CNC High Precision Machining Parts
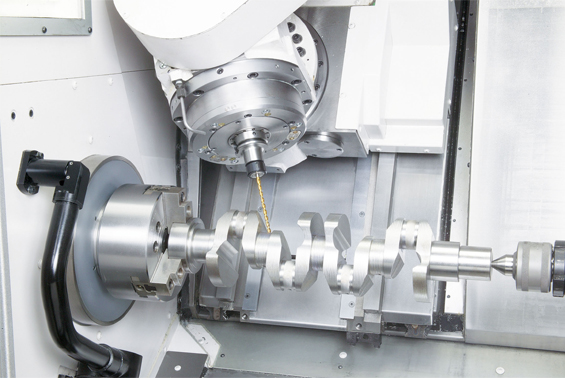
In today's fast-paced manufacturing industry, precision and efficiency are crucial for businesses to stay competitive. The need for high-quality, consistently accurate, and rapidly produced parts has led to the development of advanced machining technologies. Among them, CNC Machining stands out as a game-changer that revolutionizes the way we approach precision manufacturing. CNC (Computer Numerical Control) Machining is a cutting-edge technology that utilizes computer software to control machinery, ensuring precise and repeatable results. Unlike traditional machining processes, which heavily rely on manual labor and human intervention, CNC Machining streamlines the manufacturing process, offering enhanced accuracy, reduced human error, and increased productivity.
The heart of CNC Machining lies in its ability to transform a digital design, created using specialized software, into a physical reality. The intricate designs, complex shapes, and critical dimensions that were once challenging to achieve with traditional methods are now easily accomplished with CNC Machining. By precisely controlling the movement of cutting tools, CNC machines can produce parts with unmatched accuracy, tight tolerances, and swift turnaround times. One of the key advantages of CNC Machining is its versatility across a wide range of materials. Whether its metals, plastics, wood, or composites, CNC Machining can flawlessly cut, mill, drill, and shape various materials. This versatility makes it a go-to choice for industries such as aerospace, automotive, medical, electronics, and many others, where exact specifications and high-quality finishes are paramount.
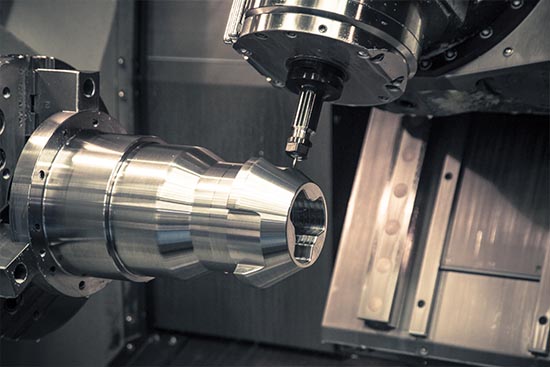
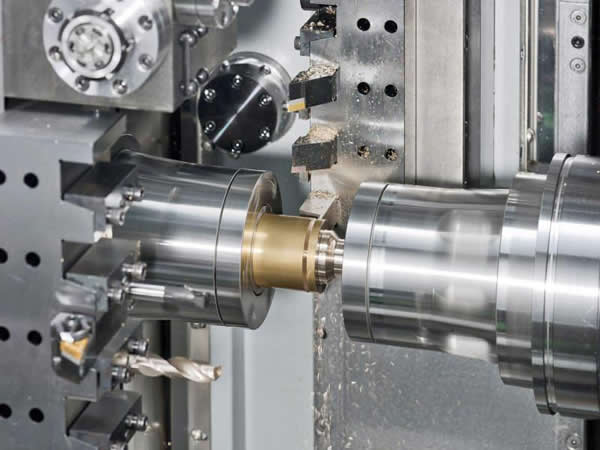
Moreover, CNC Machining boasts exceptional efficiency, allowing manufacturers to optimize their production processes and reduce costs. The automation introduced by CNC Machining eliminates the need for manual setup and constant monitoring, allowing operators to focus on other tasks while the machine operates autonomously. This efficiency greatly speeds up production, leading to shorter lead times and overall enhanced customer satisfaction. Beyond precise part production, CNC Machining offers a myriad of other benefits. It empowers manufacturers to prototype quickly, iterate designs effortlessly, and adapt to evolving market demands with ease. By utilizing advanced software programs, CNC machines can simulate manufacturing processes, detect potential errors, and optimize tool paths, leading to greater overall efficiency and material savings.
In addition, CNC Machining promotes sustainability by minimizing waste and maximizing resource utilization. By accurately determining cutting depths and tool movements, CNC machines significantly reduce material waste compared to traditional methods. Moreover, the ability to utilize scraps and leftovers for other parts further contributes to a more sustainable manufacturing approach. When it comes to CNC Machining, precision, efficiency, versatility, and sustainability are the driving forces behind its explosive popularity in the manufacturing industry. By combining state-of-the-art technology with the expertise of skilled operators, CNC Machining has transformed the way we approach complex part production, prototyping, and beyond.
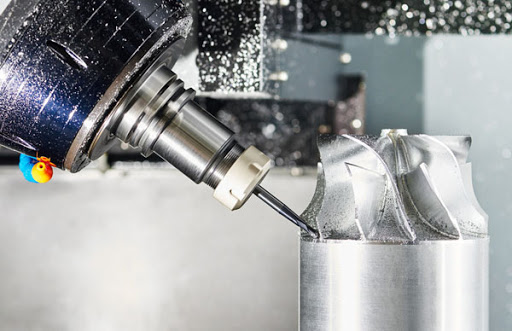
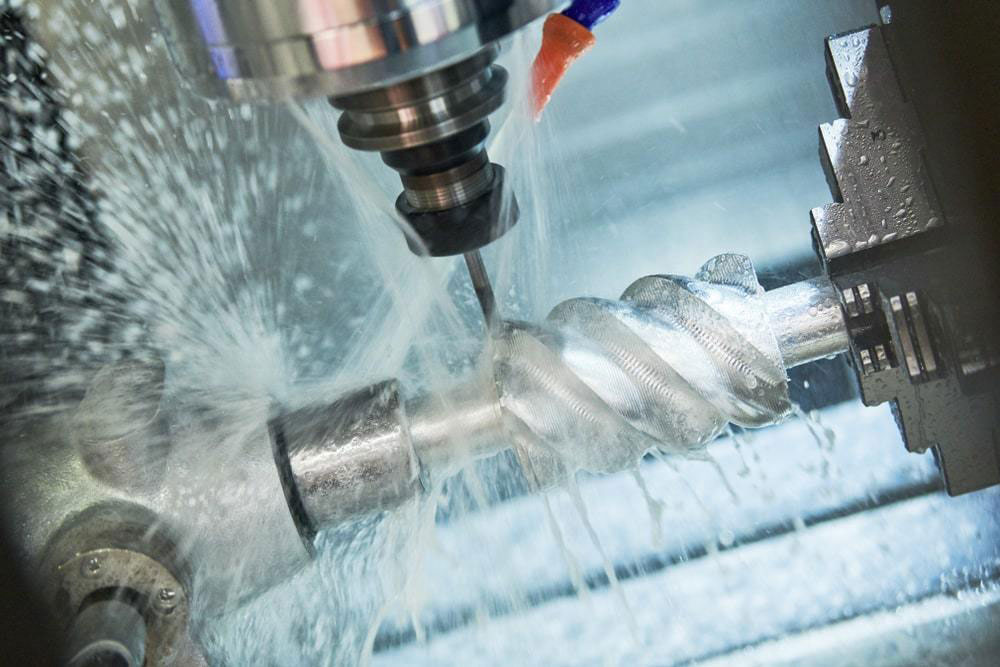
In conclusion, CNC Machining has emerged as a game-changing technology, reshaping the manufacturing landscape. Its unmatched precision, versatile material capabilities, and cost-effective production processes make it an invaluable tool for industries worldwide. By embracing CNC Machining, businesses can meet the ever-increasing demands of quality, speed, and accuracy, ensuring their success in today's competitive market.
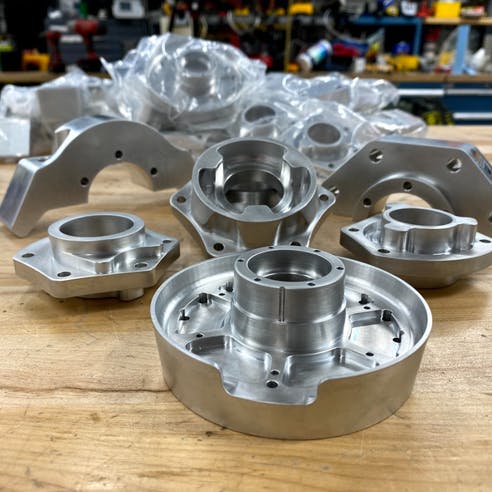
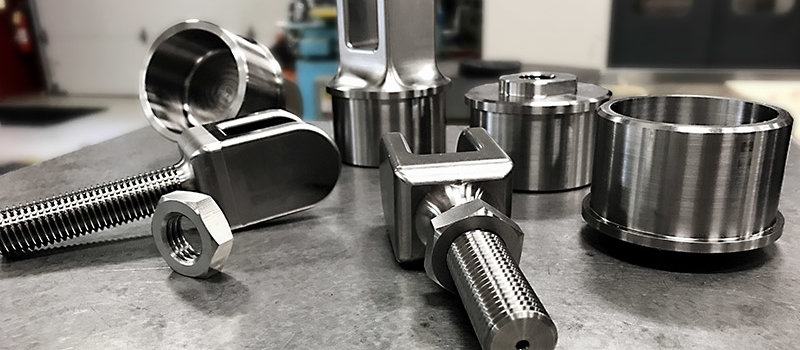
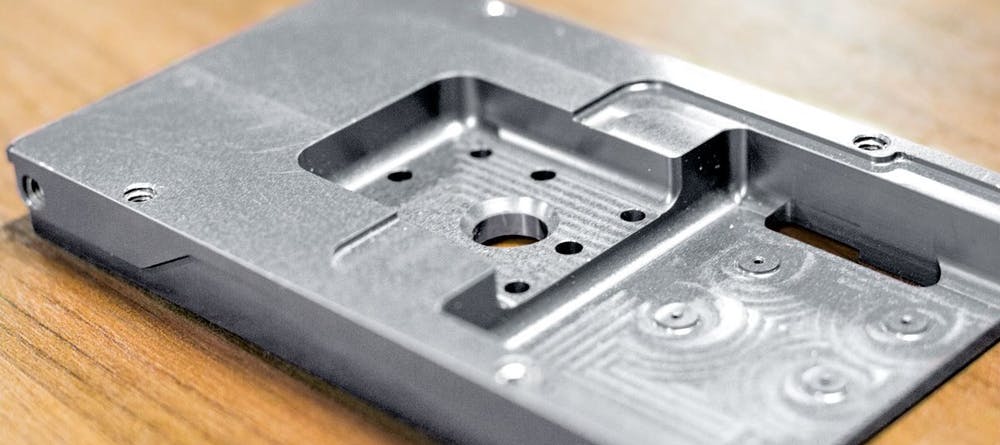
Send your message to us:
-
Axis High Precision CNC Machining Parts
-
Titanium and Titanium Alloy Fittings
-
Titanium and Titanium Alloy Forgings
-
Titanium and Titanium Alloy Wires
-
Titanium Bars
-
Titanium Seamless Pipes/Tubes
-
Titanium Welded Pipes/Tubes
-
Aluminum CNC Machining Parts
-
Auto Parts Machining
-
CNC Auto Parts Machined Parts
-
CNC Machined Components
-
Aluminum Sheet Metal Fabrication
-
Automotive Industry
-
Centerless Grinding
-
CNC Machining Advantages
-
CNC Machining Aluminum Parts