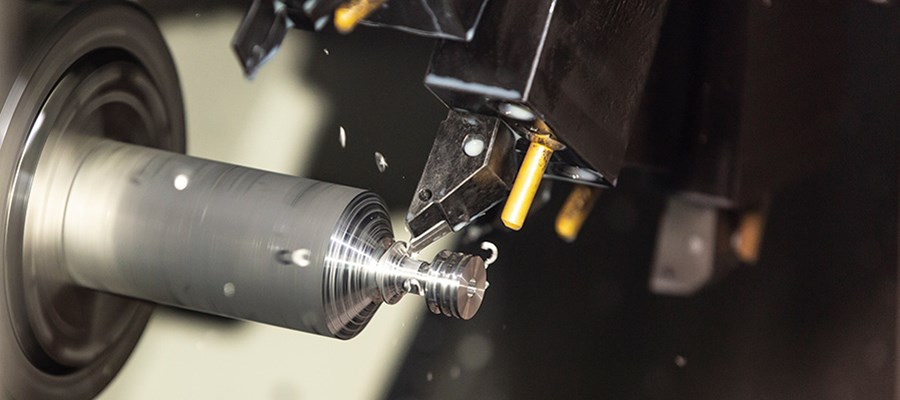
Reaming
When titanium alloy is reamed, the tool wear is not serious, and both cemented carbide and high-speed steel reamers can be used. When using carbide reamers, the rigidity of the process system similar to drilling should be adopted to prevent the reamer from chipping. The main problem of titanium alloy reaming is the poor finish of the reaming. The width of the reamer's margin must be narrowed with oilstone to prevent the margin from sticking to the hole wall, but to ensure sufficient strength, the general blade width is 0.1 ~ 0.15mm as well.
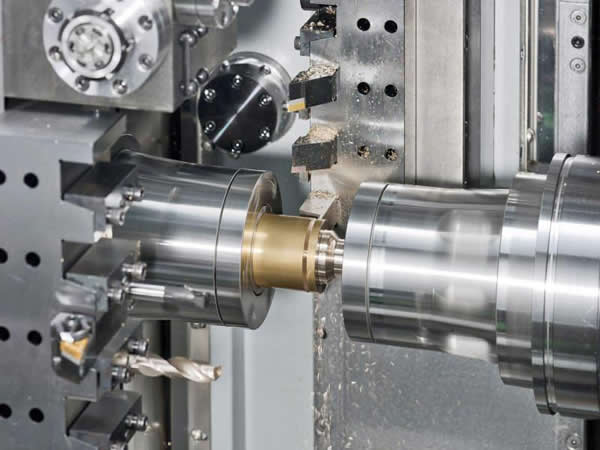
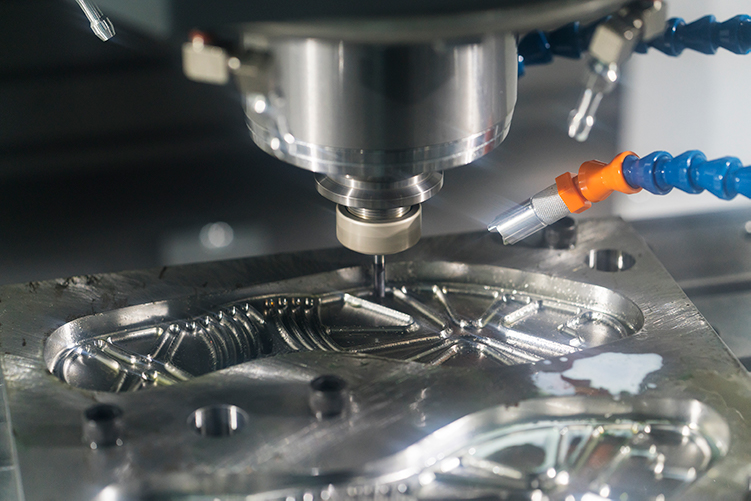
The transition between the cutting edge and the calibration part should be a smooth arc, and it should be reground in time after wear, and the arc size of each tooth should be the same; if necessary, the calibration part can be enlarged.
Drilling
Titanium alloy drilling is more difficult, and the phenomenon of knife burning and drill breaking often occurs during processing. This is mainly due to several reasons such as poor sharpening of the drill bit, untimely chip removal, poor cooling and poor rigidity of the process system. Therefore, in the drilling of titanium alloys, it is necessary to pay attention to reasonable drill sharpening, increase the apex angle, reduce the rake angle of the outer edge, increase the rear angle of the outer edge, and increase the back taper to 2 to 3 times that of the standard drill bit. Retract the tool frequently and remove the chips in time, pay attention to the shape and color of the chips. If the chips appear feathery or change in color during the drilling process, it indicates that the drill bit is blunt and should be replaced in time for sharpening.
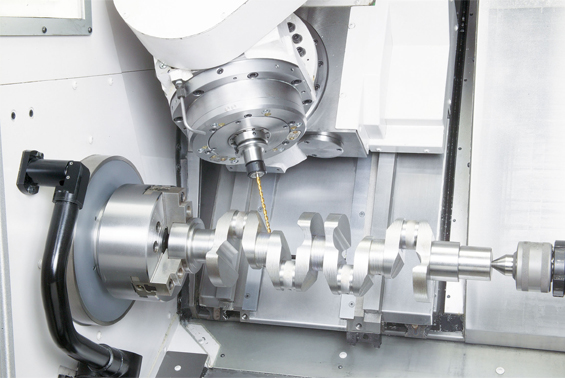
The drill die should be fixed on the worktable, and the guide face of the drill die should be close to the machined surface, and a short drill bit should be used as much as possible. Another problem worth noting is that when manual feeding is adopted, the drill bit should not advance or retreat in the hole, otherwise the drill edge will rub the machined surface, causing work hardening and dulling the drill bit.
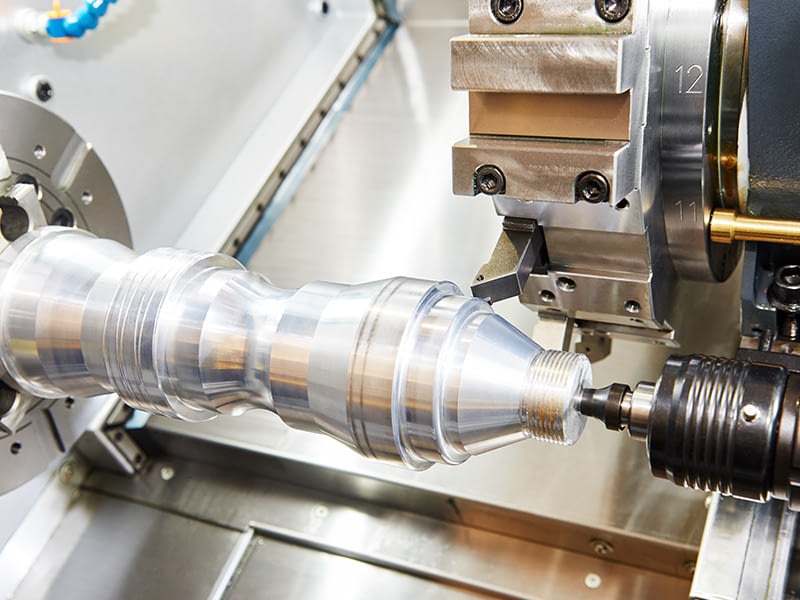
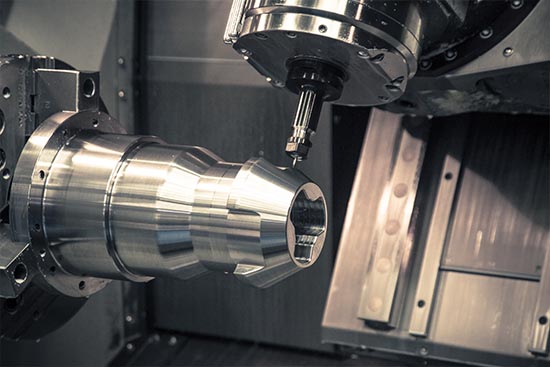
Grinding
Common problems with grinding titanium alloy parts are sticky chips that cause wheel clogging and burns on the surface of the part. The reason is that the thermal conductivity of titanium alloy is poor, which causes high temperature in the grinding area, so that titanium alloy and abrasive will bond, diffuse and have a strong chemical reaction. Sticky chips and blockage of the grinding wheel lead to a significant drop in the grinding ratio. As a result of diffusion and chemical reactions, the workpiece is burnt on the ground surface, resulting in a reduction in the fatigue strength of the part, which is more pronounced when grinding titanium alloy castings.
To solve this problem, the measures taken are:
Choose the right grinding wheel material: Green Silicon Carbide TL. Slightly lower wheel hardness: ZR1.
The cutting of titanium alloy materials) must be controlled from the aspects of tool material, cutting fluid, and processing parameters in order to improve the overall efficiency of titanium alloy material processing.
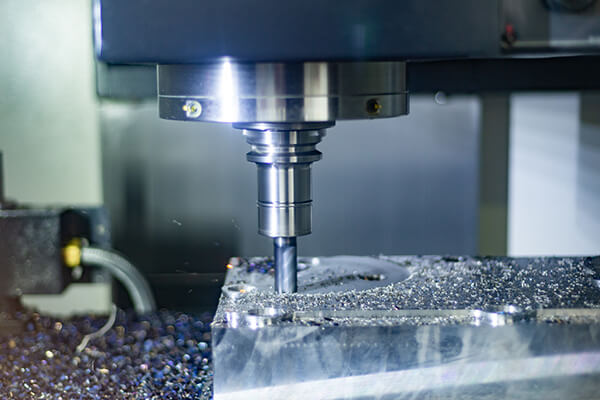
Post time: Mar-14-2022