Injection Moulding Gate
It is the channel connecting the main runner (or branch runner) and the cavity. The cross-sectional area of the channel can be equal to the main flow channel (or branch channel), but it is usually reduced. So it is the smallest cross-sectional area in the entire runner system. The shape and size of the gate have a great influence on the quality of the product.
The role of the gate is:
A. Control the material flow speed:
B. It can prevent backflow due to the premature solidification of the melt stored in this part during injection:
C. The passing melt is subjected to strong shear to increase the temperature, thereby reducing the apparent viscosity and improving the fluidity:
D. It is convenient to separate the product and the runner system. The design of the gate shape, size and position depends on the nature of the plastic, the size and structure of the product.
The Cross-sectional Shape of the Gate:
Generally, the cross-sectional shape of the gate is rectangular or circular, and the cross-sectional area should be small and the length should be short. This is not only based on the above effects, but also because it is easier for small gates to become larger, and it is difficult for large gates to shrink. The gate location should generally be selected where the product is thickest without affecting the appearance. The design of the gate size should take into account the properties of the plastic melt.
Cavity is the space in the mold for molding plastic products. The components used to form the cavity are collectively referred to as molded parts. Each molded part often has a special name. The molded parts that constitute the shape of the product are called concave molds (also called female molds), which constitute the internal shape of the product(Such as holes, slots, etc.) are called cores or punches (also known as male molds). When designing molded parts, the overall structure of the cavity must first be determined according to the properties of the plastic, the geometry of the product, the dimensional tolerances and the requirements for use. The second is to select the parting surface, the position of the gate and the vent hole and the demoulding method according to the determined structure.
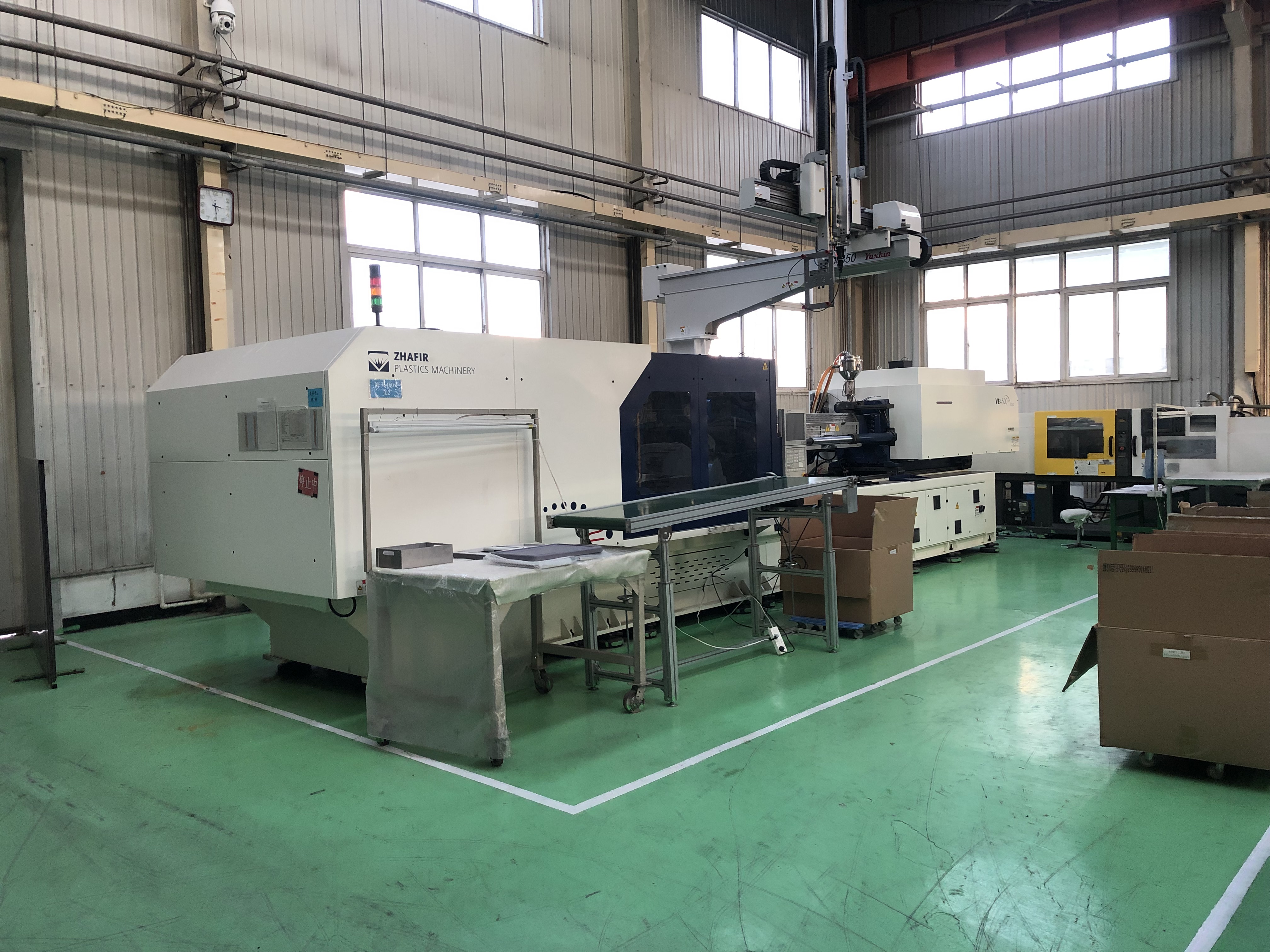
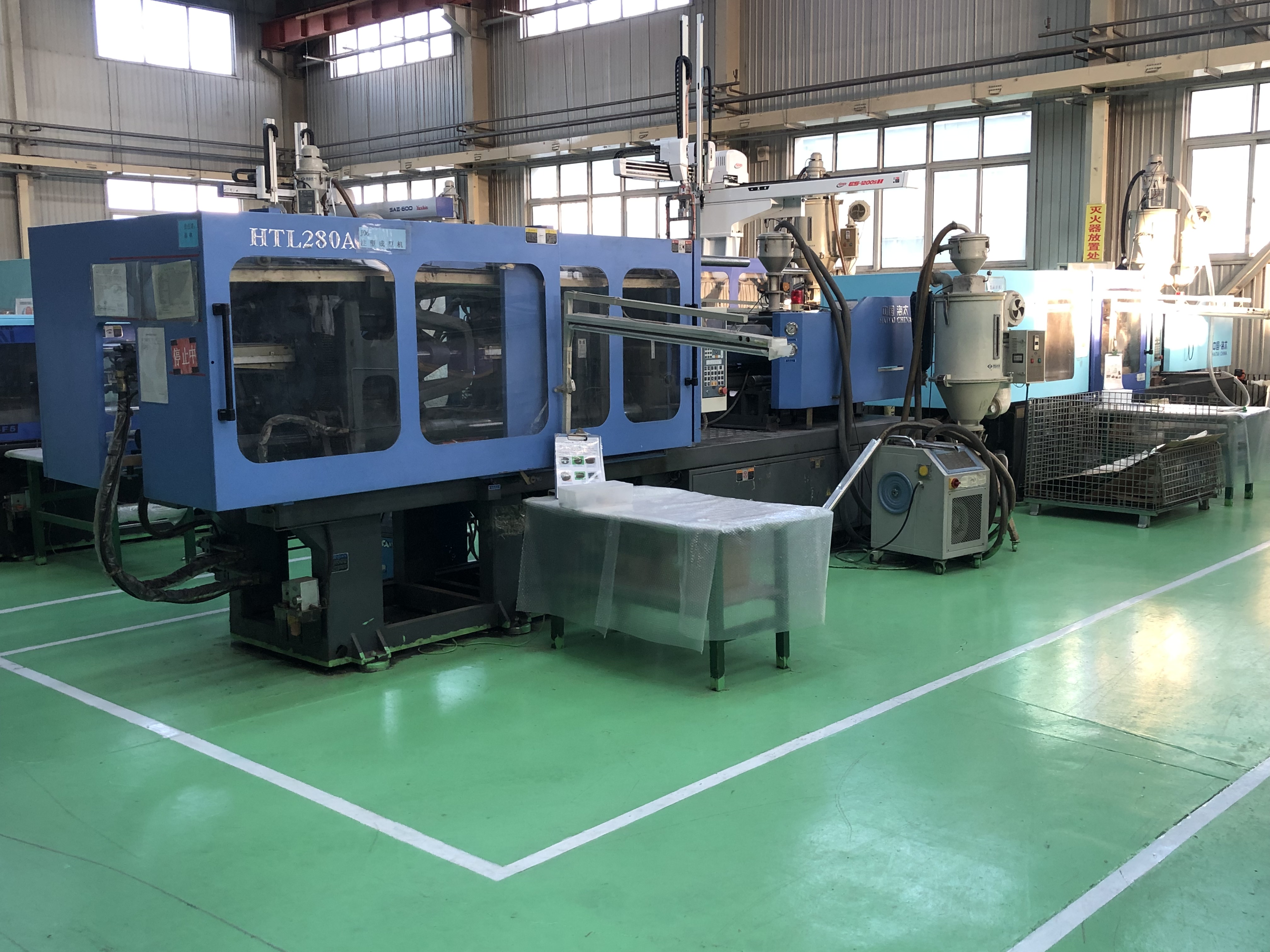
Finally, according to the size of the control product, the design of each part and the combination of each part are determined. The plastic melt has a high pressure when it enters the cavity, so the molded parts should be selected reasonably and checked for strength and rigidity. In order to ensure the smooth and beautiful surface of plastic products and easy demoulding, the roughness of the surface in contact with the plastic should be Ra>0.32um, and it should be corrosion-resistant. Formed parts are generally heat treated to increase the hardness, and are made of corrosion-resistant steel.
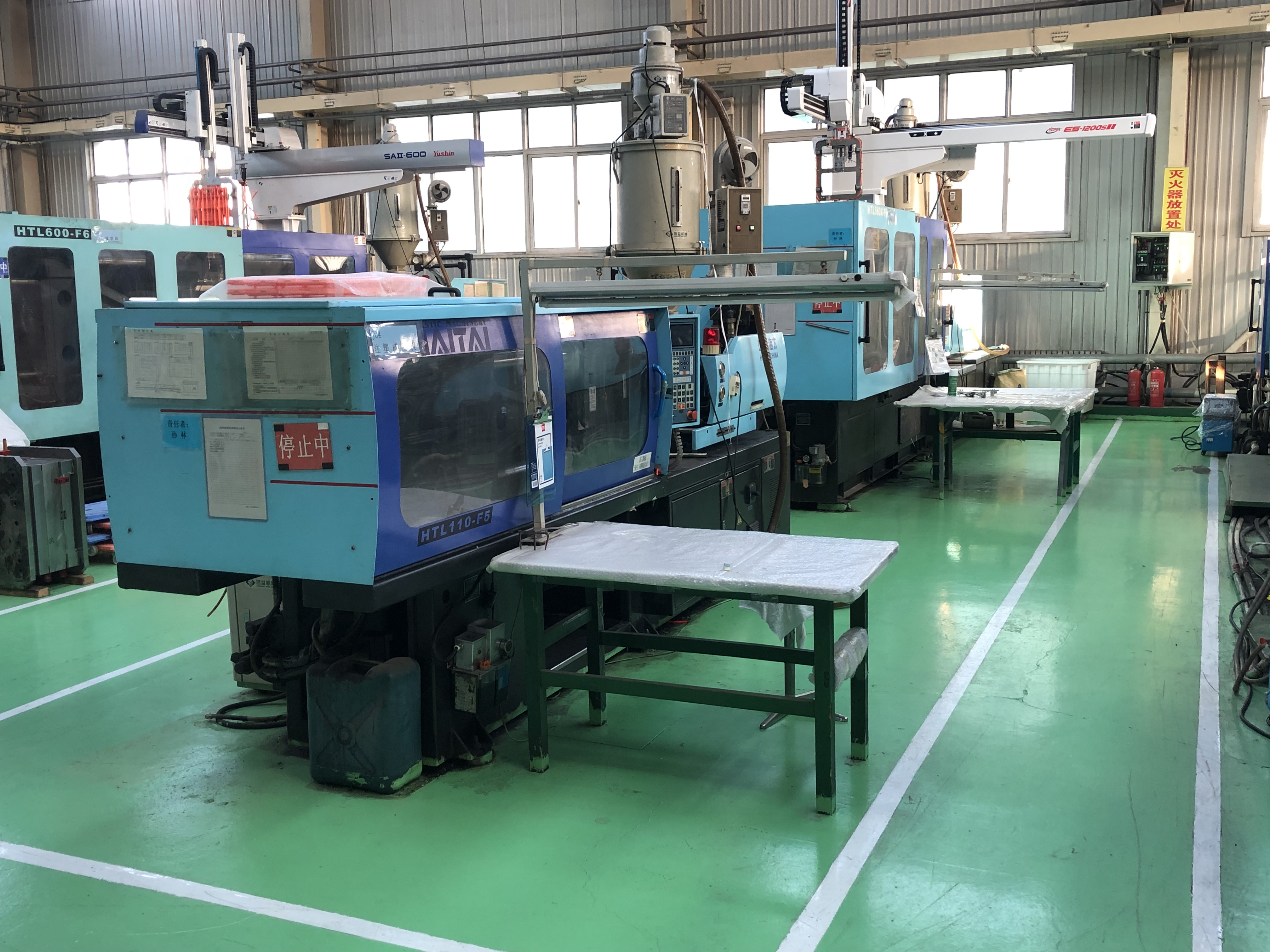
Post time: Sep-22-2021