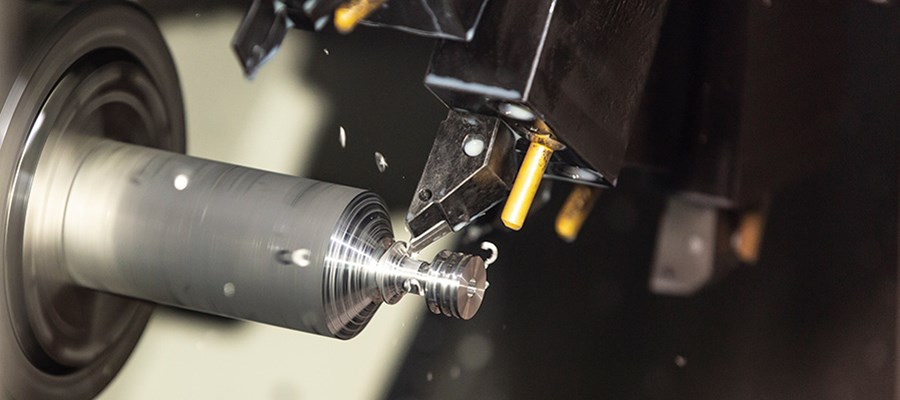
The wear of the insert groove in titanium alloy machining is the local wear of the back and front in the direction of the depth of cut, which is often caused by the hardened layer left by the previous processing. The chemical reaction and diffusion of the tool and the workpiece material at a processing temperature of more than 800 °C are also one of the reasons for the formation of groove wear. Because during the machining process, the titanium molecules of the workpiece accumulate in the front of the blade and are "welded" to the blade edge under high pressure and high temperature, forming a built-up edge. When the built-up edge peels off the cutting edge, the carbide coating of the insert is taken away.
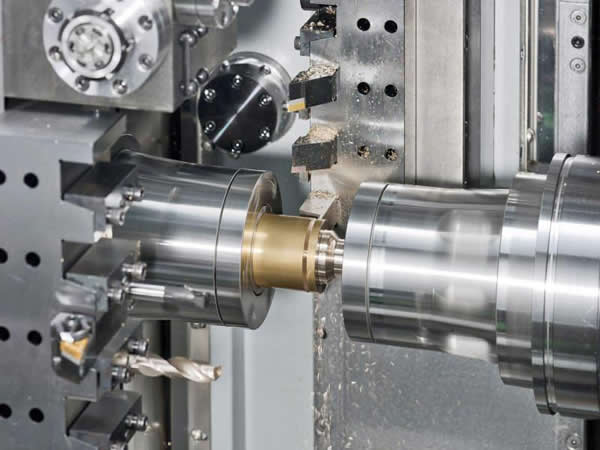
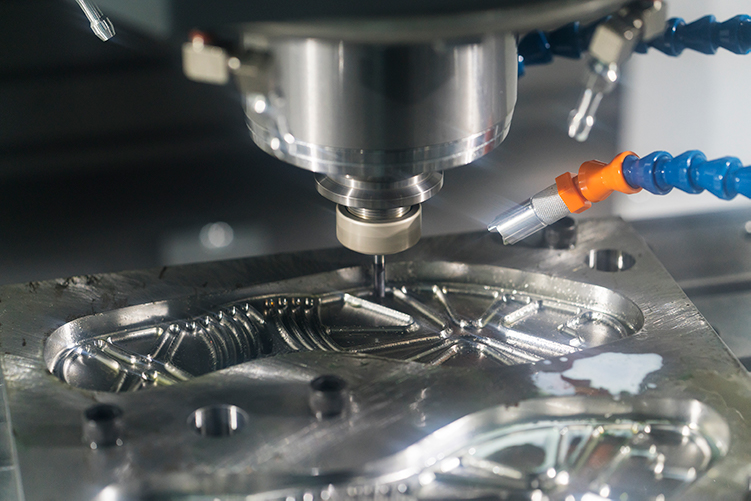
Due to the heat resistance of titanium, cooling is crucial in the machining process. The purpose of cooling is to keep the cutting edge and tool surface from overheating. Use end coolant for optimum chip evacuation when performing shoulder milling as well as face milling pockets, pockets or full grooves. When cutting titanium metal, the chips are easy to stick to the cutting edge, causing the next round of milling cutter to cut the chips again, often causing the edge line to chip.
Each insert cavity has its own coolant hole/injection to address this issue and enhance constant edge performance. Another neat solution is threaded cooling holes. Long edge milling cutters have many inserts. Applying coolant to each hole requires a high pump capacity and pressure. On the other hand, it can plug unneeded holes as needed, thereby maximizing flow to the holes that are needed.
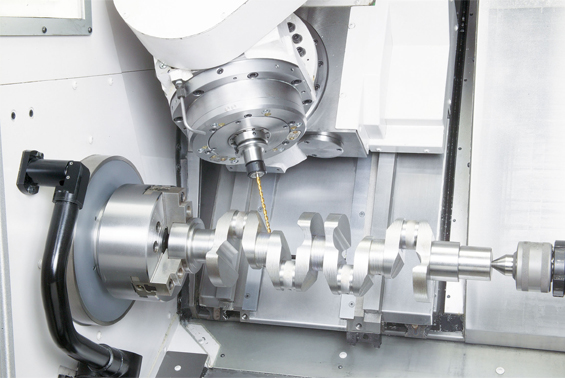
Titanium alloys are mainly used to make aircraft engine compressor parts, followed by structural parts of rockets, missiles and high-speed aircraft. The density of titanium alloy is generally about 4.51g/cm3, which is only 60% of steel. The density of pure titanium is close to that of ordinary steel.
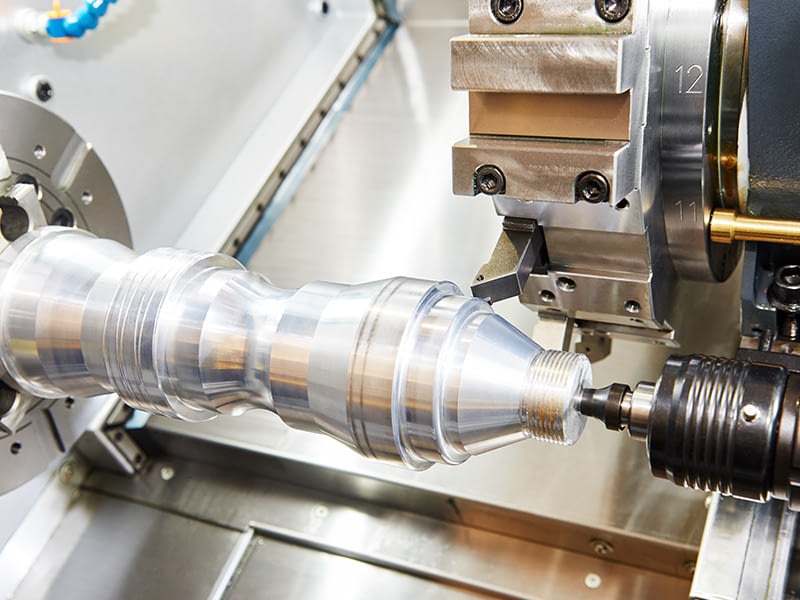
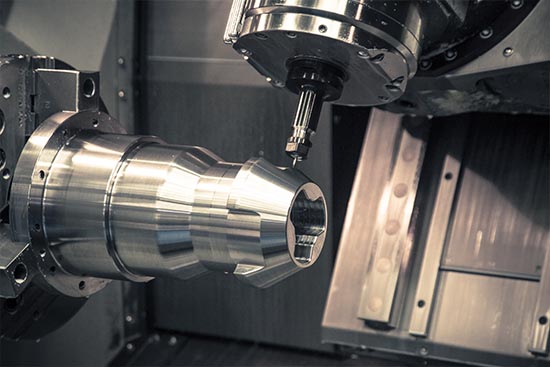
Some high-strength titanium alloys exceed the strength of many alloy structural steels. Therefore, the specific strength (strength/density) of titanium alloy is much greater than that of other metal structural materials, and parts with high unit strength, good rigidity and light weight can be produced. Titanium alloys are used in aircraft engine components, skeletons, skins, fasteners and landing gear.
In order to process titanium alloys well, it is necessary to have a thorough understanding of its processing mechanism and phenomenon. Many processors consider titanium alloys to be an extremely difficult material because they do not know enough about them. Today, I will analyze and analyze the processing mechanism and phenomenon of titanium alloys for everyone.
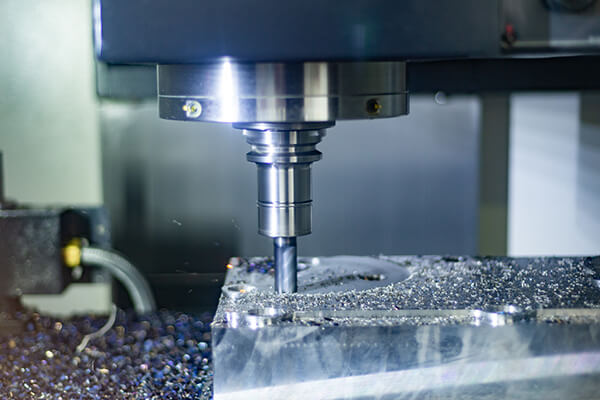
Post time: Mar-28-2022