
In the world of manufacturing, the ability to machine parts from a variety of materials is crucial for producing high-quality products. From metals to composites, the demand for precision machining of different materials has led to significant advancements in machining technology. One of the key challenges in machining different materials is the varying properties of each material. Metals such as aluminum, steel, and titanium require different machining techniques due to their hardness, ductility, and thermal conductivity. Similarly, composites like carbon fiber and fiberglass present their own set of challenges with their abrasive nature and tendency to delaminate during machining.
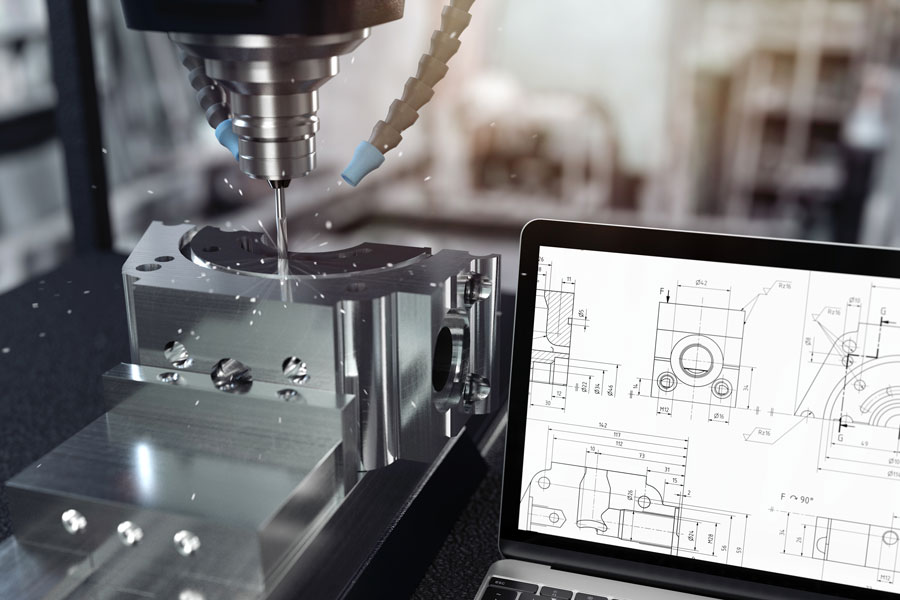
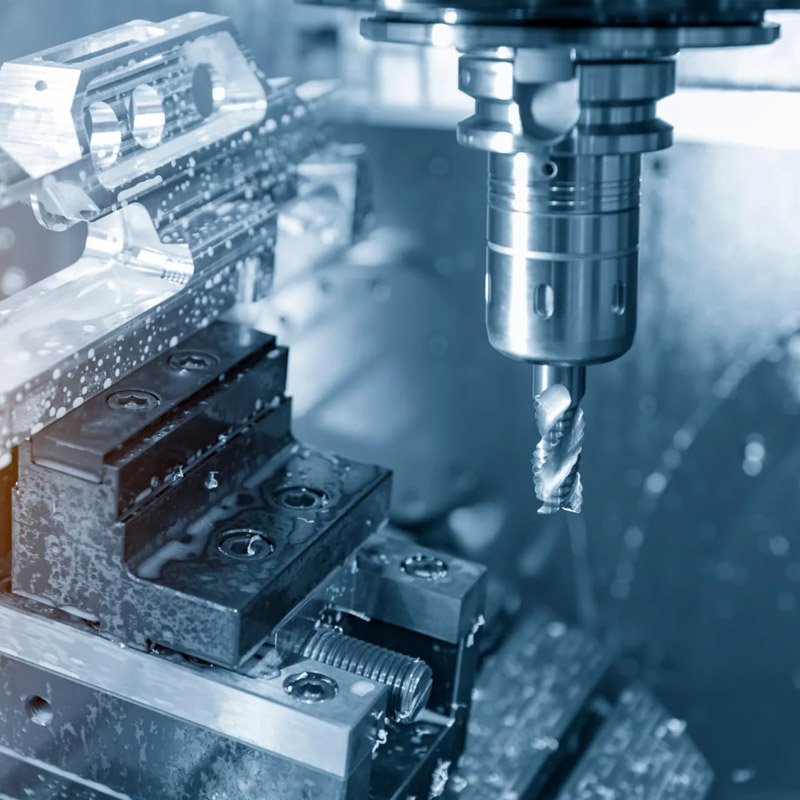
To address these challenges, manufacturers have been investing in advanced machining technologies that can handle a wide range of materials with precision and efficiency. One such technology is multi-axis CNC machining, which allows for complex geometries and tight tolerances to be achieved across different materials. By using advanced cutting tools and toolpath strategies, CNC machining has become a versatile solution for machining parts from metals, composites, and even exotic materials like ceramics and super alloys. In addition to CNC machining, advancements in cutting tool materials have also played a significant role in machining different materials. High-speed steel (HSS) and carbide tools have been the traditional choice for machining metals, but the rise of ceramic and diamond-coated tools has expanded the capabilities of machining to include hard and abrasive materials.
These advanced cutting tools offer improved wear resistance and thermal stability, allowing for higher cutting speeds and longer tool life when machining materials like Inconel, hardened steel, and carbon composites. Furthermore, the integration of additive manufacturing with traditional machining processes has opened up new possibilities for producing parts from a variety of materials. Hybrid manufacturing systems, which combine 3D printing with CNC machining, have enabled the production of complex, high-performance parts with tailored material properties. This approach has been particularly beneficial for industries such as aerospace and automotive, where lightweight, high-strength materials are in high demand.
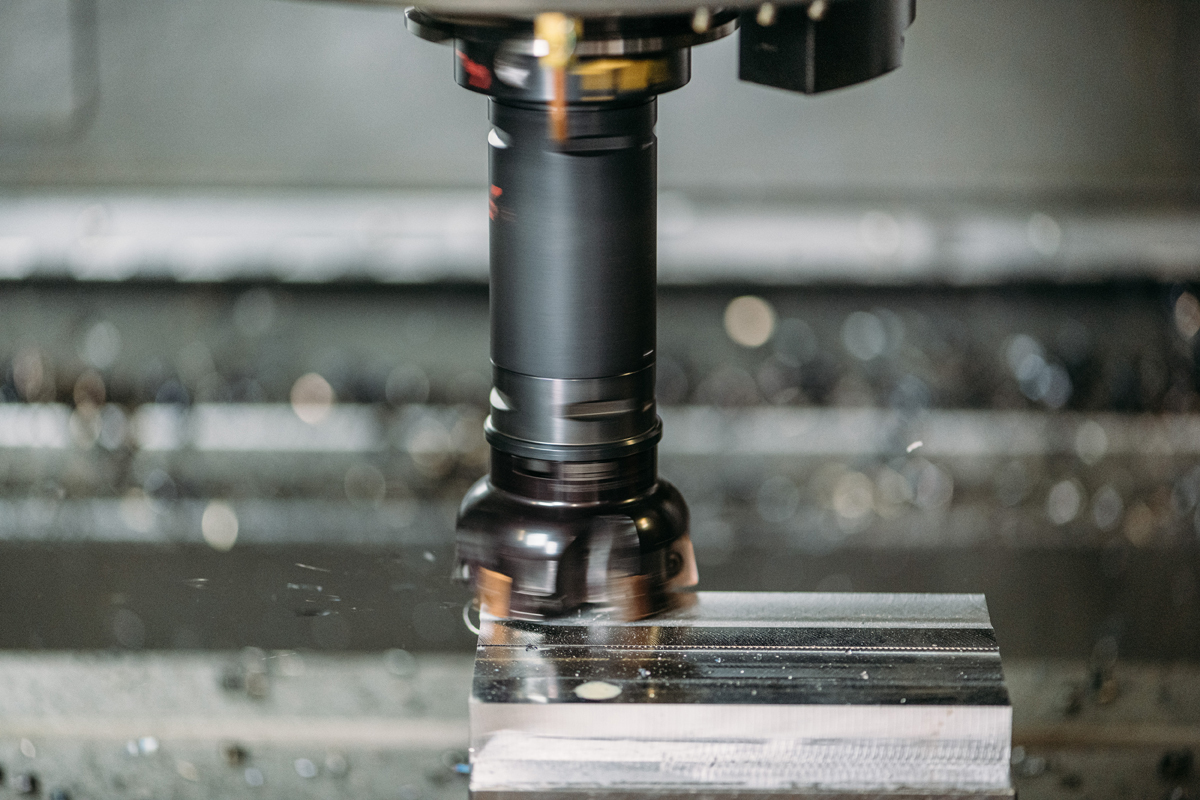
The advancements in machining technology for different materials have also been driven by the growing need for sustainable manufacturing practices. With the focus on reducing material waste and energy consumption, machining processes have evolved to be more efficient and environmentally friendly. For instance, the use of high-pressure coolant systems and minimum quantity lubrication has improved chip evacuation and reduced the consumption of cutting fluids, leading to a more sustainable machining process. Moreover, the adoption of digital manufacturing technologies, such as simulation software and real-time monitoring systems, has enhanced the predictability and control of machining processes for different materials. By simulating the machining of various materials, manufacturers can optimize tool path strategies and cutting parameters to minimize tool wear and maximize productivity.
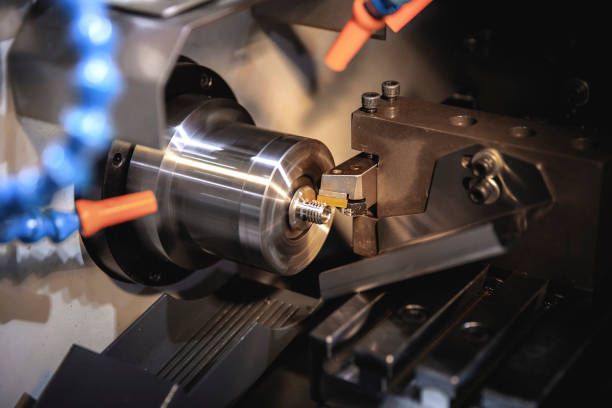
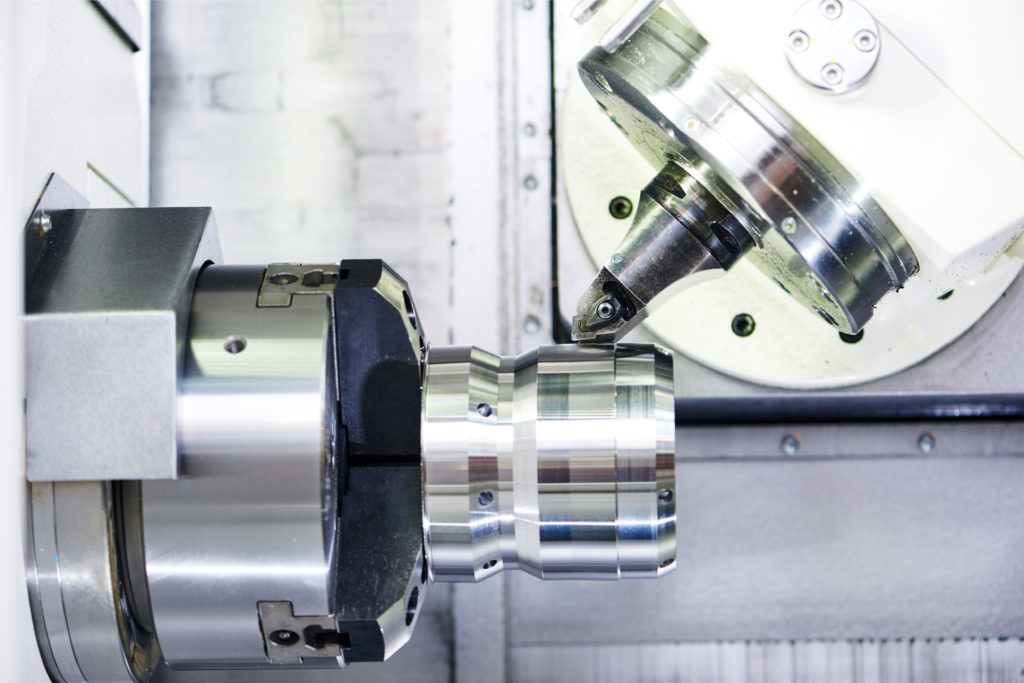
Real-time monitoring systems provide valuable insights into tool condition and process stability, allowing for proactive maintenance and quality assurance during machining operations. In conclusion, the advancements in machining technology for different materials have revolutionized the manufacturing industry, enabling the production of high-quality parts with greater precision, efficiency, and sustainability. With the continued development of multi-axis CNC machining, advanced cutting tools, hybrid manufacturing, and digital manufacturing technologies, manufacturers are well-equipped to meet the demands of machining parts from a diverse range of materials. As the industry continues to evolve, the integration of new materials and technologies will further expand the possibilities for machining, driving innovation and progress in manufacturing.
Post time: May-06-2024