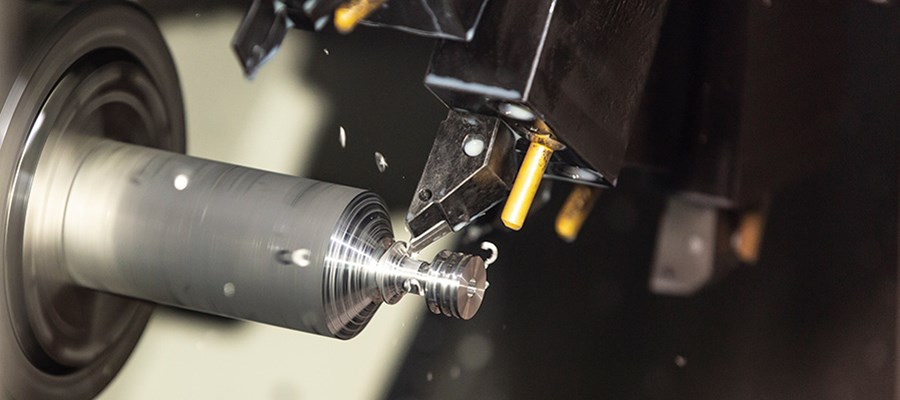
1. Physical Micromachining Technology
Laser Beam Machining: A process that uses laser beam-directed thermal energy to remove material from a metal or non-metallic surface, better suited for brittle materials with low electrical conductivity, but can be used for most materials.
Ion beam processing: an important unconventional fabrication technique for micro/nano fabrication. It uses a flow of accelerated ions in a vacuum chamber to remove, add or modify atoms on the surface of an object.
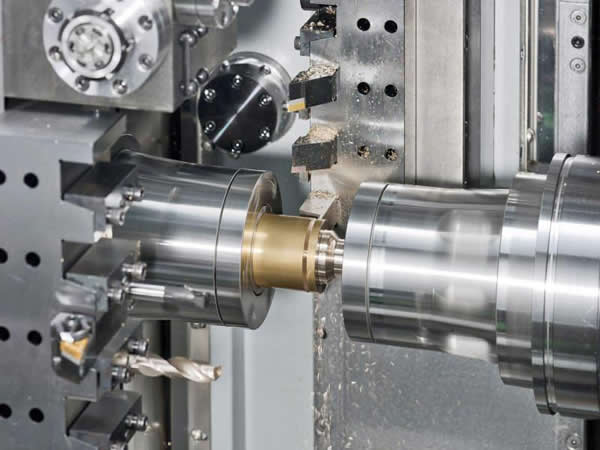
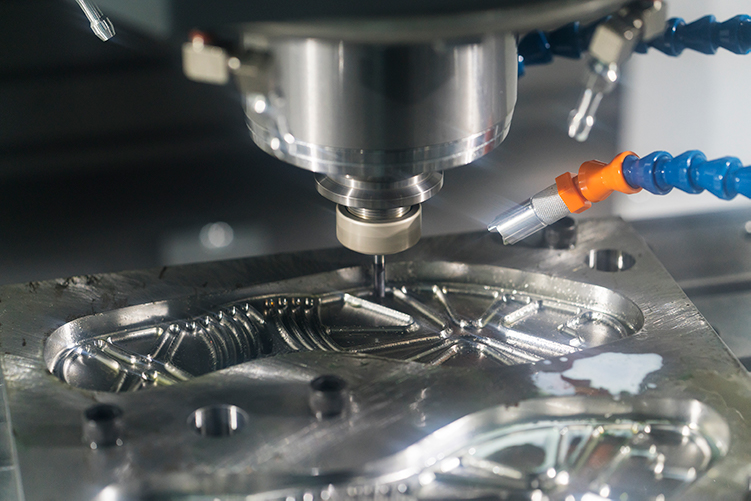
2. Chemical micromachining technology
Reactive Ion Etching (RIE): is a plasma process in which species are excited by a radio frequency discharge to etch a substrate or thin film in a low pressure chamber. It is a synergistic process of chemically active species and bombardment of high-energy ions.
Electrochemical Machining (ECM): A method of removing metals through an electrochemical process. It is typically used for mass production machining of extremely hard materials or materials that are difficult to machine with conventional methods. Its use is limited to conductive materials. ECM can cut small or profiled angles, complex contours or cavities in hard and rare metals.
3. Mechanical micromachining technology
Diamond Turning: The process of turning or machining precision components using lathes or derived machines equipped with natural or synthetic diamond tips.
Diamond Milling: A cutting process that can be used to generate aspheric lens arrays using a spherical diamond tool through a ring cutting method.
Precision Grinding: An abrasive process that allows workpieces to be machined to a fine surface finish and very close tolerances to 0.0001" tolerances.
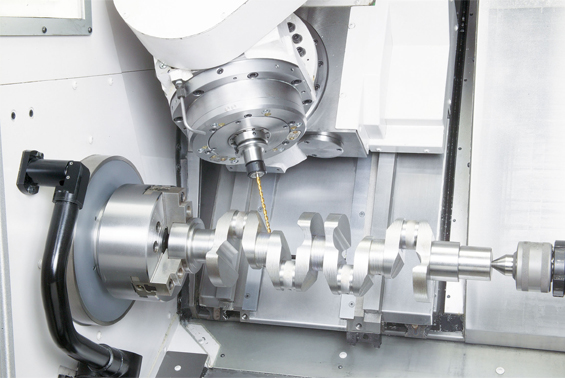
Polishing: An abrasive process, argon ion beam polishing is a fairly stable process for finishing telescope mirrors and correcting residual errors from mechanical polishing or diamond-turned optics, the MRF process was the first deterministic polishing process. Commercialized and used to produce aspherical lenses, mirrors, etc.
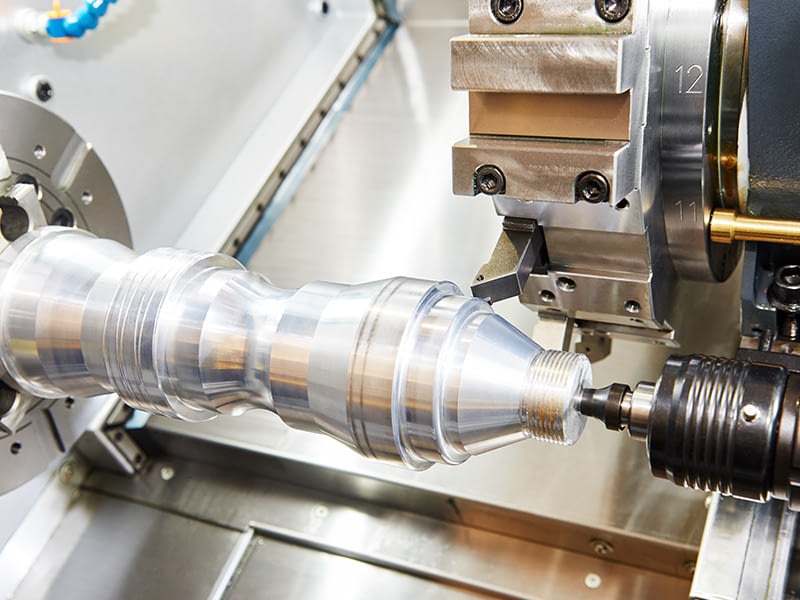
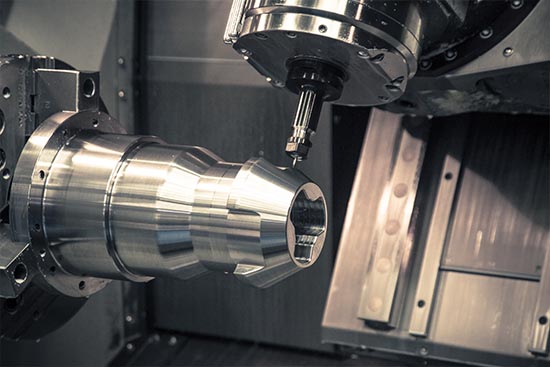
3. Laser micromachining technology, powerful beyond your imagination
These holes on the product have the characteristics of small size, dense number, and high processing accuracy. With its high strength, good directionality and coherence, laser micromachining technology can focus the laser beam into a few microns in diameter through a specific optical system. The light spot has a very high concentration of energy density. The material will quickly reach the melting point and melt into a melt. With the continued action of the laser, the melt will begin to vaporize, resulting in a fine vapor layer, forming a state where vapor, solid and liquid coexist.
During this period, due to the effect of steam pressure, the melt will be automatically sprayed out, forming the initial appearance of the hole. As the irradiation time of the laser beam increases, the depth and diameter of the microspores continue to increase until the laser irradiation is completely terminated, and the melt that has not been sprayed out will solidify to form a recast layer, so as to achieve the unprocessed laser beam.
With the increasing demand for micromachining of high-precision products and mechanical components in the market, and the development of laser micromachining technology is becoming more and more mature, laser micromachining technology relies on its advanced processing advantages, high processing efficiency and machinable materials. The advantages of small restriction, no physical damage, and intelligent and flexible control will be more and more widely used in the processing of high-precision and sophisticated products.
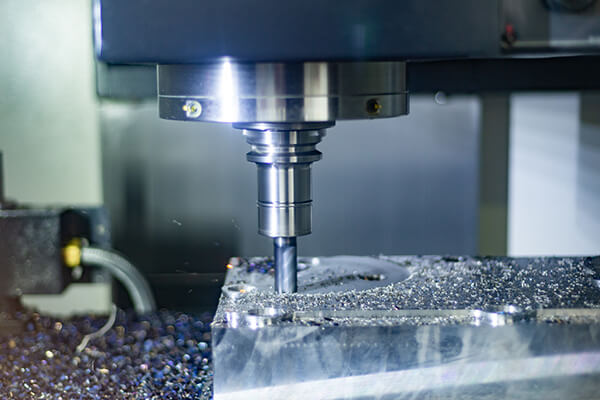
Post time: Sep-26-2022