High Performance Cnc Rapid Prototyping - Modern Machining Parts CNC Machined Part – Basile Detail:
Modern Machining Tools
Metal fabrication processes are often an effective way to generate a given product, however, one needs additional modern tools to achieve a high level of specificity and uniformity. To do so, machining tools can be used to selectively remove or finish a piece of metal or metal-based product. Modern machine tools are traditionally powered by electricity; additional automation of the machining process can be achieved by employing a CNC machine tool, guided by computer programming. The major benefit of modern machining tools is the exceptional uniformity they deliver when manufacturing numerous products with identical parameters and requirements. Many modern machining tools are merely improvements on manual machining tools that have been around for centuries. Other relatively new designs are possible because of recent advancements in technology.
Modern Tools Used in Manufacturing
Today, the most common types of machining and metal fabrication tools can be placed in the following categories:
Lathes
Drilling machines
Milling machines
Hobbing machines
Honing machines
Gear shapers
Planer machines
Grinding machines
Broaching machines
A lathe consists of a rotating work-piece upon which the workable object (in this case, metal) is placed—the result is the symmetrical and specific shaping of the product. As the product rotates, various tools are used to cut, knurl, drill or otherwise alter the metal. The friction of the rotation causes provides a simple mechanism for delivering a uniform effect around the entire circumference of an object, making lathes a good choice for products that are symmetric around an axis of rotation. Lathes vary in size, with the smallest being handheld versions used for jewelry and watchmaking.
Drilling machines, also called drill presses, consist of a fixed drill that is mounted or bolted to a stand or workbench. Drill presses are used in much the same way as handheld and power drills, however, the stationary nature of drill presses requires less exertion to achieve proper drilling and is much more stable. Factors such as the angle of the drill spindle can be fixed and maintained to allow for repeated and consistent drilling. Modern types of drilling machines include pedestal drills, bench drills, and pillar drills.
Similar to drilling machines, milling machines use a stabilized rotating cutter to machine a piece of metal, but allow more versatility by additionally performing sideways cuts. Some modern milling machines have a mobile cutter, while others have a mobile table that moves about a stationary cutter to complete the desired finishing effect. Common types of milling machines include hand milling machines, plain milling machines, universal milling machines and universal milling machines. All types of milling machines are available in vertical and horizontal configurations.
A hobbing machine is similar to a milling machine in that a rotating cutter performs the cutting action, however, they allow for simultaneous movement of both the cutter and the product being machined. This unique capability makes hobbing ideal for 3D machining applications that require uniform tooth profiles. Gear cutting is one of the most common applications for modern hobbing machines.
Honing machines, also known as hones, consist largely of one or more rotating tips that, in metalworking, enlarge holes to a precise diameter and improve surface finish. Types of honing machines include handheld, manual and automatic. Products manufactured with the help of honing include engine cylinders.
Whereas a hobbing machine cuts the external teeth of a gear, modern gear shapers fabricate internal gear teeth. This is accomplished using a reciprocating cutter that has the same pitch as the gear being cut. Modern gear shapers allow for increased precision by employing forward stroke engagement and backward stroke disengagement.
Planers are large-sized shaping machines that move the actual metal product as opposed to moving the cutting mechanism. The result is similar to that of a milling machine, making planers ideal for shaping flat or long surfaces. Modern milling machines are somewhat superior to planers in most applications; however, planers are still beneficial when extremely large metal components require squaring off.
Grinders are modern machining tools that use an abrasive wheel to create fine finishes or faint cuts. Depending on the specific grinder, the abrasive wheel or product is moved from side to side to achieve the desired finish. Types of grinders include belt grinders, bench grinders, cylindrical grinders, surface grinders, and jig grinders.
A broaching machine, or broach, uses tall chisel points to apply linear shearing and scraping motions to the given material. Broaches are often used to create non-circular shapes out of holes that have been previously punched in the metal. They also cut splines and keyways on gears and pulleys. Rotary broaches are a unique subsection of broaching machines, used in conjunction with a lathe to create a simultaneous horizontal and vertical cutting motion.
Product detail pictures:
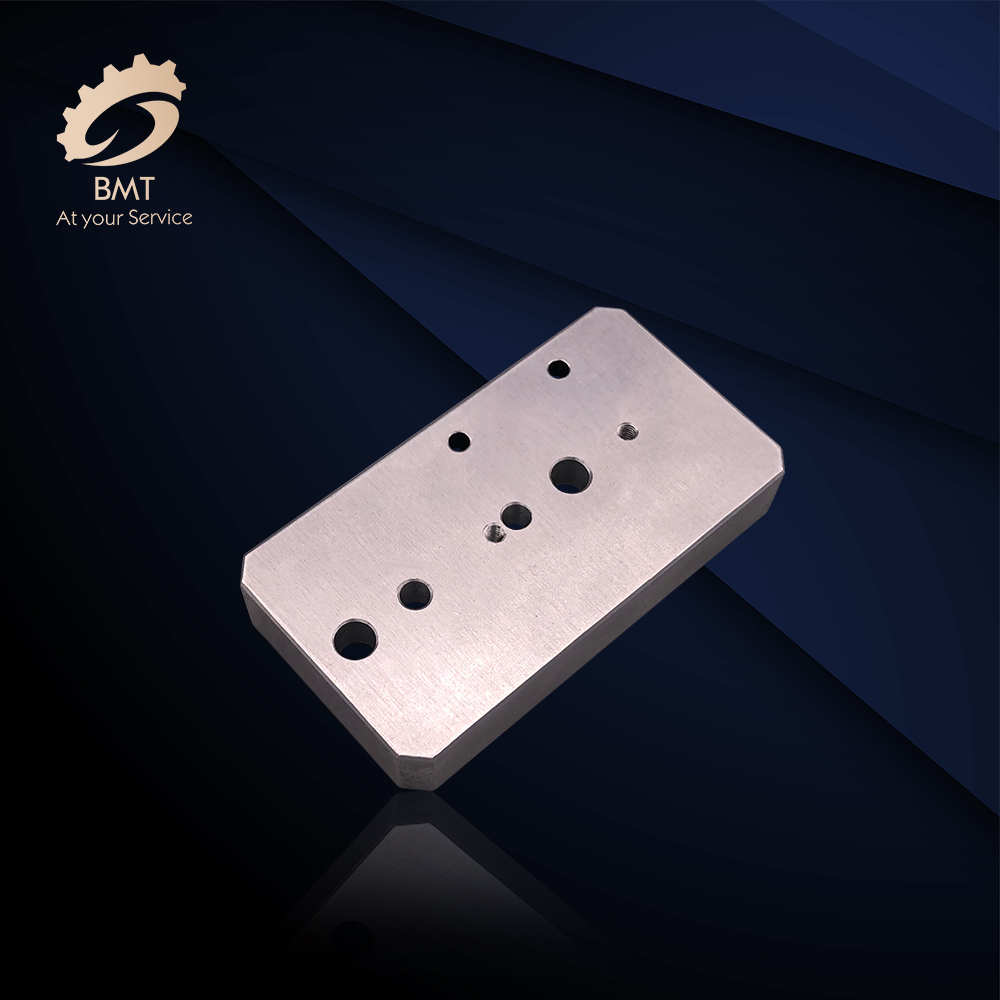
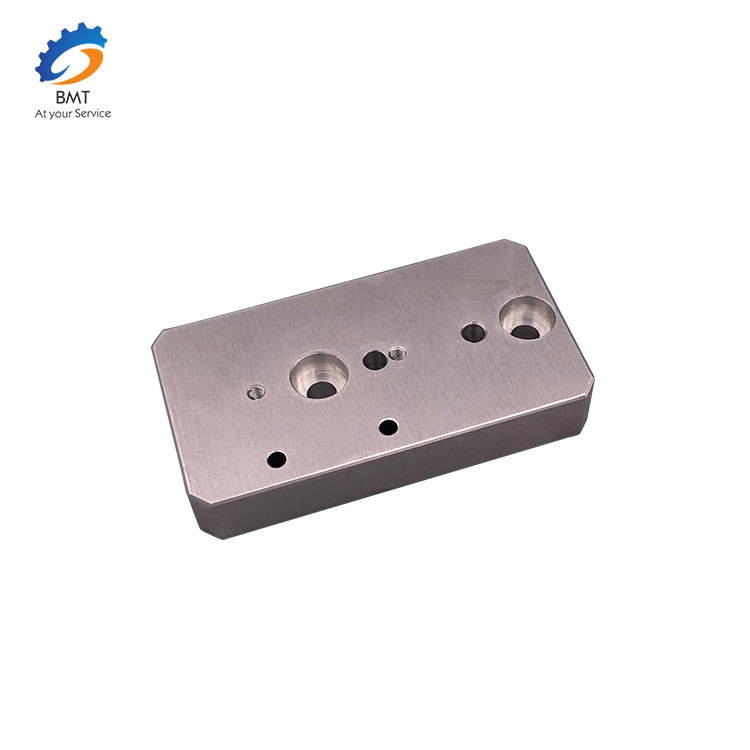
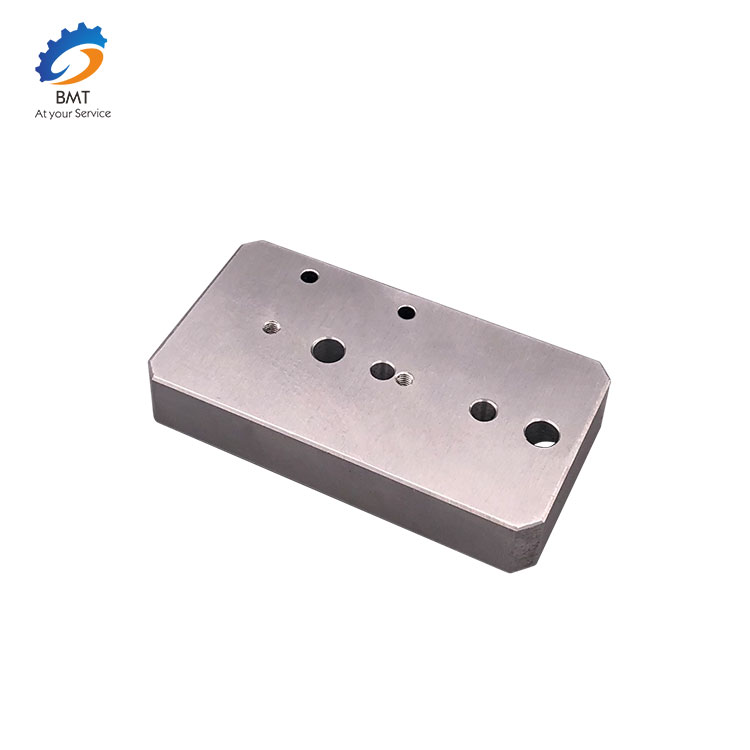
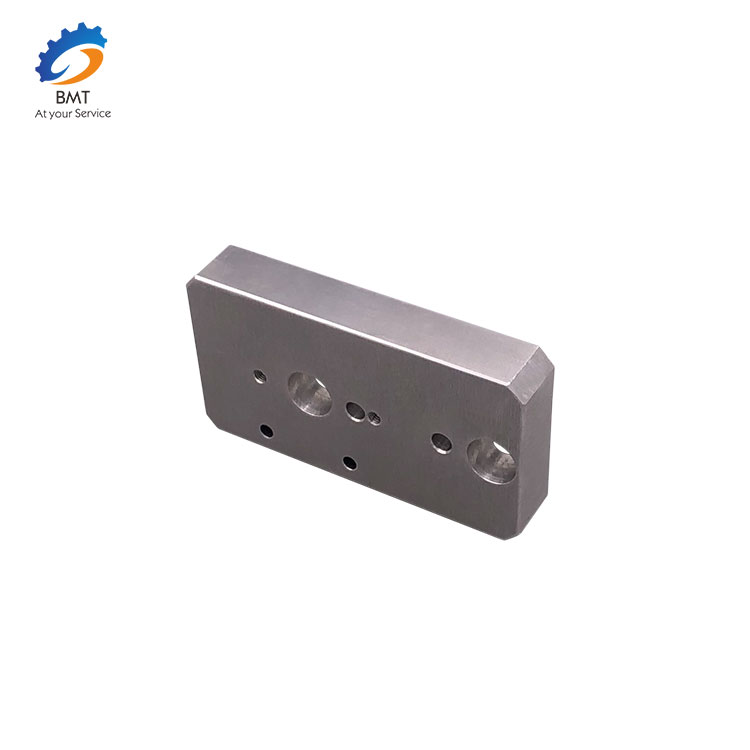
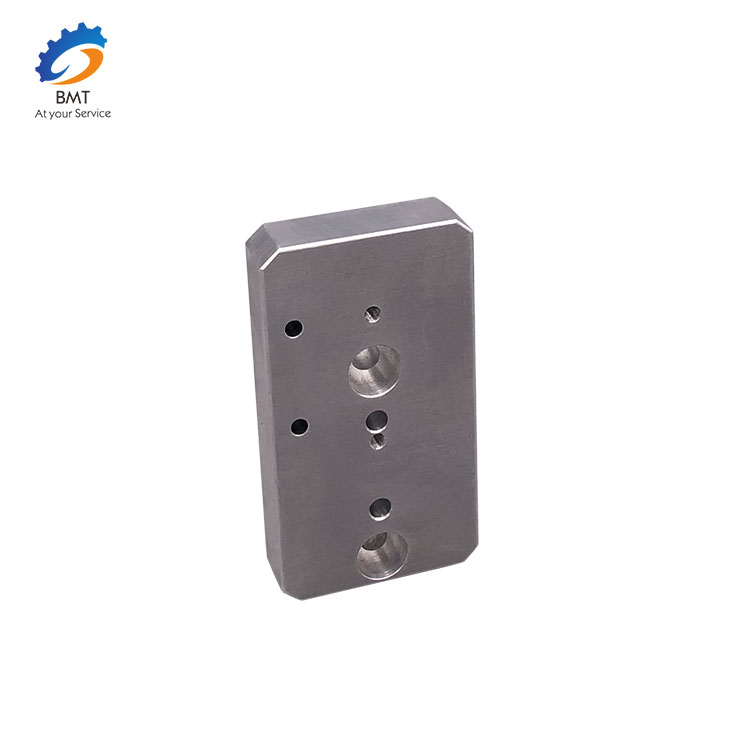
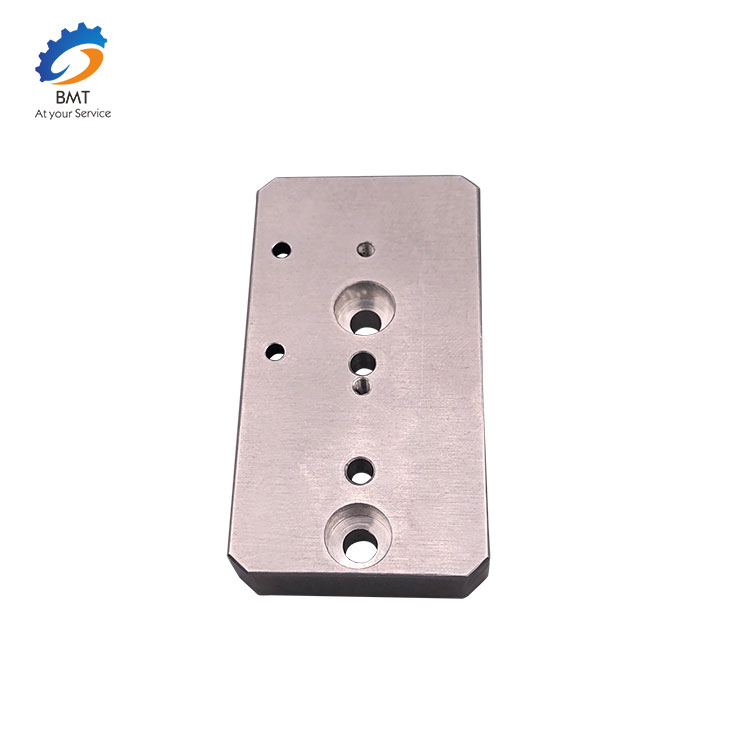
Related Product Guide:
The shopper satisfaction is our primary focus on. We uphold a consistent level of professionalism, quality, credibility and repair for High Performance Cnc Rapid Prototyping - Modern Machining Parts CNC Machined Part – Basile, The product will supply to all over the world, such as: Saudi Arabia, Ethiopia, Brazil, We warmly welcome you to come to visit us personally. We hope to establish a long-term friendship based on equality and mutual benefit. If you want to get in touch with us, please do not hesitate to call. We will be your best choice.

It's really lucky to find such a professional and responsible manufacturer, the product quality is good and delivery is timely, very nice.
