Overview of CNC Machining Process
Speaking of the numerical control machining process, it is a manufacturing process which utilizes computerized controls to operate the CNC Machines and cutting tools to get the designed parts with metals, plastics, wood or foam, etc. Although the CNC Machining process offers various operations, the fundamental principles of the process are same. The basic CNC machining process includes:
▶ Designing by CAD;
▶ Converting CAD to a CNC Program;
▶ Inputting the program into CNC Machine;
▶ Executing the machine operation;
▶ Getting the designed parts.
Designing by CAD
The CNC machining process begins with 2D or 3D software made by professional designers. CAD, computer-Aided Design, allows the designer and manufacturers to produce the model of their parts according to the technical specifications, including dimensions, technical requirements and designers’ information. Designation of CNC Machined Parts is restricted by the capabilities of CNC Machines and Cutting tooling, and the application of the workpieces. For instance, most of CNC Machine tooling is cylindrical, therefore, the part designed geometries are limited as the tooling creates curved corners. In addition, the materials properties, machine tooling and the capabilities of machine workholding restrict the possibilities of designation, such as the parts minimum thicknesses, maximum parts dimensions, and internal features, etc.
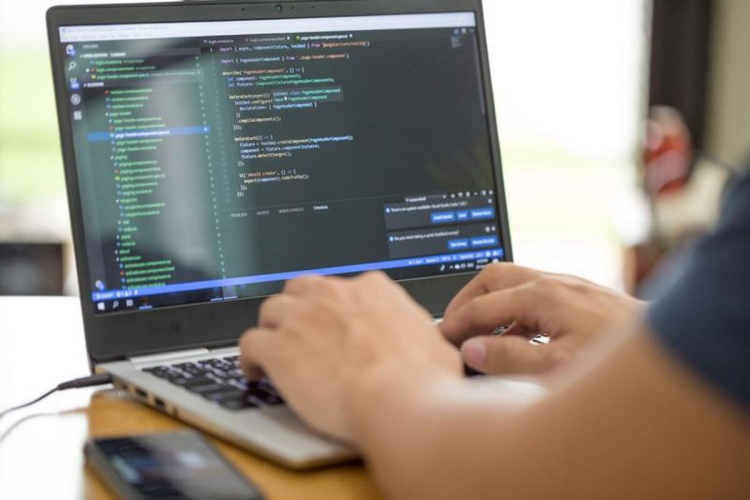
Converting CAD to a CNC Program
Once the CAD design is completed, the designer inputs it to STEP file. The CAD design files works through a program to extract the parts geometries and generates the programming code which will control the machines and tooling to produce the custom designed parts. CNC Machines uses multi programming languages, such as G-code and M-code. G-code is the most well-known programming languages, which controls when, where and how the machine tools move, for example, when the machine turn on or off, how fast to travel to a particular location, which paths to take, etc. M-code controls the auxiliary functions of the machines, such as remove or replace the machine cover when needed automatically. Once the CNC program is generated, the operator loads it to the CNC machine.
Machine Setup
Before the operator runs the CNC program, they must prepare the CNC machine for operation. These preparations include fixing the workpiece on the machine, adjusting machine spindle and machine fixtures. Attaching the required tooling, such as drill bits and end mills, to the proper machine components. Once the machine is completed set up, the operator can run the CNC program.
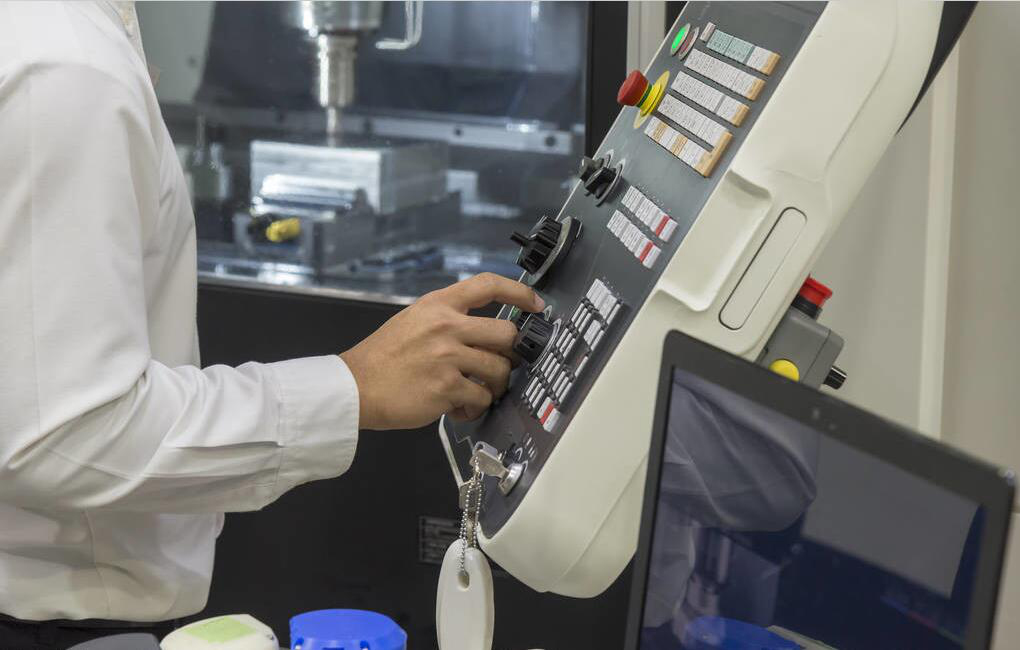
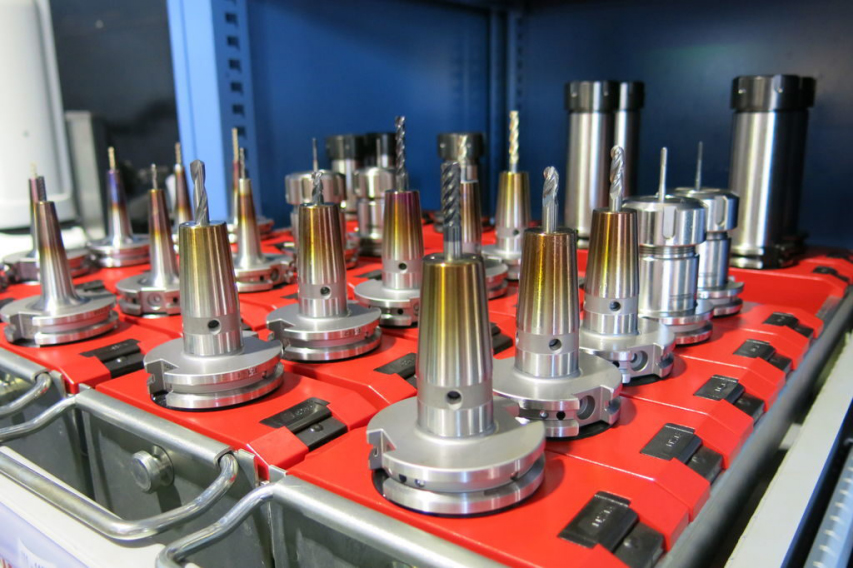
Machining Operation Execution
As the instructions of the CNC Machine, the CNC program submits the commands of tooling actions and movements to the machine’s integrated computer, which operates and manipulates the machine tooling to work on the workpiece. Programs start means the CNC machine starts machining processes, and the program guides the machine throughout the process to produce a custom-designed part. CNC machining processes can be executed in-house if the company has their own CNC equipment—or out-sourced to dedicated CNC machining service providers.
We, BMT, are a dedicated CNC machining service manufacturer, engaging producing high precision machined parts for Industries of Automotive, Food Processing, Industrial, Petroleum, Energy, Aviation, Aerospace, etc. with very tight tolerances and high precision. We actually care about what you need and dedicated to provide the best machining service and parts to your quick turn-around manufacturing requirements.