Several Metal Processing Techniques
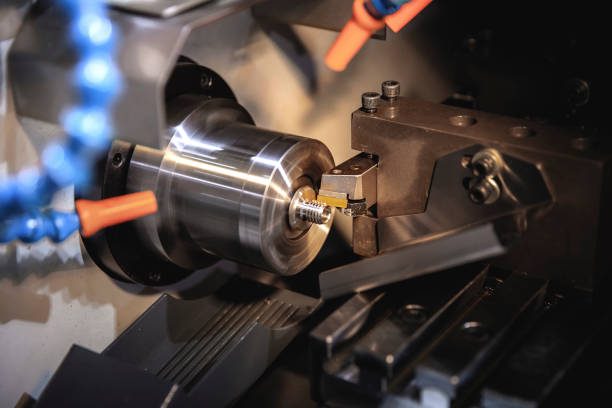
It is impossible to cover all of these techniques in one article. We'll pick six of them and explain what they are, their respective tools and possible use cases.
Metal Marking
Direct part marking is a range of techniques for permanent marking on metal for traceability of parts, labelling of industrial parts, decoration or any other purpose. Metal has been marked since humans started using metal tools such as axes and spears, and metal marking is as old as the invention of smelting technology. However, current technology has advanced to a level that allows humans to create complex marks with high precision for any product imaginable. Marking can be achieved by a variety of techniques including engraving, embossing, die casting, stamping, etching and grinding.
Metal Engraving
Engraving is a technique mainly used to engrave patterns, words, drawings or codes on metal surfaces to obtain products with permanent marks, or to use engraved metal to print engravings on paper. Engraving mainly uses two technical means: laser and mechanical engraving. Although laser technology is already very versatile and easy to use, it provides us with the highest quality metal engraving process because it is computer-aided and precisely pre-orders various surfaces for the best engraving results. Mechanical engraving can be done by hand, or by more reliable pantographs or CNC machines. Metal engraving technology can be used for: personalized jewelry, fine art, photopolymer laser imaging, industrial marking technology, engraving sports competition trophies, printing plate making, etc.
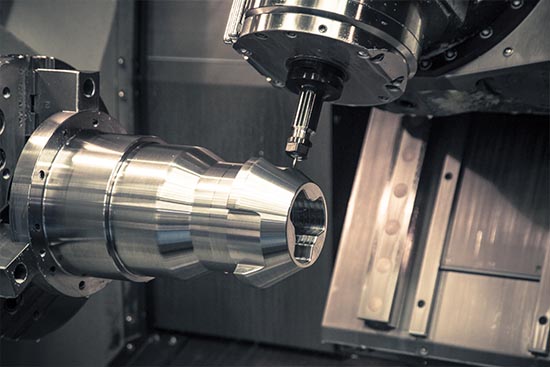
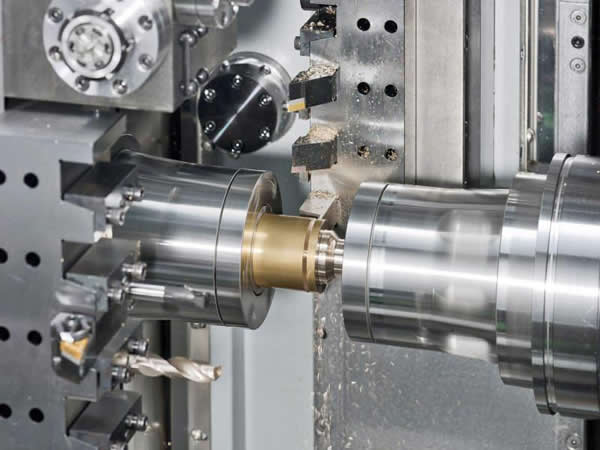
Metal Stamping
Metal stamping is not a subtractive process. It is the use of molds to fold metal sheets into various shapes. Household utensils that we come into contact with, such as pans, spoons, cooking pots and plates, are stamped. Punch presses are also used to make ceiling materials, medical equipment, machine parts and even coins. Its products are widely used in medical, electronic, electrical, automotive, military, HVAC, pharmaceutical, commercial and machinery manufacturing industries.
.
There are two types of metal stamping machines: mechanical and hydraulic. Sheets of stainless steel, aluminum, zinc, and copper are typically cast, punched, and cut into three-dimensional objects by these machines. They have very high product turnover due to their relative ease of processing. Punch presses can be arranged in tandem to process metal stock, using different step operations to finally convert them into finished parts and separate them from the processing line.
Presses are versatile and capable of producing a wide variety of products. These products come in different sizes and designs, and most are for industrial use. Usually, you can just send the sample and sheet metal to a company that does metal stamping and get what you want.
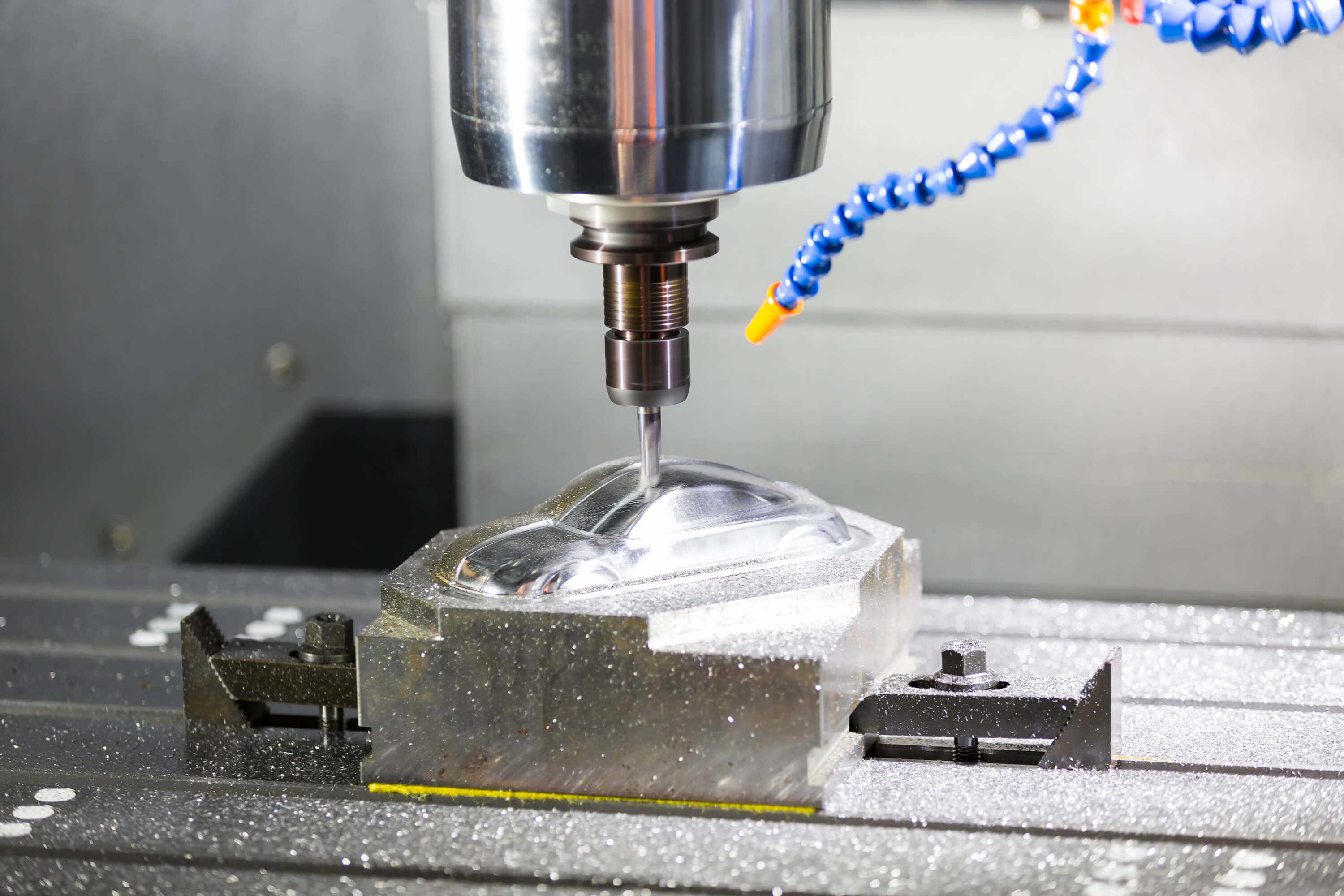
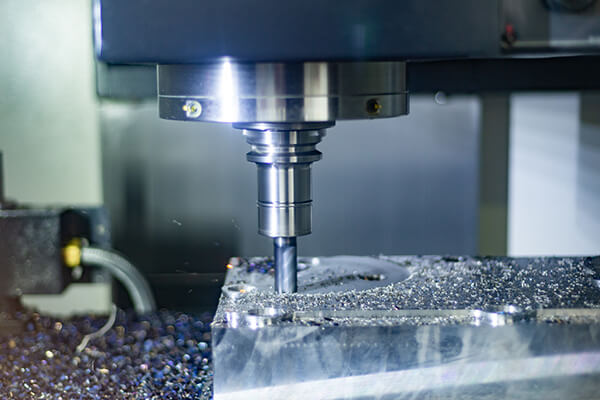
Metal Etching
Etching can be achieved by photochemical or laser processes. Laser etching is currently a popular technology. Over time, this technology has developed exponentially. It refers to high-precision etching by using a coherently amplified beam of light on a metal surface. Laser is the cleanest way to etch marks because it doesn't involve the use of aggressive reagents, or a drilling or grinding process that is noisy. It simply uses a laser beam to vaporize material as instructed by a computer program to create precise images or text. Due to the continuous advancement of technology, its size has become smaller and smaller, and researchers or laser hobbyists can now also buy new and cheaper laser equipment.
Chemical Etching
Chemical etching is the process of exposing a portion of a sheet of metal to a strong acid (or etchant) to cut a pattern into it and create a designed shape in a groove (or cut) in the metal. It is essentially a subtractive process, using etchant chemistry to produce complex, high-precision metal parts. In basic metal etching, the metal surface is covered with a special acid-resistant coating, parts of the coating are scraped off by hand or mechanically, and the metal is placed in a bath of strong acid reagent. The acid attacks the metal parts uncovered by the coating, leaving the same pattern as the coating scrapes, and finally removes and cleans the workpiece.
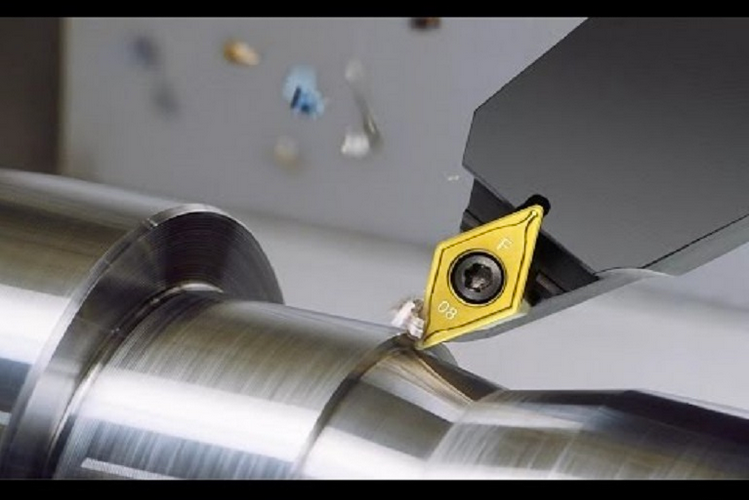
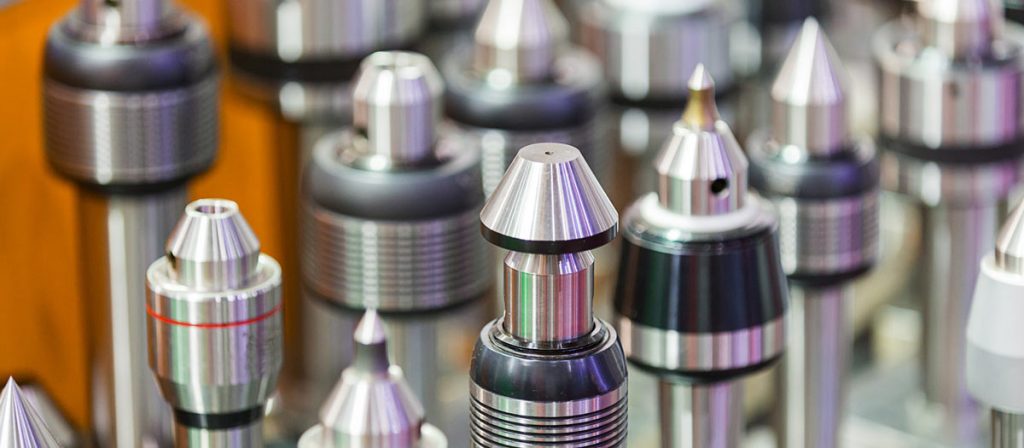
Send your message to us:
-
Aluminum CNC Machining Parts
-
Aluminum Sheet Metal Fabrication
-
Axis High Precision CNC Machining Parts
-
CNC Machined Parts for Italy
-
CNC Machining Aluminum Parts
-
Auto Parts Machining
-
Titanium Alloy Forgings
-
Titanium and Titanium Alloy Fittings
-
Titanium and Titanium Alloy Forgings
-
Titanium and Titanium Alloy Wires
-
Titanium Bars
-
Titanium Seamless Pipes/Tubes
-
Titanium Welded Pipes/Tubes