Titanium Alloy CNC Machining
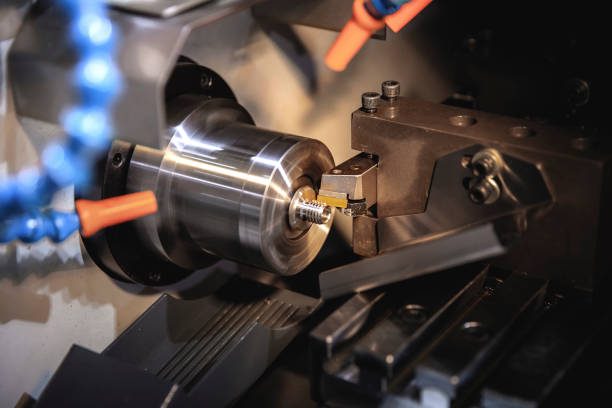
When the hardness of titanium alloy is greater than HB350, cutting is particularly difficult, and when it is less than HB300, it is easy to stick to the knife and it is difficult to cut. Therefore, the titanium processing problem can be solved from the blade. The wear of the insert groove in the machining of titanium alloys is the local wear of the back and front in the direction of the depth of cut, which is often caused by the hardened layer left by the previous machining.
The chemical reaction and diffusion of the tool and the workpiece material at a processing temperature of more than 800 °C are also one of the reasons for the formation of groove wear. Because during the machining process, the titanium molecules of the workpiece accumulate in the front of the blade and are "welded" to the blade edge under high pressure and high temperature, forming a built-up edge.
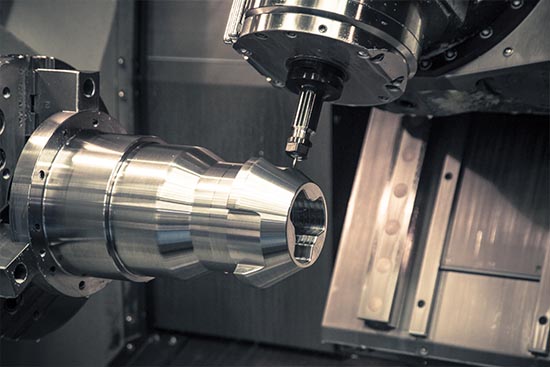
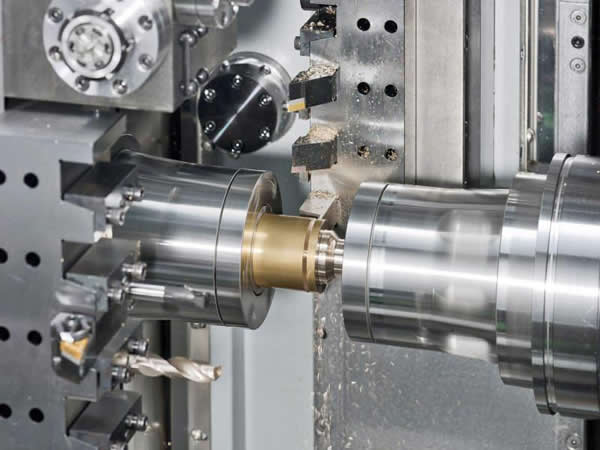
When the built-up edge peels off the cutting edge, it takes away the carbide coating of the insert, so titanium machining requires special insert materials and geometries.
.
It is worth mentioning that since titanium alloys generate high heat during processing, a large amount of high-pressure cutting fluid must be sprayed on the cutting edge in a timely and accurate manner to quickly remove the heat. There are also unique structures of milling cutters specially used for titanium alloy processing on the market today, which are better suited for titanium alloy processing.
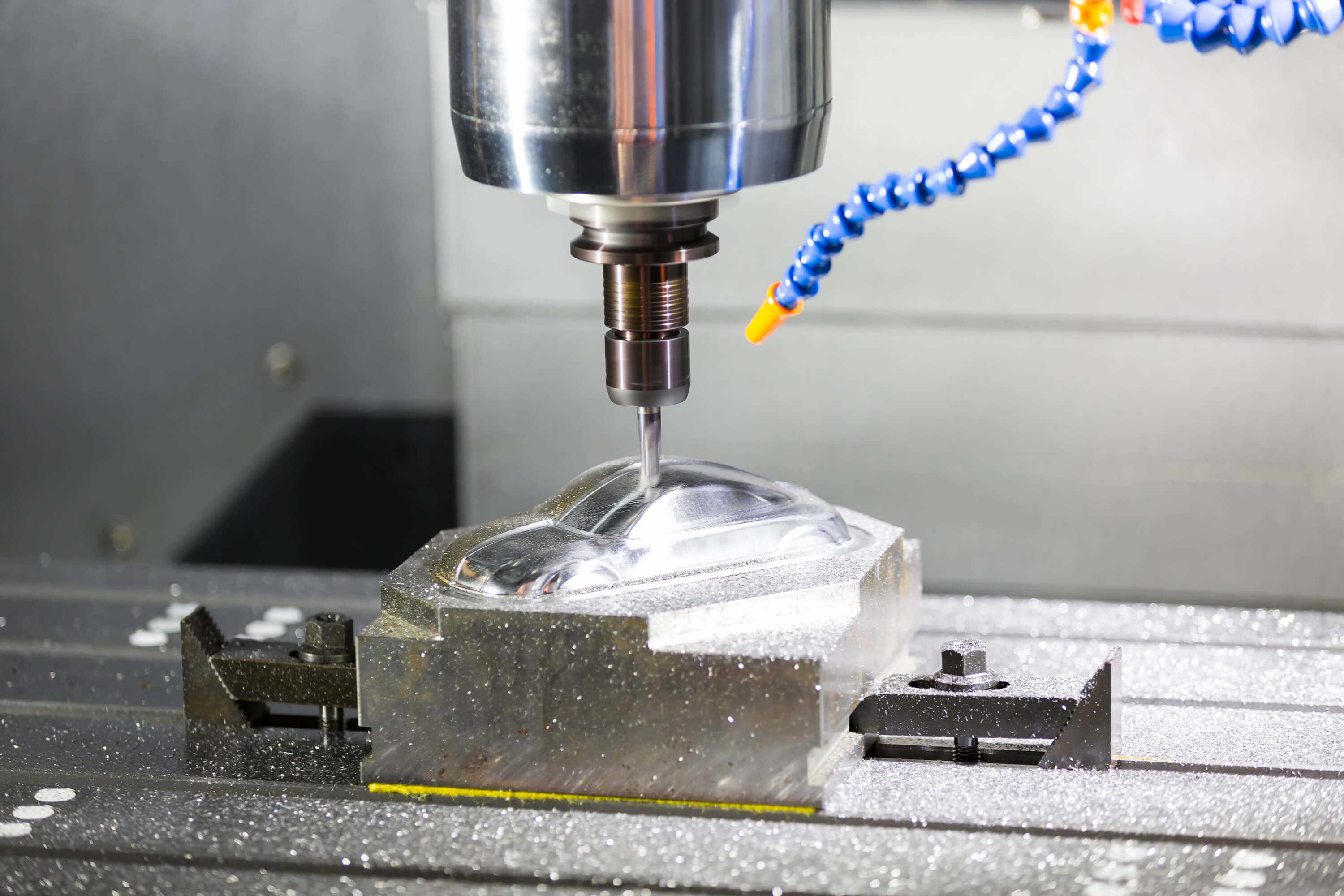
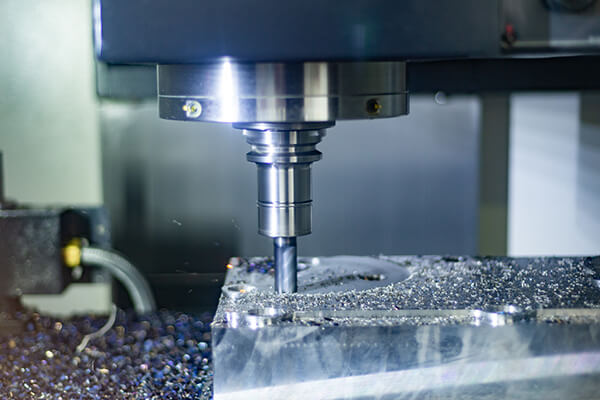
At present, all countries are developing new titanium alloys with low cost and high performance, and strive to make titanium alloys enter the civilian industrial field with huge market potential. my country also spares no effort to move forward in this field.
It is believed that through the joint efforts of all industry professionals, the processing of titanium alloys will no longer be a problem in the future, but will become a sharp blade for the development of my country's manufacturing industry, overcoming obstacles for the development of the entire industry.
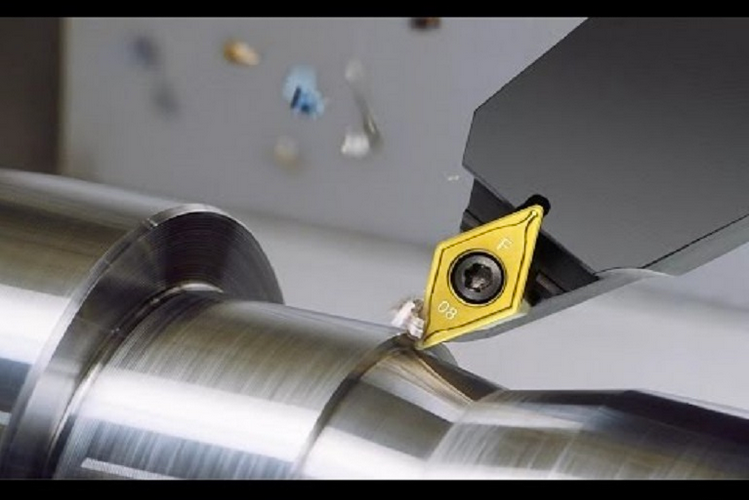
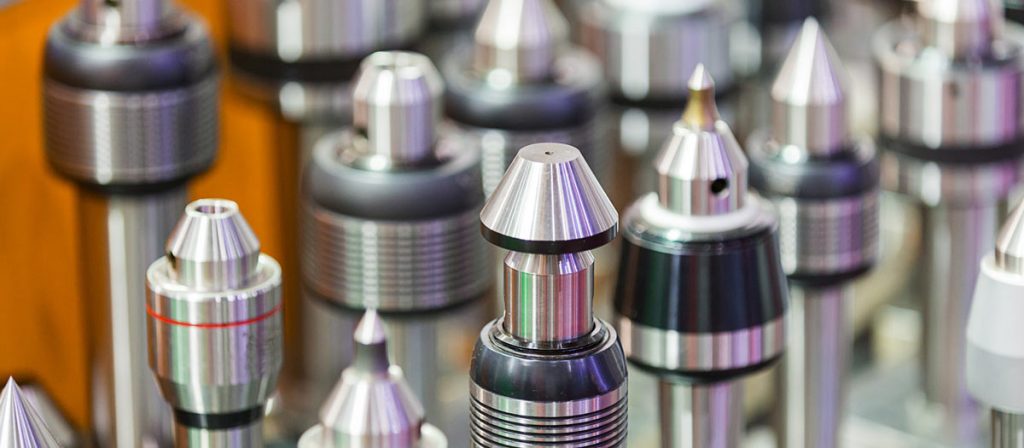
Send your message to us:
-
Aluminum CNC Machining Parts
-
Aluminum Sheet Metal Fabrication
-
Axis High Precision CNC Machining Parts
-
CNC Machined Parts for Italy
-
CNC Machining Aluminum Parts
-
Auto Parts Machining
-
Titanium Alloy Forgings
-
Titanium and Titanium Alloy Fittings
-
Titanium and Titanium Alloy Forgings
-
Titanium and Titanium Alloy Wires
-
Titanium Bars
-
Titanium Seamless Pipes/Tubes
-
Titanium Welded Pipes/Tubes