High Quality Custom Precision Machining - Features of Milling Cutters – Basile Detail:
Features of Milling Cutters
When dealing with difficult-to-machine materials such as Hastelloy, waspaloy, Inconel and Kovar, machining knowledge and experience is very important. At present, there are more and more applications of nickel-based alloys, mainly used to manufacture some important parts in aerospace, medical and chemical industries. These materials have high strength, corrosion resistance, and can withstand extremely high temperatures. Some special elements are added to the above materials to obtain superior performance. On the other hand, however, these materials also become particularly difficult to mill.
We know that nickel and chromium are the two main additives in nickel-based alloys. Adding nickel can increase the toughness of the material, adding chromium can improve the hardness of the material, and the balance of other components can be used to predict the wear of the tool. Other elements added to the material may include: silicon, manganese, molybdenum, tantalum, tungsten, etc. It is worth noting that tantalum and tungsten are also the main components used to make cemented carbide, which can effectively improve the performance of cemented carbide , but the addition of these elements to the workpiece material makes it difficult to mill, almost like cutting one carbide tool with another.
Why do milling cutters cutting other materials break faster when milling nickel-based alloys? It is important to understand this. Machining nickel-based alloys, the tool cost is high, and the cost is 5 to 10 times that of milling general steel.
Needless to say, heat is the most important factor affecting tool life when milling nickel-based alloys, because even the best carbide tools can be destroyed by excessive cutting heat. The generation of extremely high cutting heat is not just a problem for milling nickel alloys. So when milling these alloys, heat needs to be controlled. In addition, it is very important to know the heat value generated when machining with various types of tools (high-speed steel tools, carbide tools or ceramic tools).
Many tool damage is also related to other factors, and substandard fixtures and tool holders can shorten tool life. When the rigidity of the clamped workpiece is insufficient and movement occurs during cutting, it may cause the fracture of the cemented carbide matrix. Sometimes small cracks develop along the cutting edge, and sometimes a piece breaks off the carbide insert, making it impossible to continue cutting. Of course, this chipping can also be caused by too hard carbide or too much cutting load. At this time, high-speed steel tools should be considered for processing to reduce the occurrence of chipping. Of course, high-speed steel tools cannot withstand higher heat like cemented carbide. Exactly what material to use must be determined on a case-by-case basis.
Product detail pictures:


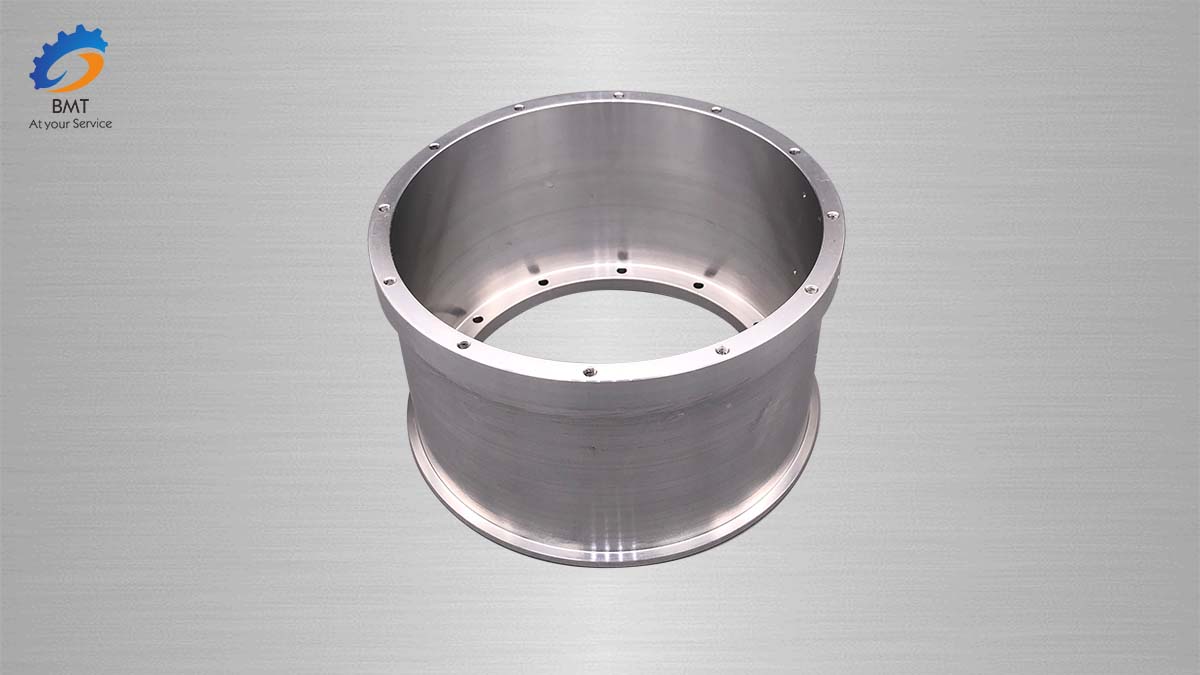



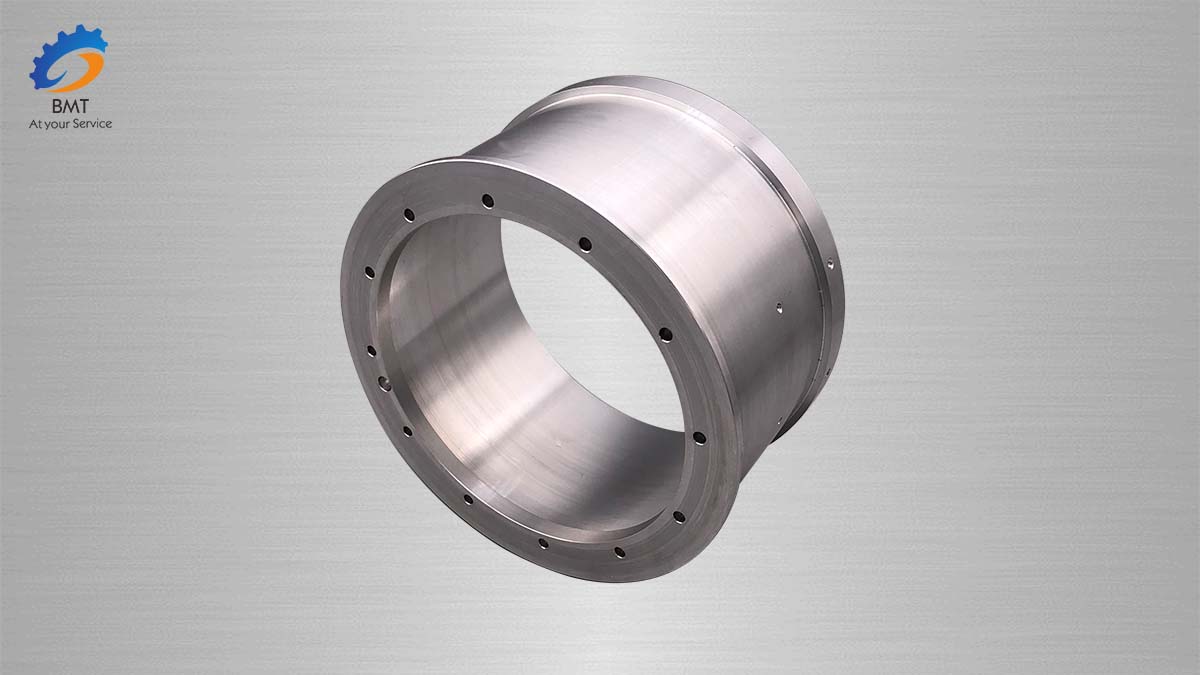

Related Product Guide:
"Sincerity, Innovation, Rigorousness, and Efficiency" will be the persistent conception of our company to the long-term to establish together with customers for mutual reciprocity and mutual gain for High Quality Custom Precision Machining - Features of Milling Cutters – Basile, The product will supply to all over the world, such as: Tanzania, Egypt, Japan, We are seeking the chances to meet all the friends from both at home and abroad for the win-win cooperation. We sincerely hope to have long-term cooperation with all of you on the bases of mutual benefit and common development.

Goods just received, we are very satisfied, a very good supplier, hope to make persistent efforts to do better.

Send your message to us:
-
Factory making Cnc Milling Companies - Custom ...
-
OEM China China Cnc Parts - Aluminum CNC Machi...
-
2021 Good Quality Ames Sheet Metal - Precision...
-
Good User Reputation for Cnc Machining Companie...
-
Lowest Price for Brass And Aluminum Cnc Machini...
-
Best Price for Car Seat Parts - Customized Sta...