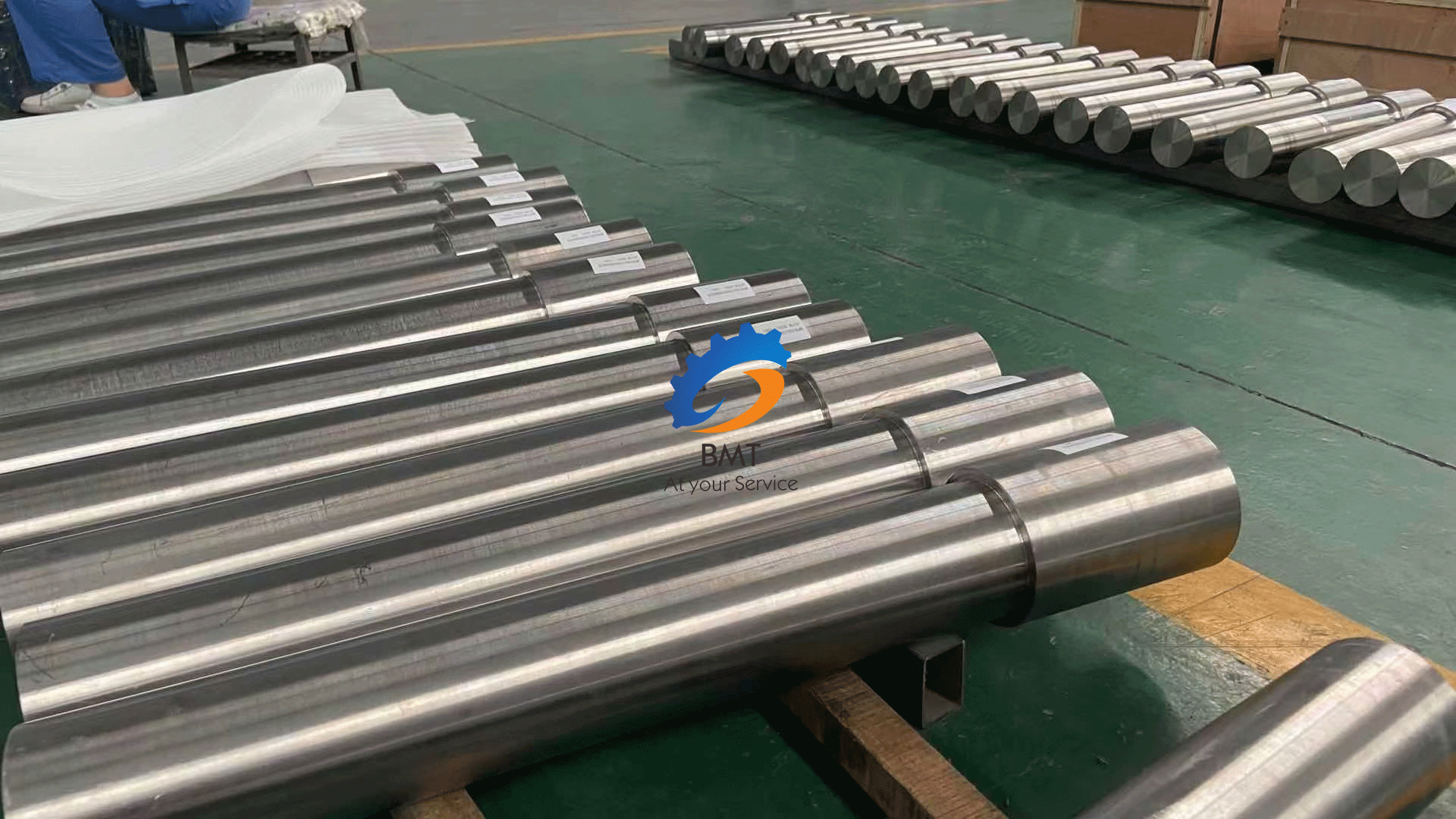
In the constantly evolving field of manufacturing, CNC titanium machining parts have emerged as the new benchmark for strength and precision. As industries such as aerospace, automotive, and medical push the boundaries of innovation, the demand for high-quality titanium components has surged. CNC machining, along with titanium's exceptional properties, provides engineers with endless possibilities for creating complex and durable parts. Titanium, renowned for its exceptional strength-to-weight ratio, corrosion resistance, and biocompatibility, has become the material of choice for industries where reliability and performance are paramount.
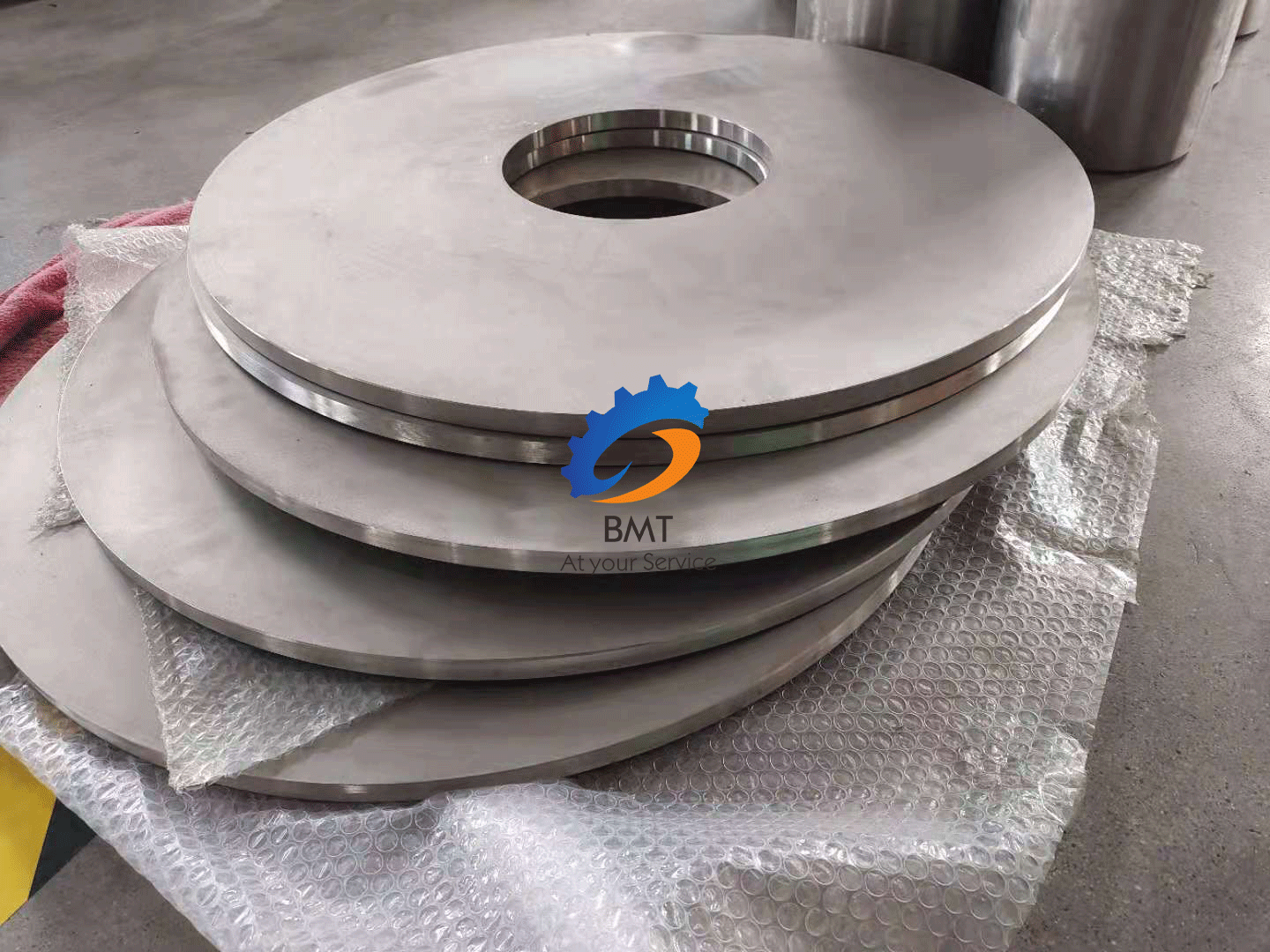
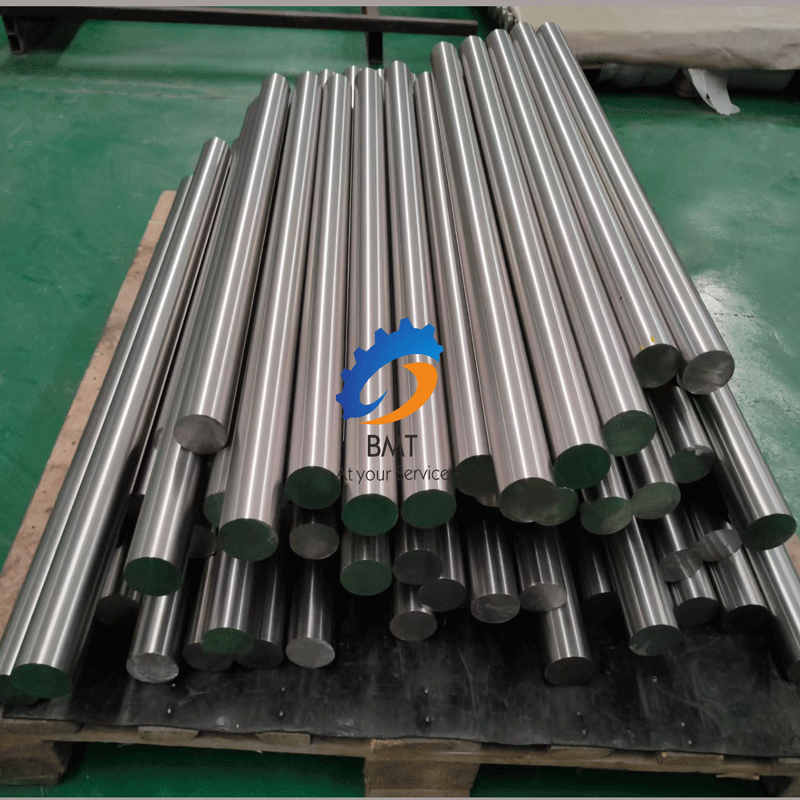
However, machining titanium is notoriously challenging due to its low thermal conductivity and high reactivity with cutting tools. This is where CNC (Computer Numerical Control) machining comes into play. CNC machining is a computer-controlled manufacturing process that allows for precise and repeatable production of intricate parts. By utilizing advanced software and automated machinery, CNC machining provides unparalleled accuracy and efficiency that surpasses conventional machining methods. Combined with titanium, CNC machining facilitates the production of complex, high-performance components that meet the stringent requirements of modern industries.
One of the key advantages of CNC titanium machining parts is the ability to produce custom parts with intricate designs and complex geometries. With CNC technology, manufacturers can turn complex 3D CAD models into reality, creating parts with precise tolerances and intricate details. This enables engineers to explore new possibilities in product design and develop cutting-edge solutions that were once thought to be unattainable. Additionally, CNC titanium machining parts offer exceptional strength and durability. Titanium's high strength-to-weight ratio makes it ideal for applications where weight reduction is crucial without compromising structural integrity. Whether its aerospace components subjected to extreme temperatures and stress or medical implants requiring biocompatibility and long-term reliability, CNC titanium machining parts provide a winning combination of strength and performance.
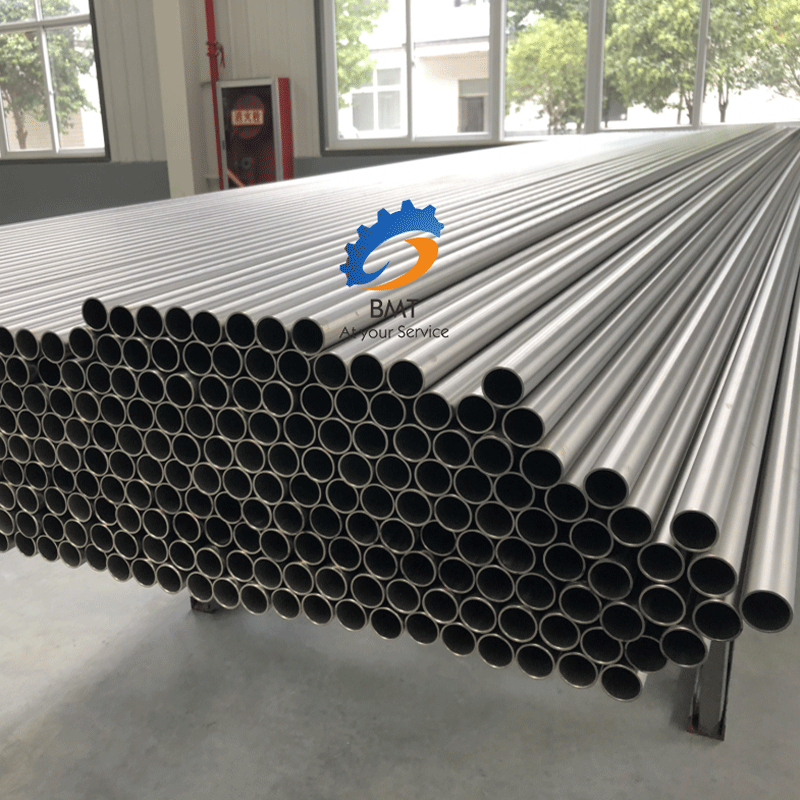
Moreover, CNC machining ensures consistent quality and improved productivity. Traditional machining methods are often time-consuming, requiring manual operation and frequent tool changes. CNC machines, on the other hand, minimize human error and reduce production time by enabling simultaneous operation of multiple axes and tools. This not only boosts productivity but also guarantees consistent quality, as each part is manufactured with precision and repeatability. With the increasing demand for titanium components, manufacturers have invested in state-of-the-art CNC machines specifically designed for machining titanium. These machines feature robust structures, high-performance spindle systems, and advanced cooling techniques to mitigate the challenges associated with machining titanium.
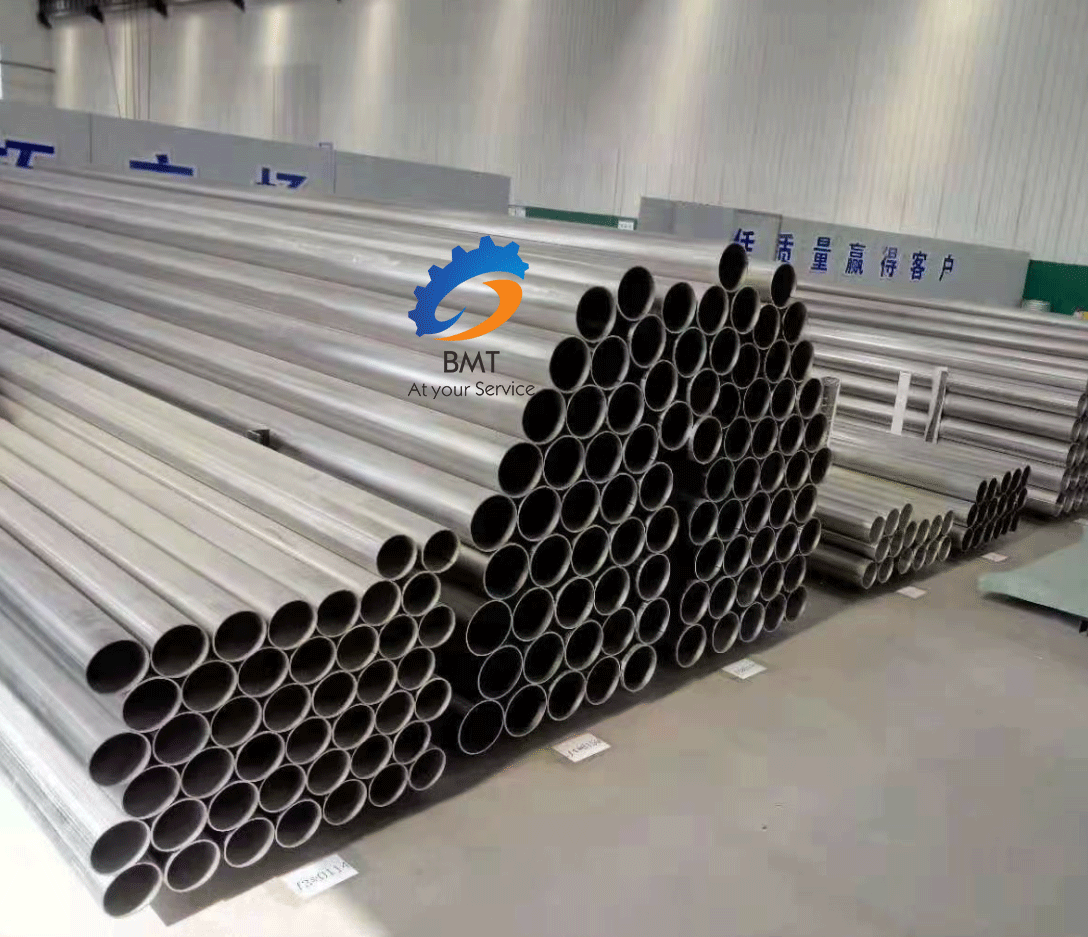
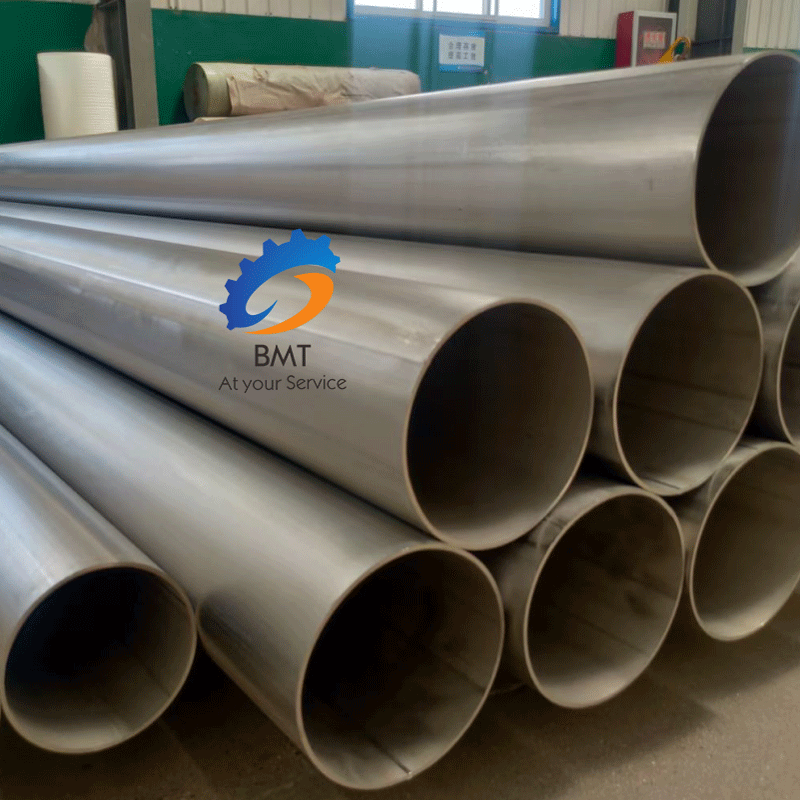
Combined with skilled operators and in-depth knowledge of titanium's properties, manufacturers can achieve exceptional results in terms of both quality and efficiency. In conclusion, CNC titanium machining parts represent the epitome of strength and precision in the manufacturing industry. Thanks to CNC machining technology, engineers can push the boundaries of design and create intricate, custom parts that meet the rigorous demands of modern industries. With titanium's exceptional properties and CNC's accuracy and efficiency, the possibilities for innovation are endless. As the demand for high-quality titanium components continues to grow, the future of CNC titanium machining parts looks promising, promising a world of strength, reliability, and unrivaled performance.
Post time: Sep-05-2023