CNC Machining Operational Safety
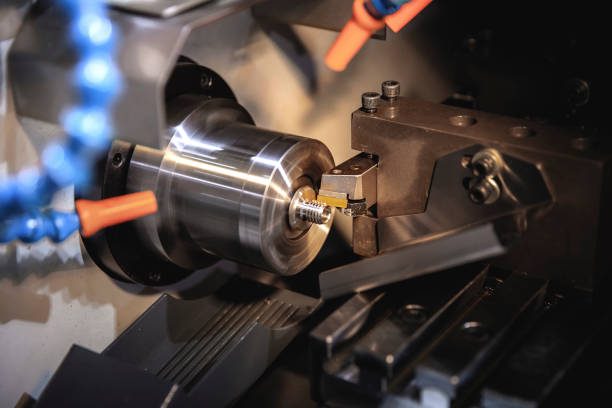
Matters needing attention during debugging
1) Edit, modify and debug the program. If it is the first piece of trial cut, it must be dry run to ensure that the program is correct.
2) Install and debug the fixture according to the process requirements, and remove the iron filings and debris on each positioning surface.
3) Clamp the workpiece according to the positioning requirements to ensure correct and reliable positioning. Do not loosen the workpiece during processing.
4) Install the tool to be used. If it is a machining center, the tool position number on the tool magazine must be strictly consistent with the tool number in the program.
5) Perform tool setting according to the programmed origin on the workpiece to establish a workpiece coordinate system. If multiple tools are used, the remaining tools will be compensated for length or tip position respectively.
Numerically controlled machine tools are increasingly widely used in mechanical processing due to their high precision, high efficiency, and adaptability to the processing of small batches of multiple varieties of complex parts. In summary, the processing of CNC machine tools has the following advantages.
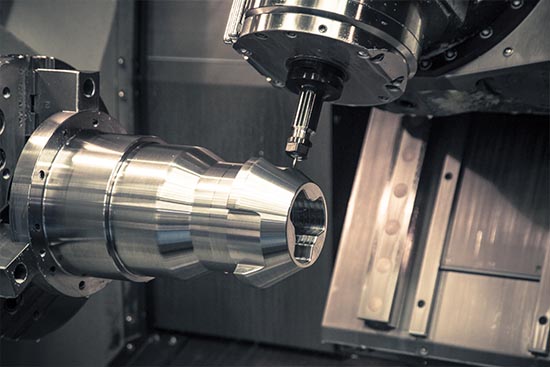
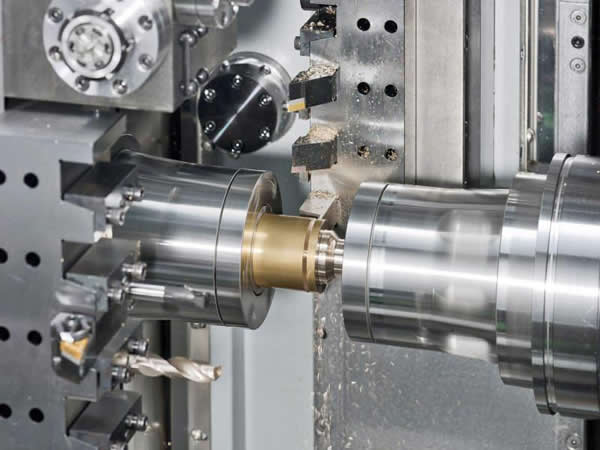
(1) Strong adaptability. Adaptability is the so-called flexibility, which is the adaptability of the index-controlled machine tool to change with the change of the production object. When changing the machining parts on the CNC machine tool, you only need to reprogram the program and input the new program to realize the processing of the new part; there is no need to change the hardware of the mechanical part and the control part, and the production process is completed automatically. This provides great convenience for single, small batch production and trial production of new products of complex structure parts. Strong adaptability is the most prominent advantage of CNC machine tools, and it is also the main reason for the production and rapid development of CNC machine tools.
(2) High precision and stable quality. CNC machine tools are processed in accordance with instructions given in digital form. Under normal circumstances, the work process does not require manual intervention, which eliminates the error caused by the operator. When designing and manufacturing CNC machine tools, many measures have been taken to make the mechanical part of CNC machine tools reach a higher precision and rigidity. The movement equivalent of the worktable of CNC machine tools generally reaches 0.01~0.0001mm, and the backlash of the feed transmission chain and the error of the lead screw pitch can be compensated by the CNC device. The high-end CNC machine tool adopts the grating ruler for closed-loop control of the worktable movement. The machining accuracy of CNC machine tools has increased from ±0.01 mm in the past to ±0.005 mm or even higher. The positioning accuracy has reached ±0.002mm~±0.005mm in the early and mid-1990s.
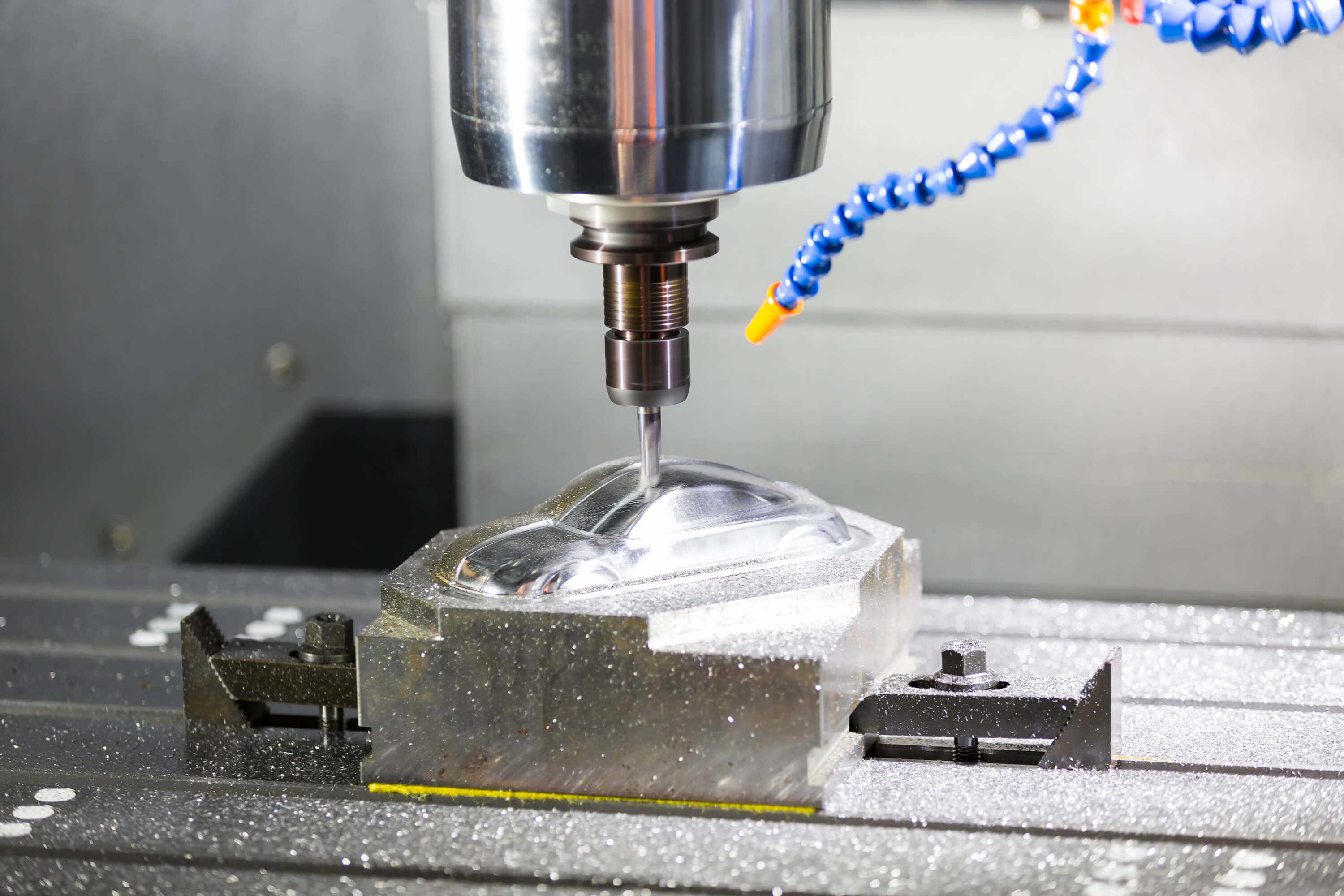
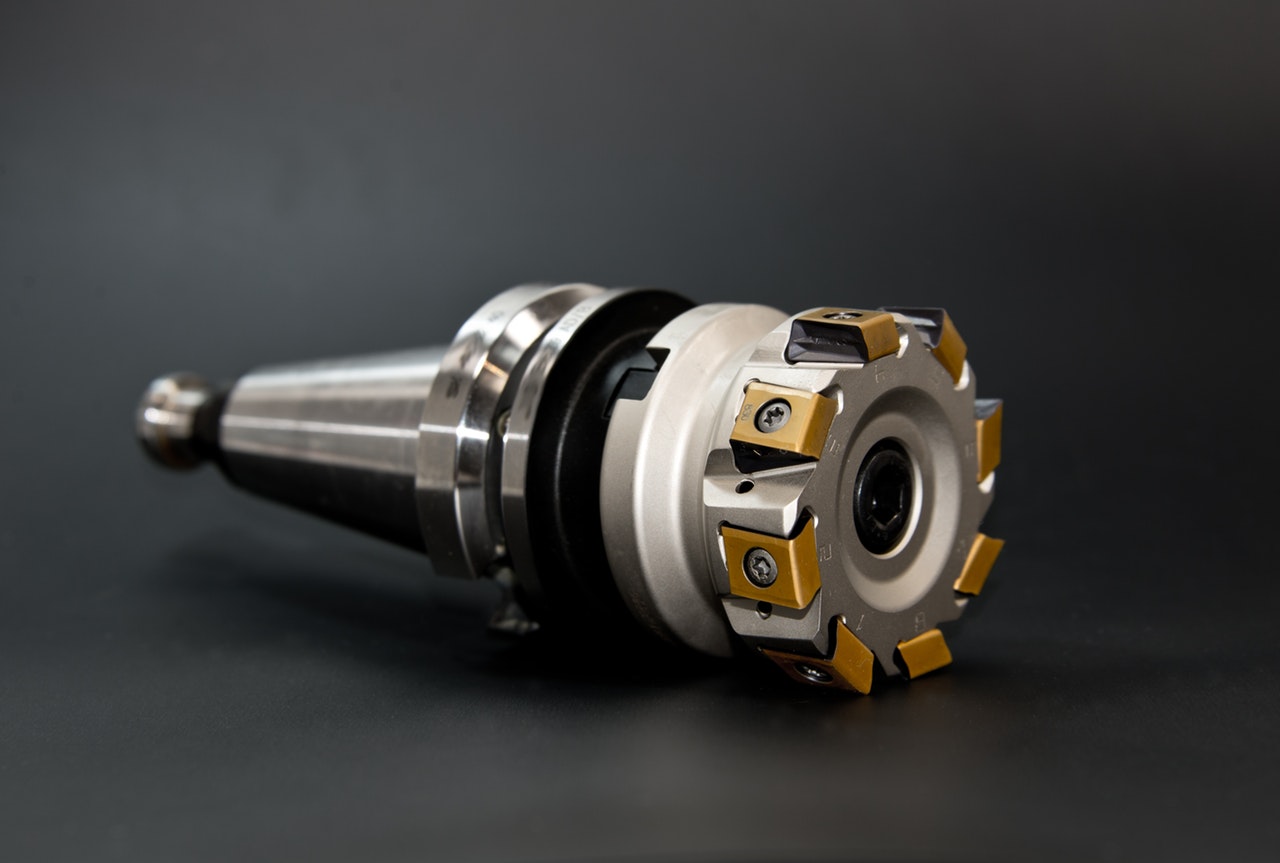
In addition, the transmission system and the structure of the CNC machine tool have high rigidity and thermal stability. Through compensation technology, CNC machine tools can obtain higher processing accuracy than their own. In particular, the consistency of the production of the same batch of parts is improved, the product qualification rate is high, and the processing quality is stable.
(3) High production efficiency. The time required for parts processing mainly includes two parts: maneuvering time and auxiliary time. The spindle speed and feed rate of the CNC machine tool have a larger variation range than ordinary machine tools. Therefore, each process of the CNC machine tool can choose the most favorable cutting amount. Due to the high rigidity of the CNC machine tool structure, it allows powerful cutting with a large amount of cutting, which improves the cutting efficiency of the CNC machine tool and saves maneuvering time. The moving parts of the numerical control machine tool have a fast idle travel speed, a short workpiece clamping time, and the tool can be automatically replaced, and the auxiliary time is greatly reduced compared with ordinary machine tools.
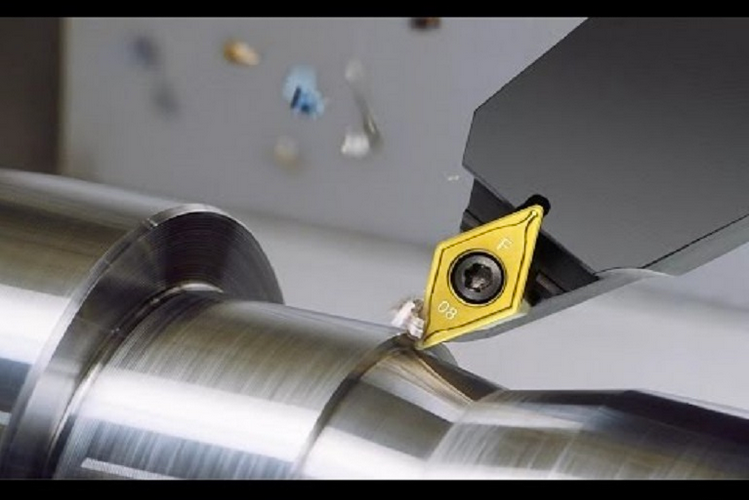
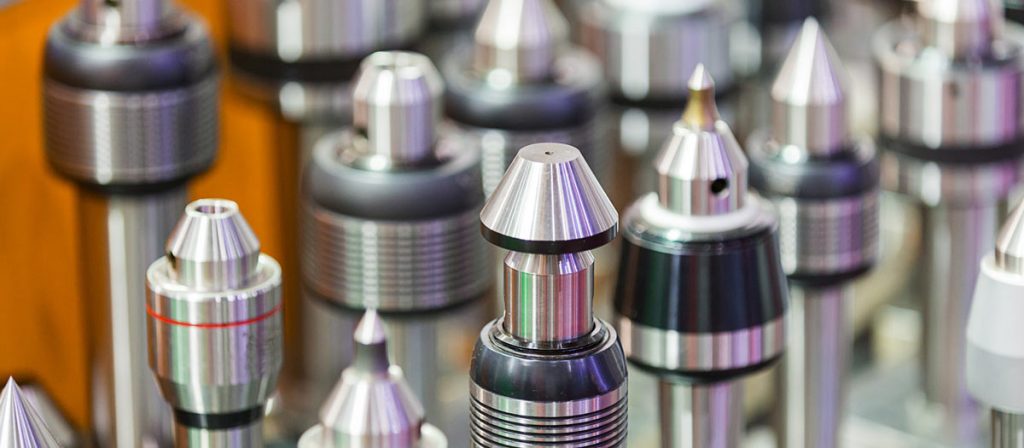