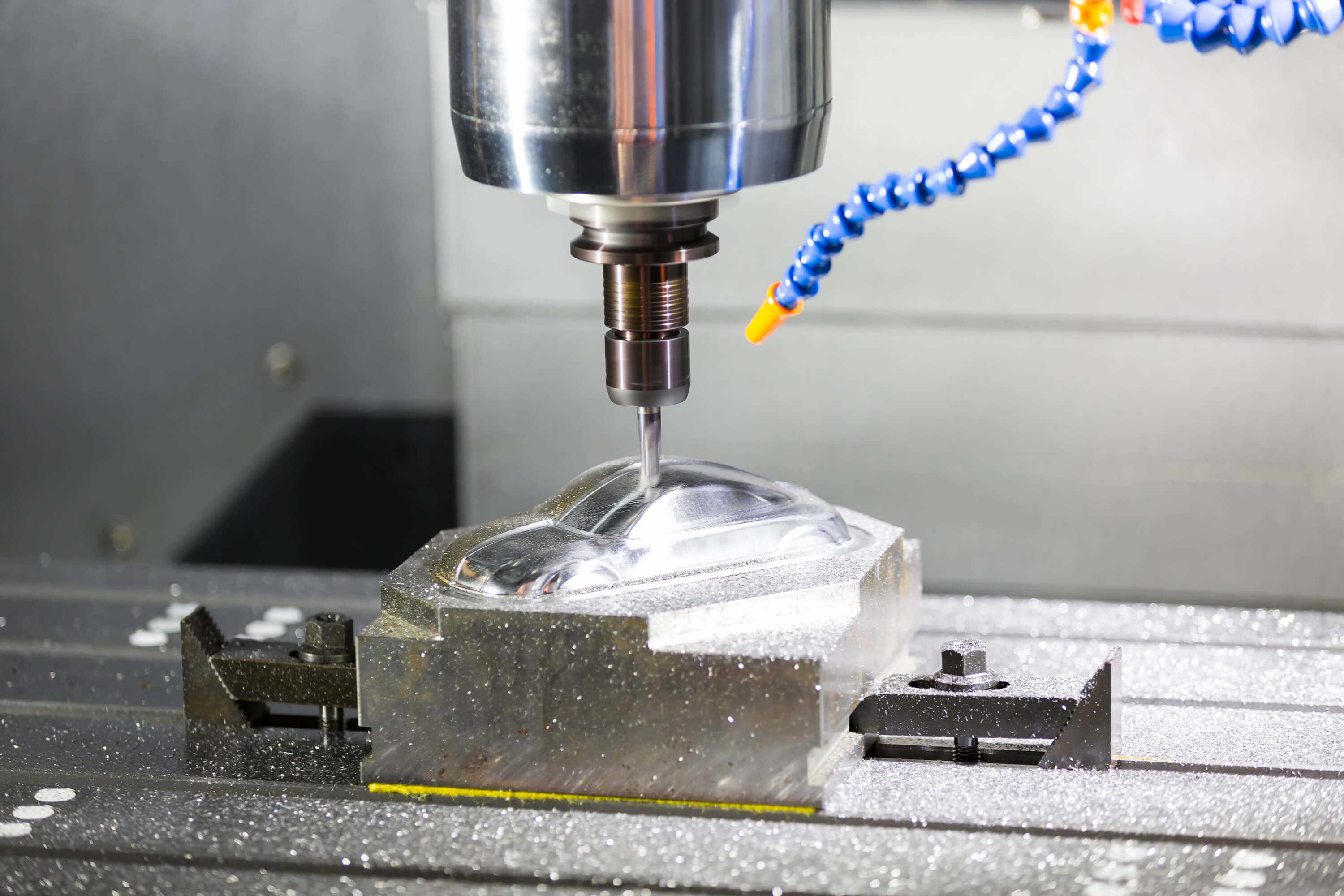
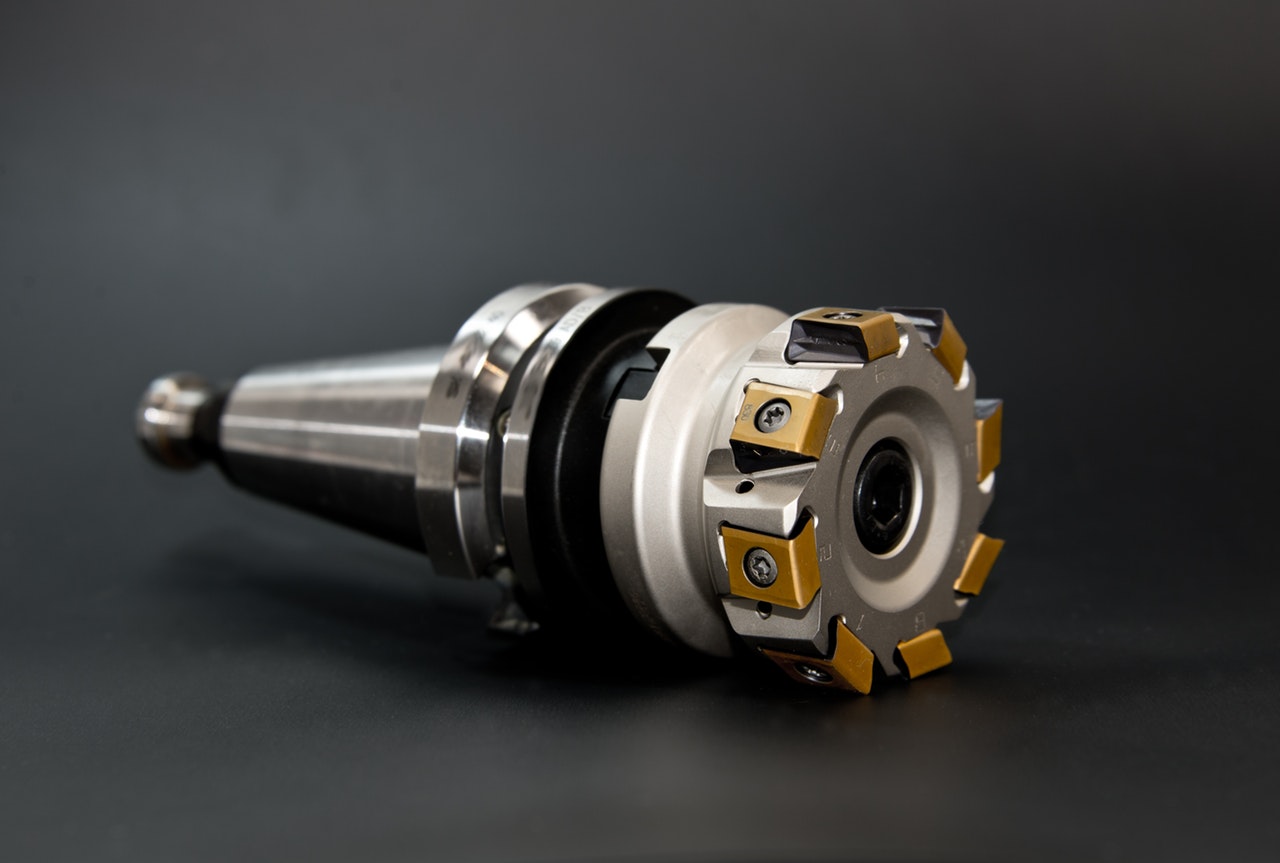
At the same time, the spindle speed, cutting depth and feed speed can be adapted to each other to form the best cutting amount.
The cutting amount is not only an important parameter that must be determined before the machine tool is adjusted, but also whether its value is reasonable or not has a very important influence on the processing quality, processing efficiency, and production cost. The so-called "reasonable" cutting amount refers to the cutting amount that makes full use of the cutting performance of the tool and the dynamic performance (power, torque) of the machine tool to obtain high productivity and low processing cost under the premise of ensuring quality.
The tip of this type of turning tool is composed of linear main and secondary cutting edges, such as 900 internal and external turning tools, left and right end face turning tools, grooving (cutting) turning tools, and various external and internal cutting edges with small tip chamfers. Hole turning tool. The selection method of the geometric parameters of the pointed turning tool (mainly the geometric angle) is basically the same as that of ordinary turning, but the characteristics of CNC machining (such as machining route, machining interference, etc.) should be considered comprehensively, and the tool tip itself should be considered strength.
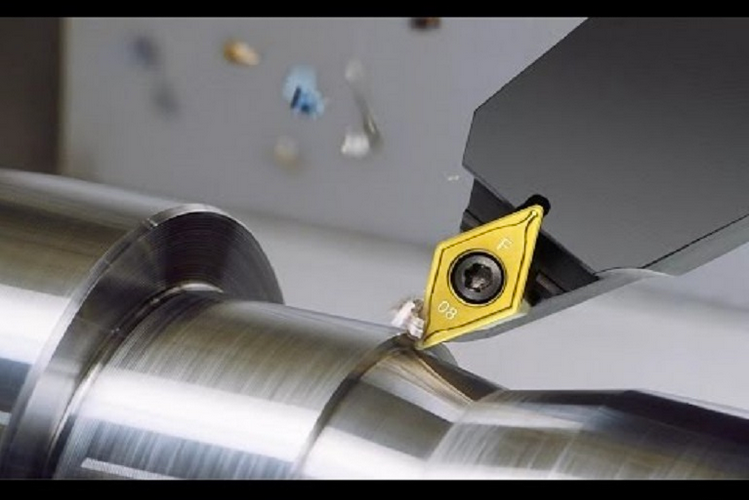
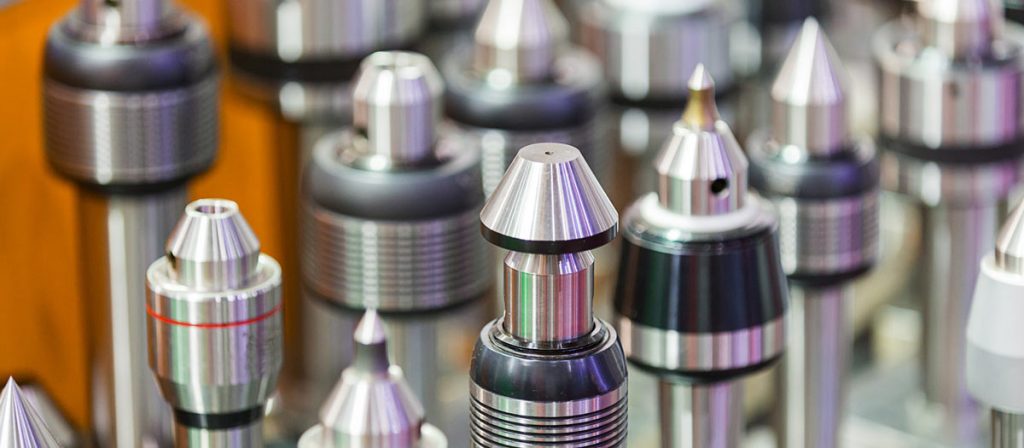