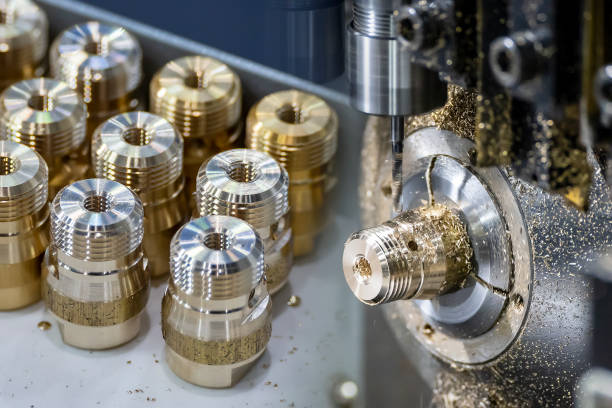
In today's rapidly evolving technological world, precision and accuracy are crucial across industries. One technological advance that has contributed greatly to this is computer numerical control (CNC) machining. The implementation of CNC machining technology has revolutionized the production of complex, high-quality and precision parts. This article explores the importance of CNC machined parts in various fields and their role in shaping the future of manufacturing. CNC machining provides unparalleled precision through its automated process. A computer program controls the machine, ensuring always accurate measurements and minimizing human error. With comprehensive 3D modeling software, engineers can design complex parts with virtual precision and then use CNC machines to transform them into physical components. This level of accuracy is critical for industries such as aerospace, automotive, medical and defense.
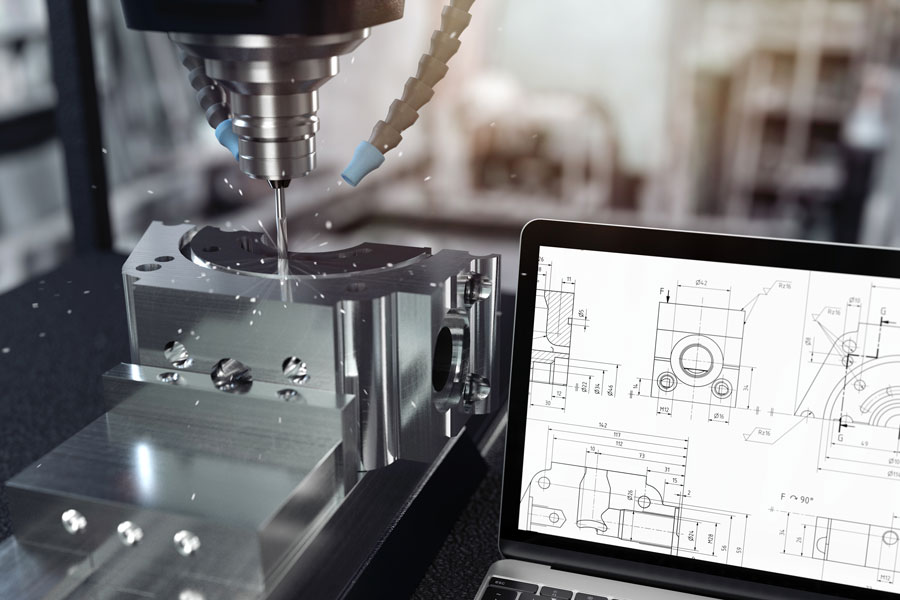
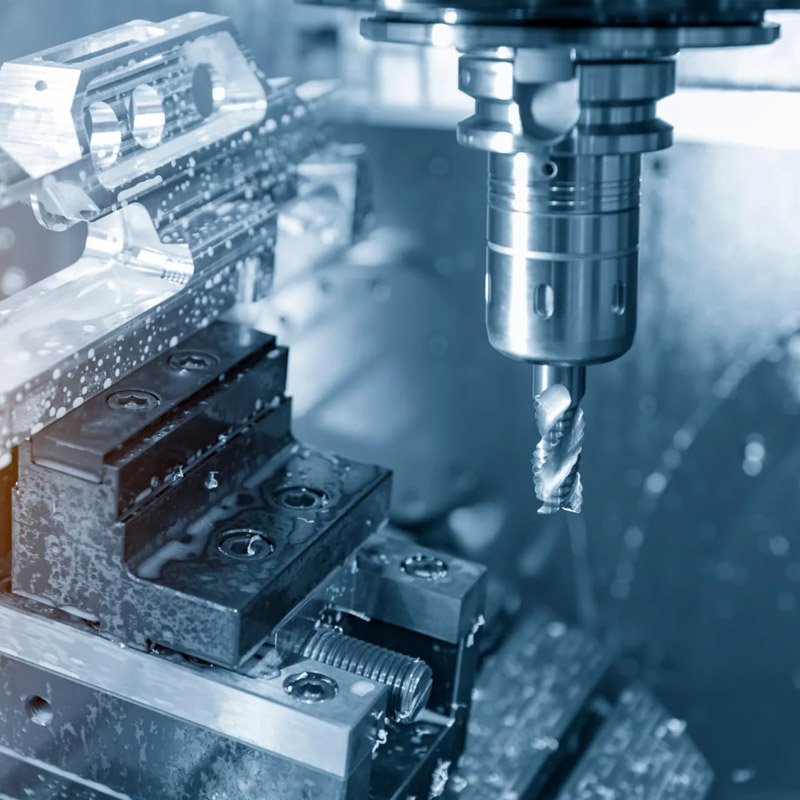
CNC machined parts are used in various industries due to their versatility. In the aerospace sector, CNC machined components are used to produce aircraft engines, hydraulic systems and landing gear. Likewise, the automotive industry relies on CNC machined parts to manufacture critical components such as engines, transmissions, and suspensions. Medical devices and orthopedic implants also rely heavily on CNC machining to produce precision and custom parts. The CNC machining process guarantees excellent quality due to its excellent repeatability and consistency. Once a design is programmed, the CNC machine can replicate the same part repeatedly with precise accuracy. This aspect ensures quality consistency throughout the production process, reducing the risk of defective or substandard products. Additionally, CNC machines operate efficiently, thereby reducing material waste and optimizing production time.
Time-consuming manual labor is eliminated, increasing productivity and cost-effectiveness. With advanced multi-axis machining capabilities, complex parts that were previously nearly impossible to manufacture manually can now be produced seamlessly. The adoption of CNC machined parts is in line with the concept of Industry 4.0, the fourth industrial revolution characterized by automation and interconnection. CNC machine tools integrate Internet of Things capabilities to enable real-time monitoring, maintenance prediction, and data analysis. This connectivity increases productivity, streamlines operations and drives innovation in manufacturing. CNC machined parts contribute to sustainable manufacturing practices. With their precision and efficiency, CNC machine tools significantly reduce material waste and minimize the consumption of natural resources.
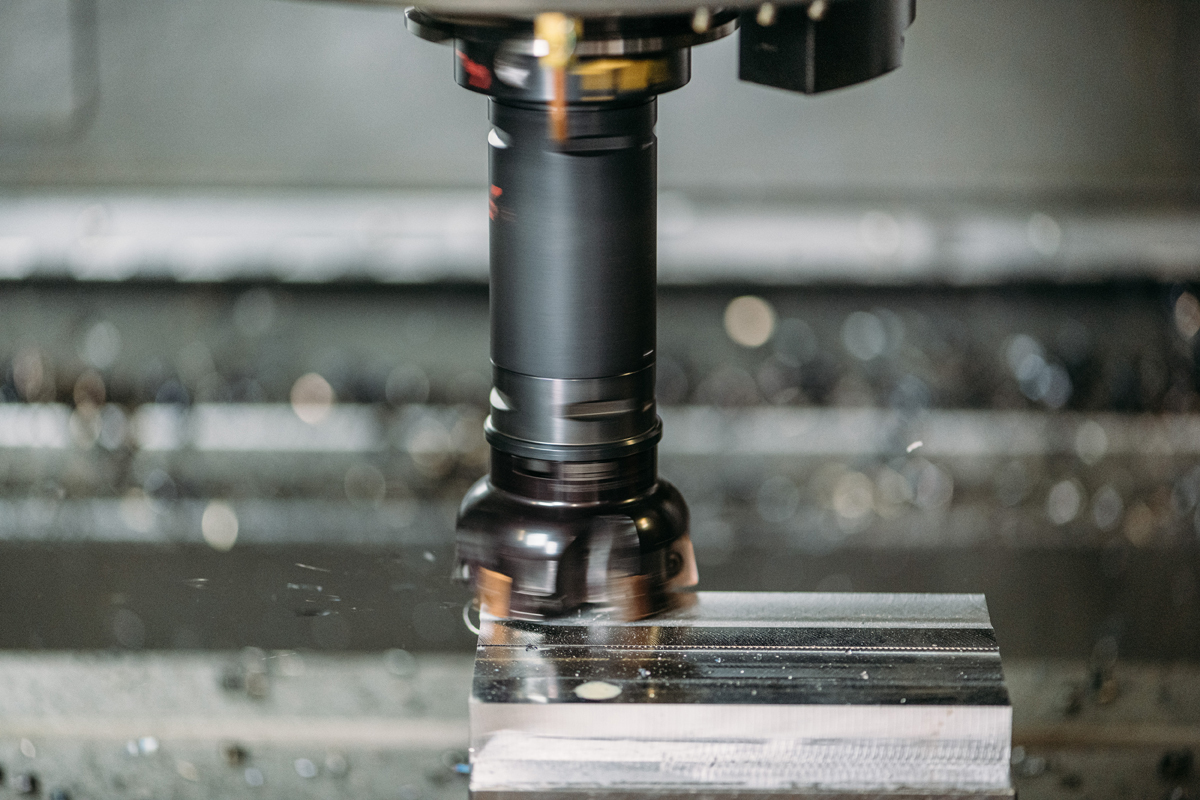
In addition, the automation and simplification of manufacturing processes can save energy and reduce carbon emissions, promoting a green environment. CNC machining has come a long way over the years and continues to improve. The continued development of new materials and the integration of artificial intelligence and robotics are pushing the boundaries of precision manufacturing. Industries are increasingly relying on CNC machined parts to meet the growing demand for high-quality, customizable components. However, challenges remain, such as the high initial investment cost of CNC machine tools, which limits their use by small manufacturers. Addressing these barriers and ensuring widespread adoption of CNC machining technology is critical to unlocking the full potential of precision manufacturing.
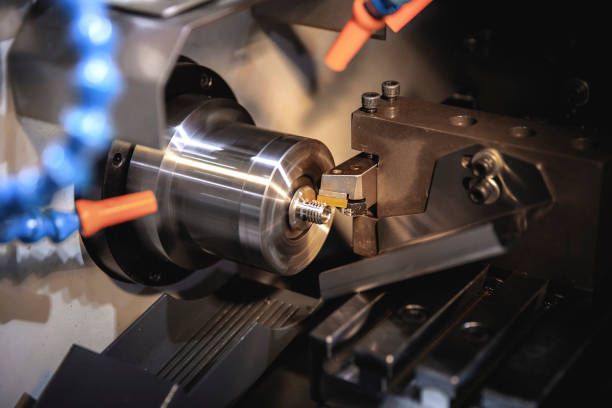
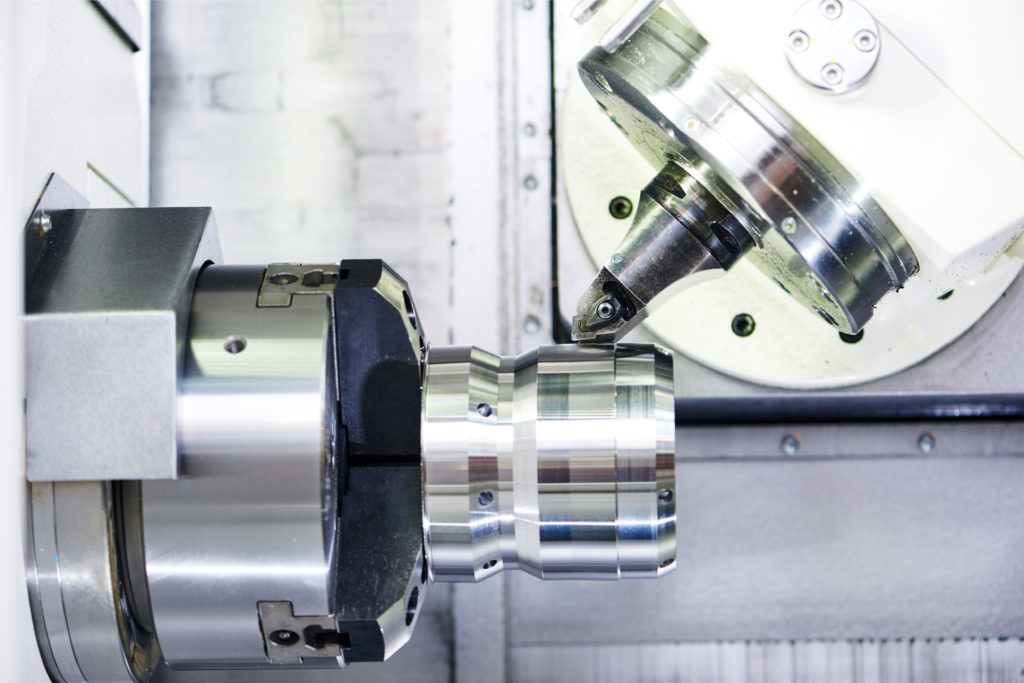
CNC machined parts have revolutionized the way manufacturing is done across different industries, providing unparalleled precision, versatility and efficiency. Their contribution to the production of quality components cannot be underestimated. With the continuous advancement of technology and reduction of costs, CNC machining will become an indispensable aspect of modern manufacturing. Embracing this technology will undoubtedly reshape the industry, drive innovation, reduce waste, and set new standards for precision manufacturing in the future.
Post time: Sep-19-2023