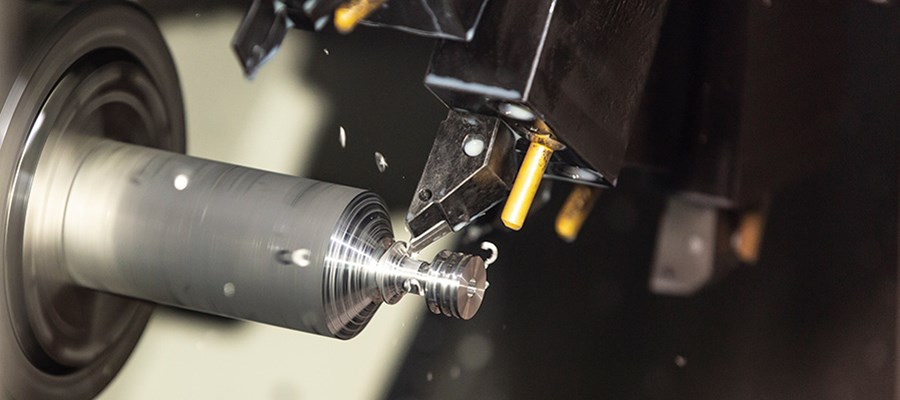
In 2021, the new crown epidemic is still severe, and global economic growth is severely limited. However, the new crown virus cannot stop the pace of scientific and technological progress. Military materials are the most basic and cutting-edge technology. Under the traction of the development needs of equipment replacement, the milestone technological breakthrough is still remarkable. In the past three years, we have successively launched the "Major Development Trends of Foreign Military Materials Technology". By systematically sorting out the technological progress in the field of military materials in this year, we have selected ten technologies with significant influence, and judged the future development trend of the materials field, inspiring readers and readers. Scientific researchers, providing a platform for discussion. Over the past three years, this work has achieved good responses.
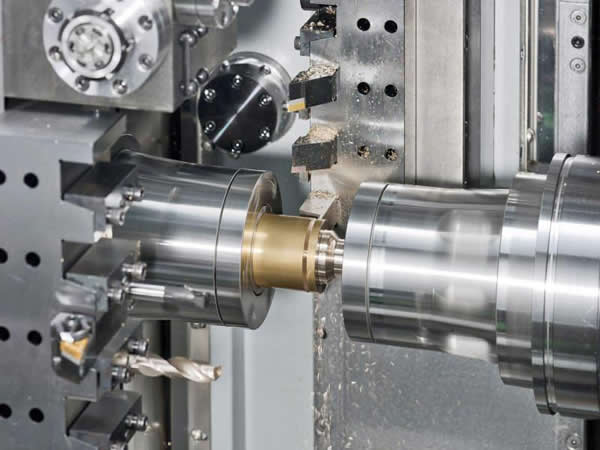
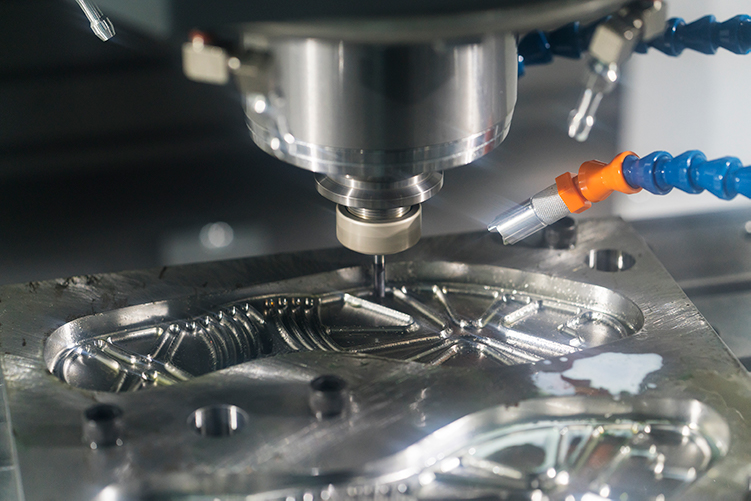
In 2021, the development momentum of composite materials will be strong, and they will perform well in the application exploration in the fields of aerospace and weapons; for different application environments, new materials such as high-performance radiation resistance and wear resistance will emerge; 2nm process chips will light up electronics. At the high point of the development of information functional materials, bismuth materials have opened up the way for 1nm process chips. In addition, the introduction of new algorithms has also accelerated the discovery of various inorganic compounds and high-entropy alloy materials that rely on component design.
On January 19, 2022, China Aviation Industry Development Research Center organized experts in Beijing to carry out the selection work of "Major Trends in Foreign Military Materials in 2021". From a total of 158 development trends in five fields, including performance metal materials, advanced composite materials, special functional materials, electronic information functional materials, and key raw materials, the following ten major technical trends are selected for reference by decision-making institutions, scientific research units and readers.
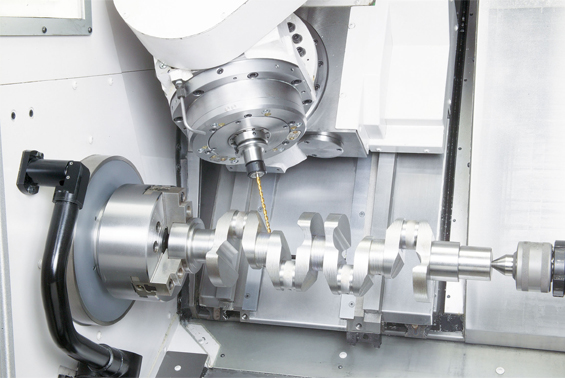
The U.S. Air Force successfully verified the continuous fiber 3D printer wing spars
Rapid production and low-cost flexible customization are important requirements for the current development of carbon fiber composite materials. The U.S. Air Force Research Laboratory is highly focused on continuous fiber 3D printing technology, hoping it can become a breakthrough technology approach to replacing traditional composite manufacturing methods, reducing the cost and lead time of composite parts. In April 2021, U.S. Continuous Composites used its patented continuous fiber 3D printing technology (CF3D) to successfully print two 2.4-meter-long, 1.8-kilogram carbon fiber composite spar assemblies, completing the U.S. Air Force Research Laboratory.
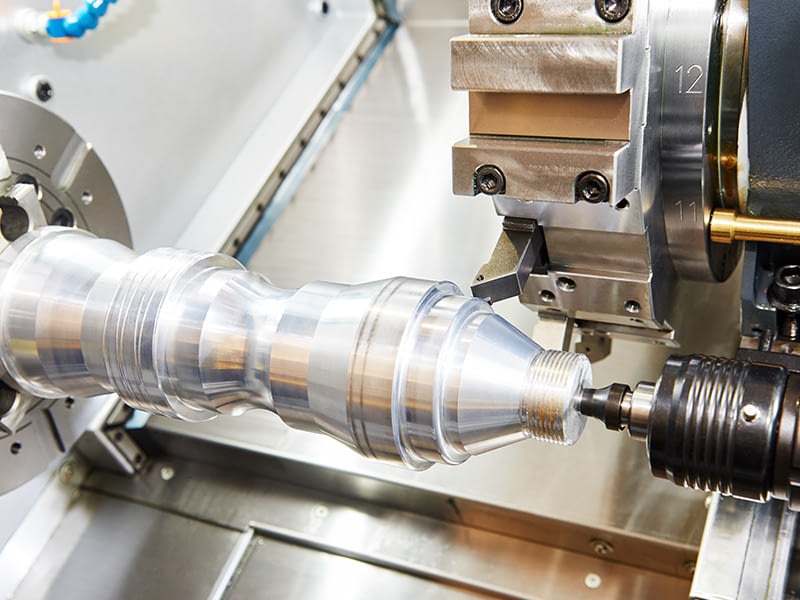
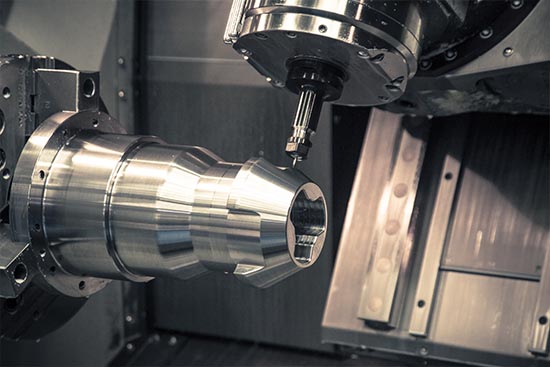
Two-year Wing Structure Design for Manufacturing (WiSDM) contract. Static test results of the final wing assembly surface, the fully assembled wing was loaded to 160% of the design limit load. No measurement or visual damage to the CF3D printed spars was detected. The printed carbon fiber spar achieved a fiber volume fraction of 60% with approximately 1%-2% voids.
This new composite fabrication method features in-situ impregnation, consolidation and curing, which significantly reduces costs and lead times. The fully automated process features cutting and refeeding for ply drop and variable part thickness within the structure. The project, which optimizes oriented structural fibers, is a success story using a custom CF3D material solution, with implications for the manufacture of expensive aerospace structural parts.
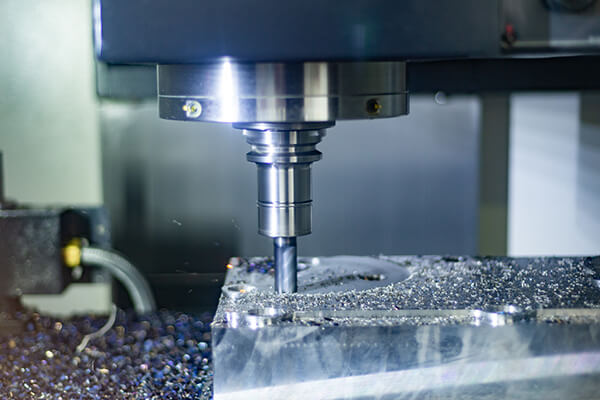
Post time: Jul-05-2022