How to choose a tool?
In fact, in mechanical processing, the choice of what tool is mainly based on the processing materials and processing properties to decide. Choose the right tool, improve not only the processing efficiency and processing quality, but also the life of the tool. High hardness of the workpiece material, generally with higher hardness of the tool to process, the hardness of the tool material must be higher than the workpiece material hardness.
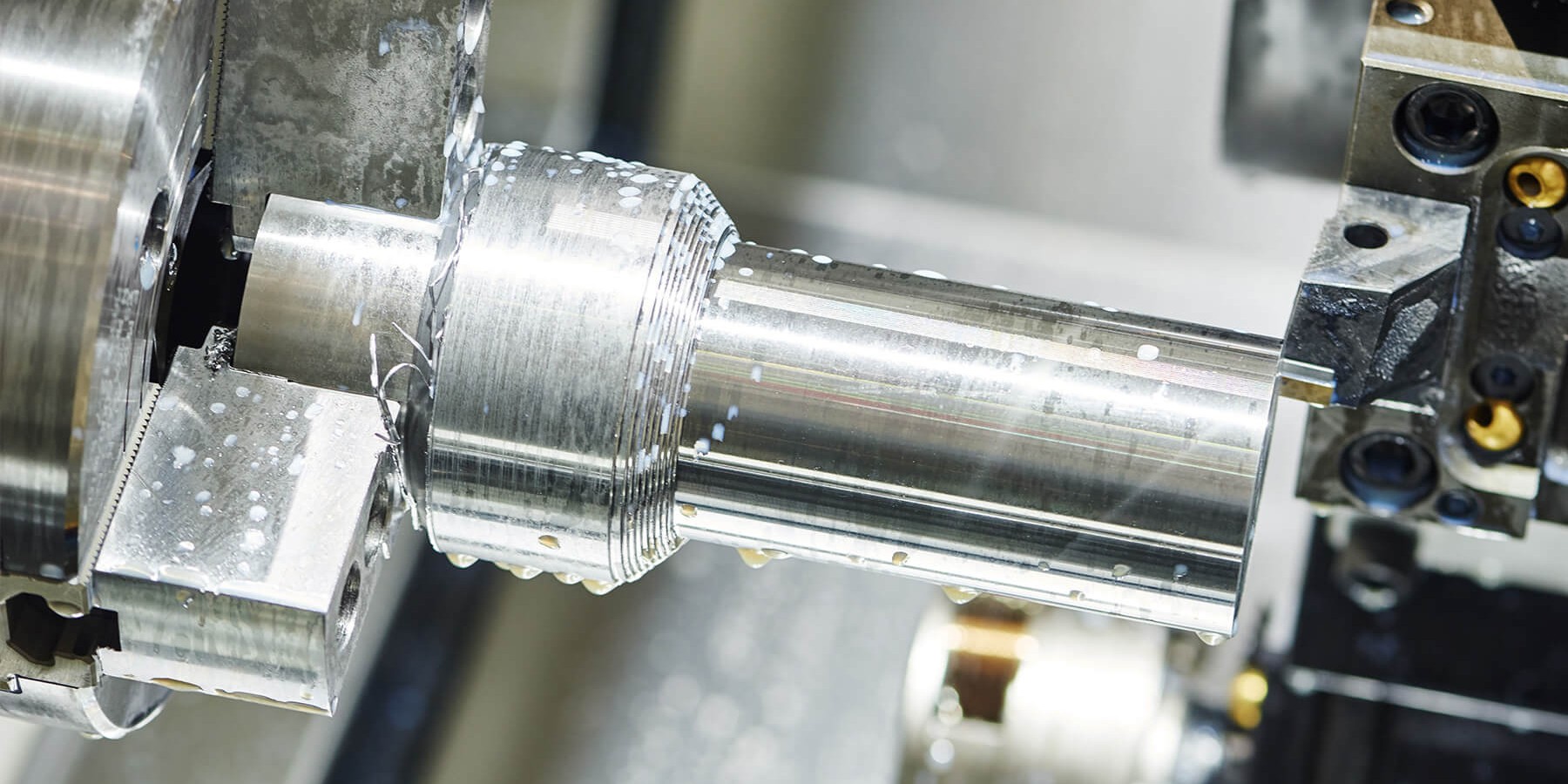
In mechanical processing, in order to process a qualified product, the thickness of that layer of metal that must be cut from the blank, called processing allowance. Processing allowance can be divided into process allowance and total allowance. The amount of metal that needs to be removed in a process is the processing allowance for that process. The total amount of margin that needs to be removed from the blank to the finished product is the total margin, equal to the sum of the corresponding surface allowances of each process.
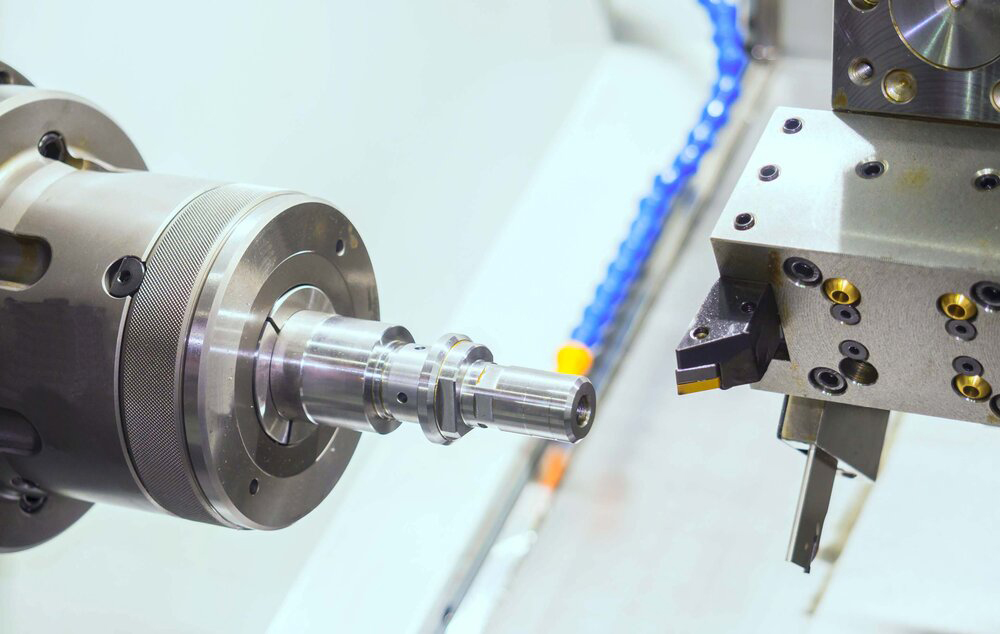
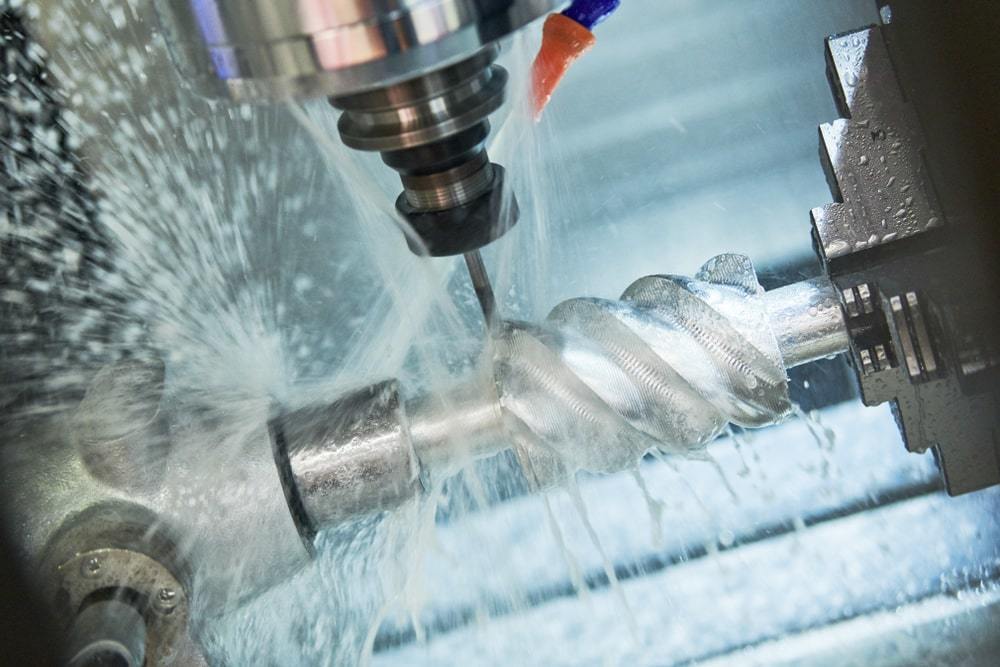
The purpose of machining allowance on the workpiece is to remove the machining error and surface defects left by the last procedure, such as the casting surface cold hard layer, porosity, sand layer, forging surface scale, decarbonization layer, surface cracks, internal stress layer and surface roughness after machining. Thus improve the accuracy and surface roughness of the workpiece.
Mechanical processing
Machining allowance has great influence on machining quality and production efficiency. Processing allowance is too large, not only increases the amount of mechanical processing labor, reduce productivity, but also increases the consumption of materials, tools and power, and improves the processing cost. If the processing allowance is too small, it can not eliminate the various defects and errors of the previous process, and can not compensate for the clamping error of the process, resulting in waste. Therefore, the selection principle is to ensure the quality of the premise, so that the margin as small as possible. Generally speaking, the more finishing, the smaller the process allowance.
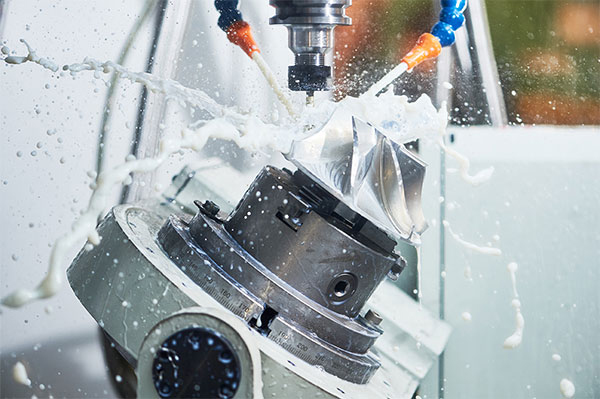
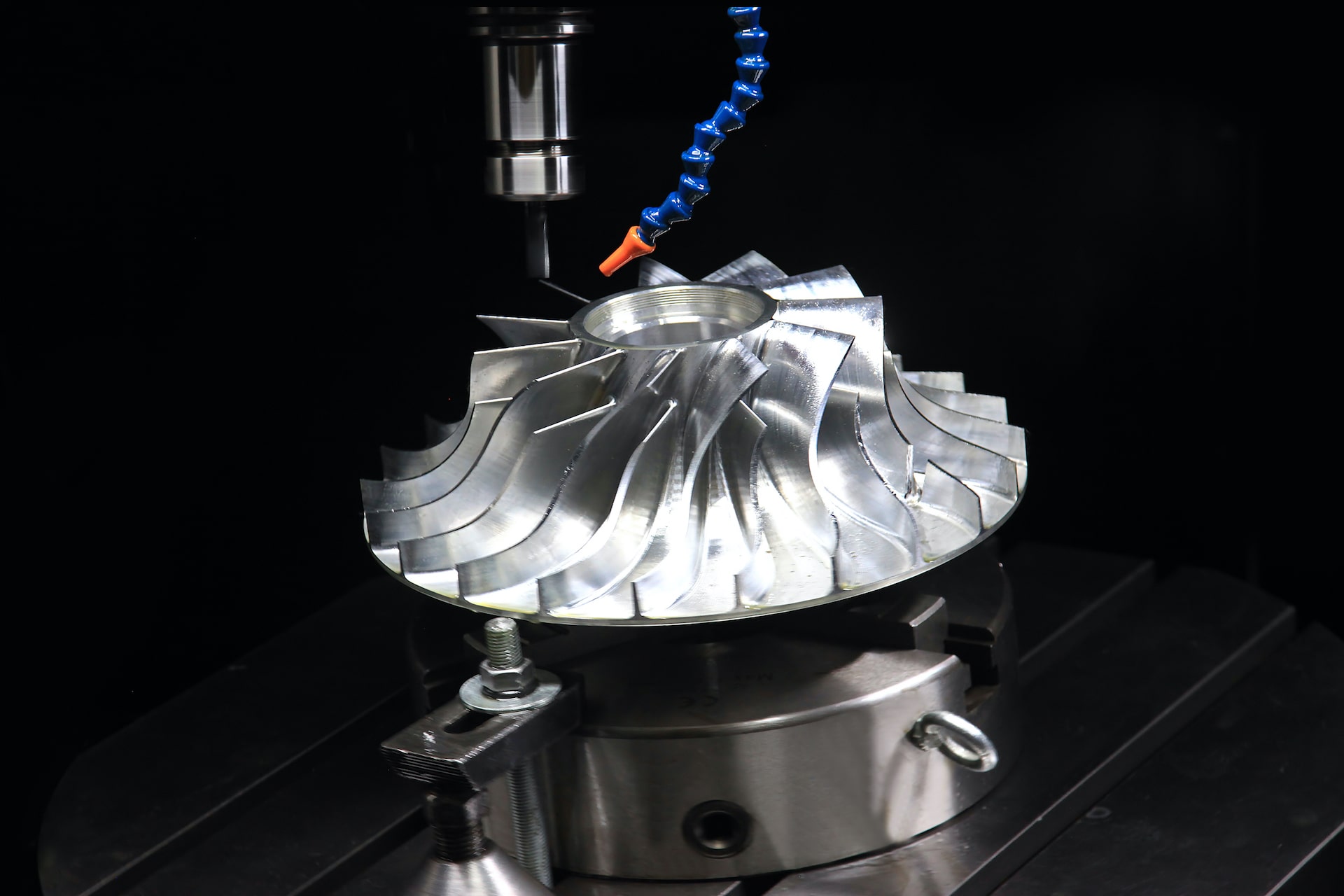
At present, for precision machining ordinary non-standard parts has been very simple, but the development of Shilihe has been constantly changing the process, simplify unnecessary links to shorten the processing time. And independent research and development of the corresponding technology, in order to further improve the quality of products. How to do this, we need several other aspects of cooperation.
First of all, for the technical personnel of Shili and precision parts processing, it is not only necessary to have strong technical support, but also rich working experience to deal with unexpected events. Otherwise, even if the company is equipped with how perfect equipment, it is difficult to make a blank into a high precision, quality parts.
Secondly, in order to produce high-quality products, Shilihe specially equipped with engineers with more than ten years of industry experience to formulate the process flow and analyze the details of all aspects from the drawings. Follow the scientific and reasonable actual situation, match the equipment and personnel required by the process, and strictly follow the process flow. In this way, work efficiency is improved and production cycle is shortened.
Thirdly, for the special requirements put forward by some customers, such as whether there will be problems during the assembly, the team of Shilihe will put forward corresponding opinions according to the system analysis. We know that some levels of details cannot be understood. In terms of providing processing drawings, we can only provide corresponding suggestions in accordance with our expertise before precision machining and communicate with customers about the progress of product processing in a timely manner during machining. Communication helps both of us to work better, providing efficiency and making quality parts that best meet customer needs.
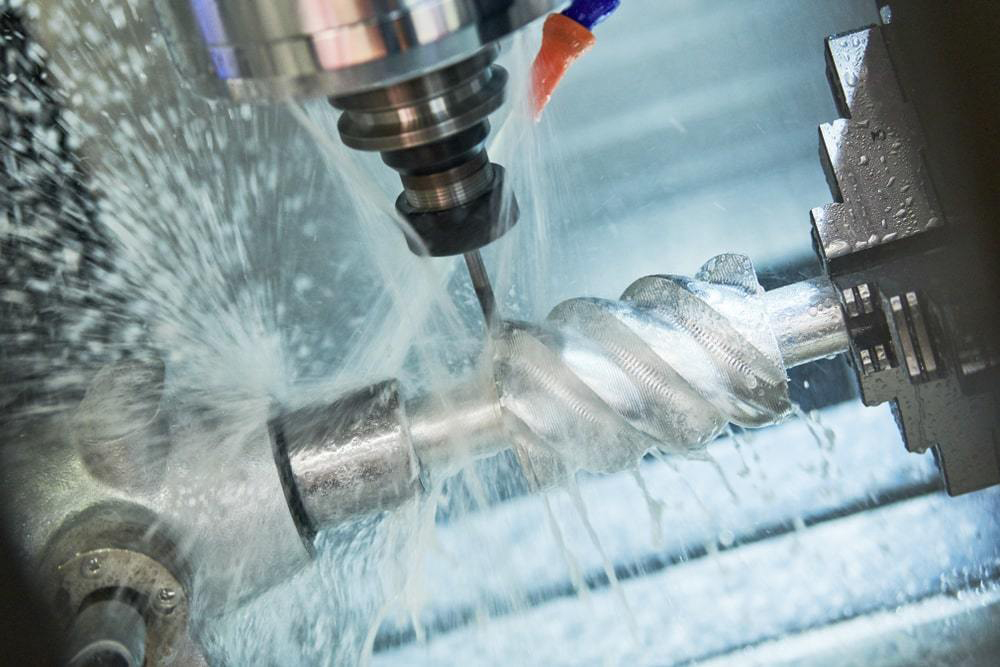