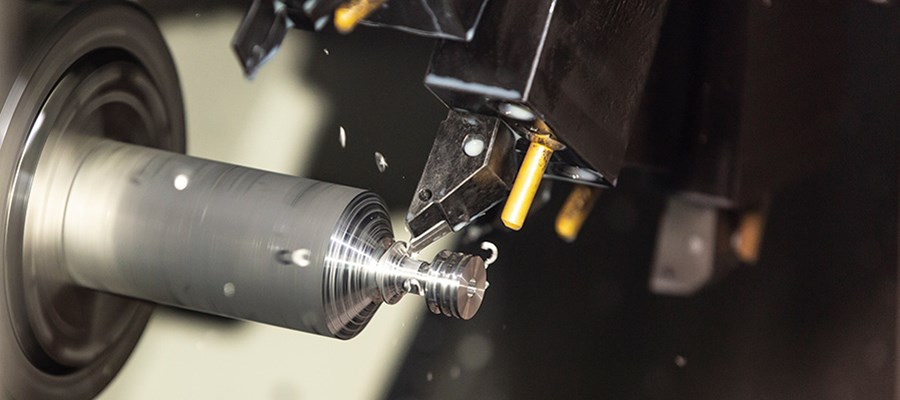
On April 17, the 7103 Plant of the Sixth Institute of Aerospace Science and Technology Group conducted a test run with a liquid oxygen kerosene engine behind the secondary pump of my country's new-generation manned launch vehicle. The test run was started according to the predetermined procedure, and the engine worked for 10 seconds.
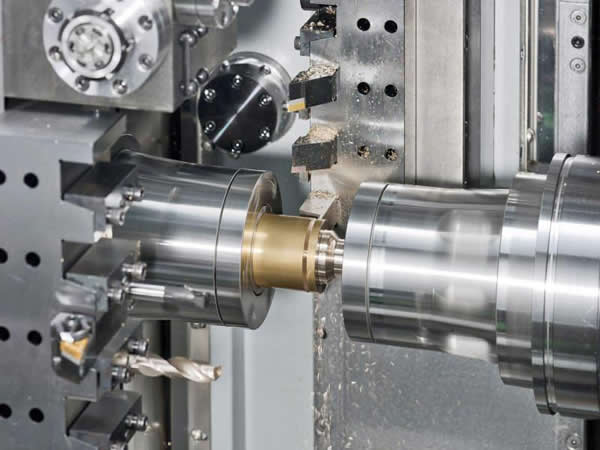
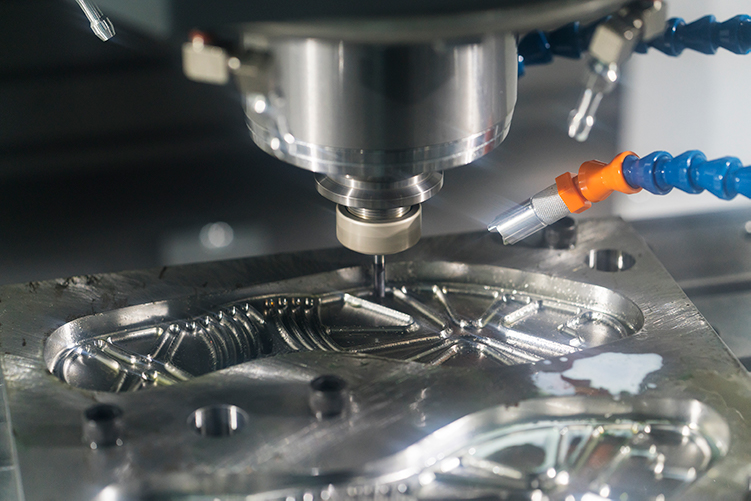
The engine of this test run adopts the first titanium alloy large nozzle thrust chamber newly developed in my country, which greatly reduces the weight of the engine. The whole engine assembly adopts an inverted assembly scheme. This test run successfully verified the feasibility of the titanium alloy nozzle scheme.
On the basis of the existing engine thrust chamber, the new generation of manned carrier rocket secondary pump rear-swing liquid oxygen kerosene engine develops titanium alloy nozzles to realize the effective connection between the existing thrust chamber copper-steel material system and the titanium-titanium structure, and further Reduce the weight of the engine, improve the thrust-to-mass ratio of the engine, and improve the effective carrying capacity of the rocket.
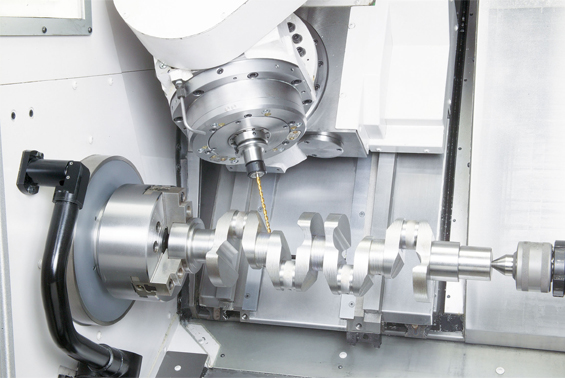
It is reported that at the beginning of the project of this type of engine, my country has no experience in the development and production of large-sized titanium alloy nozzles, and everything needs to be "started from scratch". Faced with the arduous research and development task, the 7103 factory established a research and development team for titanium alloy large nozzles. In the face of one technical problem after another, the research team fully carried forward the spirit of spaceflight, actively carried out technical research, and gathered wisdom to solve problems. In order to ensure the development progress of the titanium alloy nozzle, the research team regularly organizes regular meetings to coordinate in time, study and deal with the problems and difficulties in the development process.
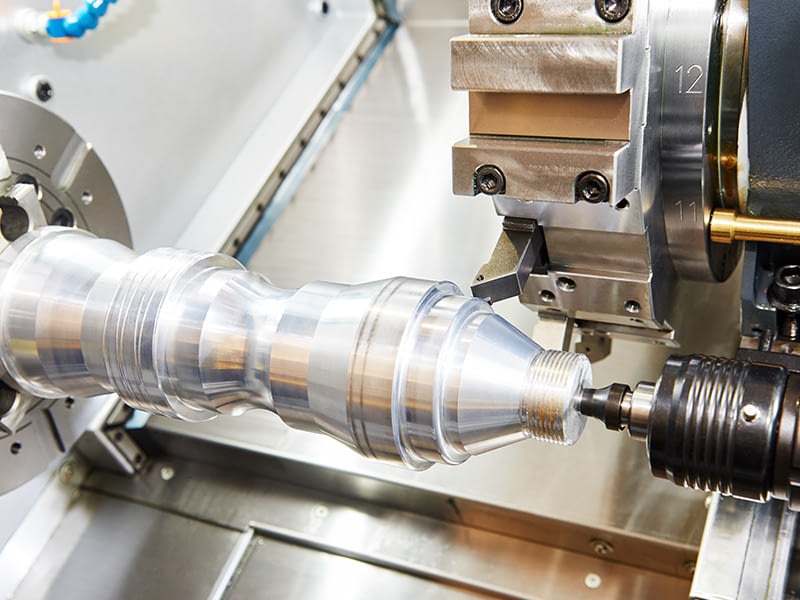
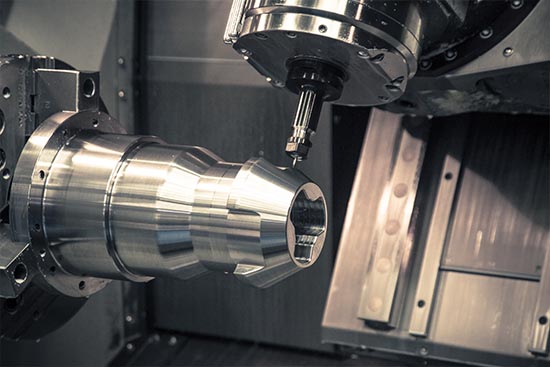
After 5 years, the research team has successively conquered a number of key technologies, successfully developed my country's first large-size titanium alloy nozzle thrust chamber, and delivered it to the test run as scheduled. The unidirectional compression experiment of TC4 titanium alloy was carried out on a Gleeble-3800 thermal simulation testing machine to study the high temperature deformation behavior of the alloy under the conditions of a compression amount of 50%, a temperature of 700-900 ℃ and a strain rate of 0.001-1 s-1.
The microstructure of TC4 titanium alloy after high temperature compression experiment was observed by metallographic microscope, the dynamic recrystallization process of TC4 titanium alloy was studied, and the factors affecting the dynamic spheroidization of TC4 titanium alloy layered structure were analyzed. The critical strain was determined by fitting the work hardening rate and flow stress curve with cubic polynomial, and the spheroidization kinetic model was studied according to the stress-strain curve of TC4 titanium alloy. The results show that the increase of the deformation temperature and the decrease of the strain rate promote the dynamic recrystallization process.
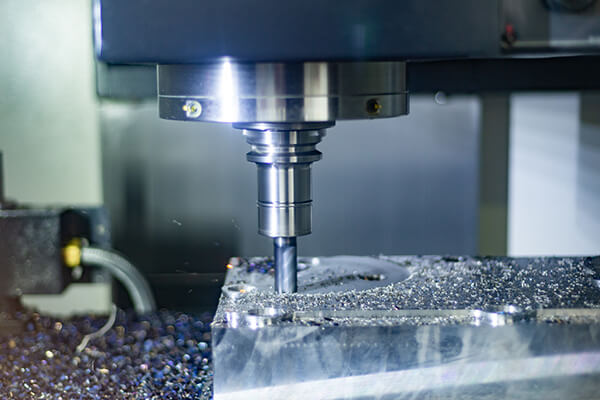
Post time: May-16-2022