With the unceasing change of customer demand, in order to adapt to the market demand of non-standard custom products increasingly become the mainstream, but non-standard custom due to the non-standard products, quality, cost, delivery control still is the core content of production management, production management of each work must also be around to improve product quality, reduce production cost, satisfy the customer delivery in order to develop.
Non-standard features analysis before the implementation of the company's products should be classified according to the product properties and use of the range, in fact is a kind of the standardization of product design (cannot make refrigerators and cars on an assembly line) most designers in the design of non-standard products according to the enterprise has some standardized products as the prototype design is improved. The standard product pretending to be the design prototype is the basis of the analysis of the non-standard characteristics of the non-standard product. Process personnel must be serious about the product process research and analysis, pay special attention to the non-standard part of the process design, must consider the existing production line equipment, tooling, tools, and even the workstation and working space, as far as possible under the existing process level to complete the process design of non-standard products.
At the same time, if in the process of process analysis, it is found that the design structure is not conducive to the production under the existing conditions, it is necessary to communicate with the designer about the process, and unify to the existing production and manufacturing platform without changing the needs of customers. Finally, the technician must specify the specific process treatment on the process analysis card.
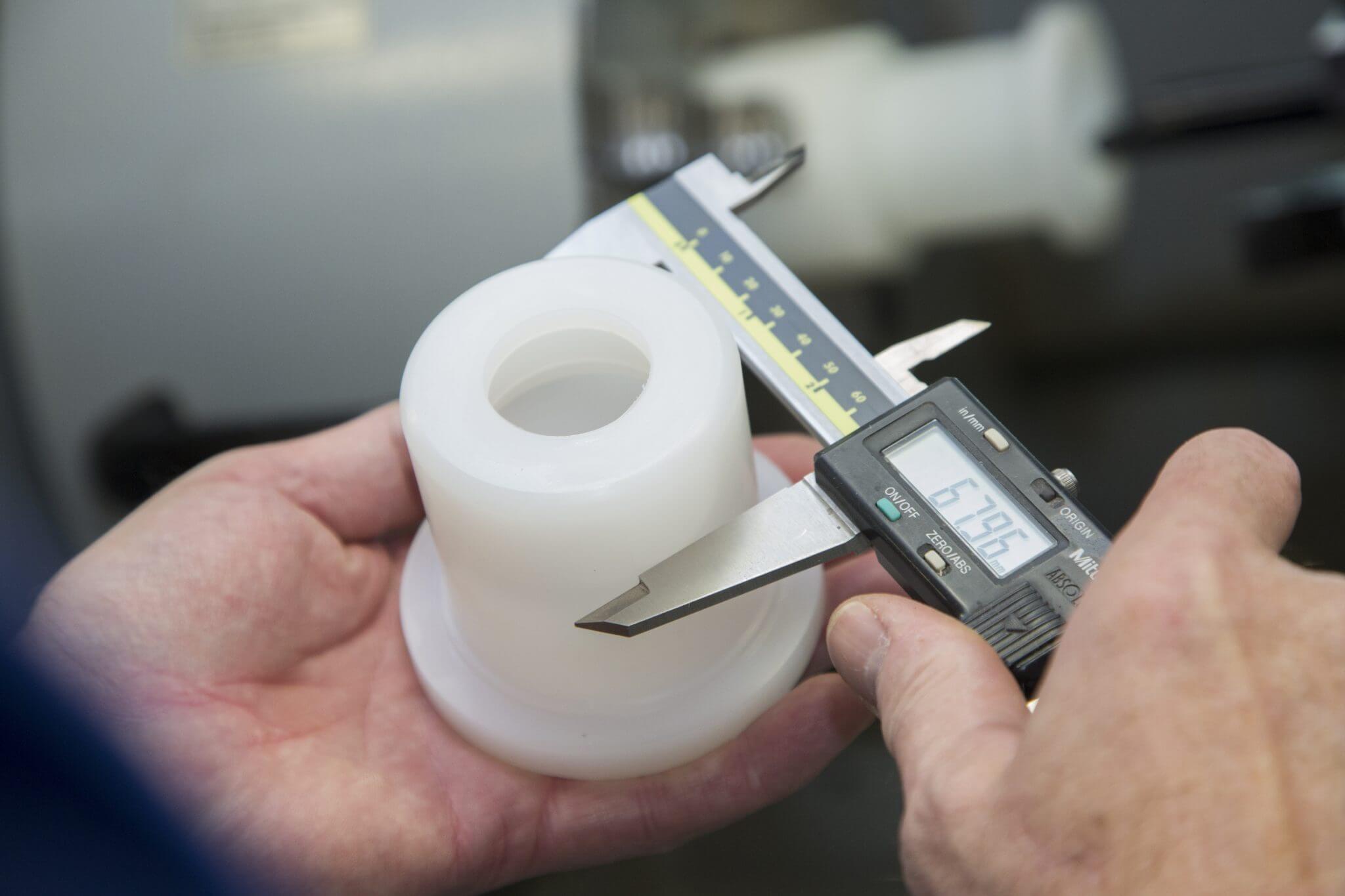
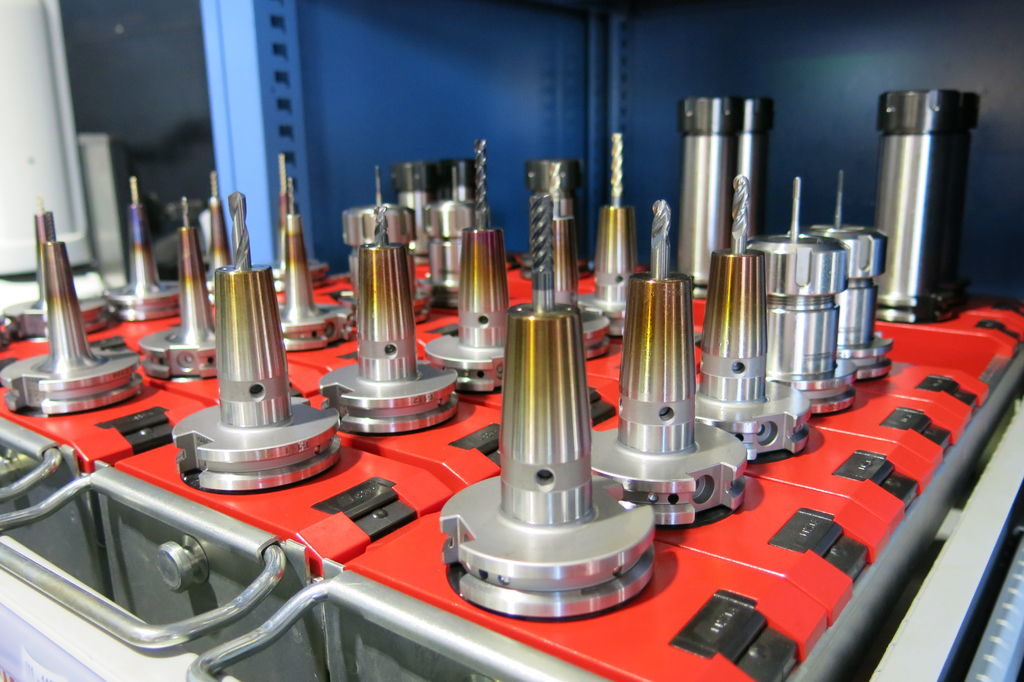
Mechanical processing is mainly manual processing and numerical control processing two categories. Manual processing refers to the process of machining various materials through manual operation of milling machines, lathes, drilling machines and sawing machines. Manual processing is suitable for small batch, simple parts production. Numerical control machining (CNC) refers to mechanical workers using numerical control equipment for machining, such as machining centers, turning milling centers, electrical discharge wire cutting equipment, thread cutting machines, etc.
The vast majority of machining workshops adopt numerical control machining technology. Through programming, the workpiece in the Cartesian coordinate system position coordinates (X, Y, Z) into the program language, CNC machine tool CNC controller through recognition and interpretation of the program language to control the axis of CNC machine tool, automatic removal of materials according to the requirements, so as to get the finishing workpiece. CNC machining processes the workpiece in a continuous manner, suitable for large quantities of complex shape parts.
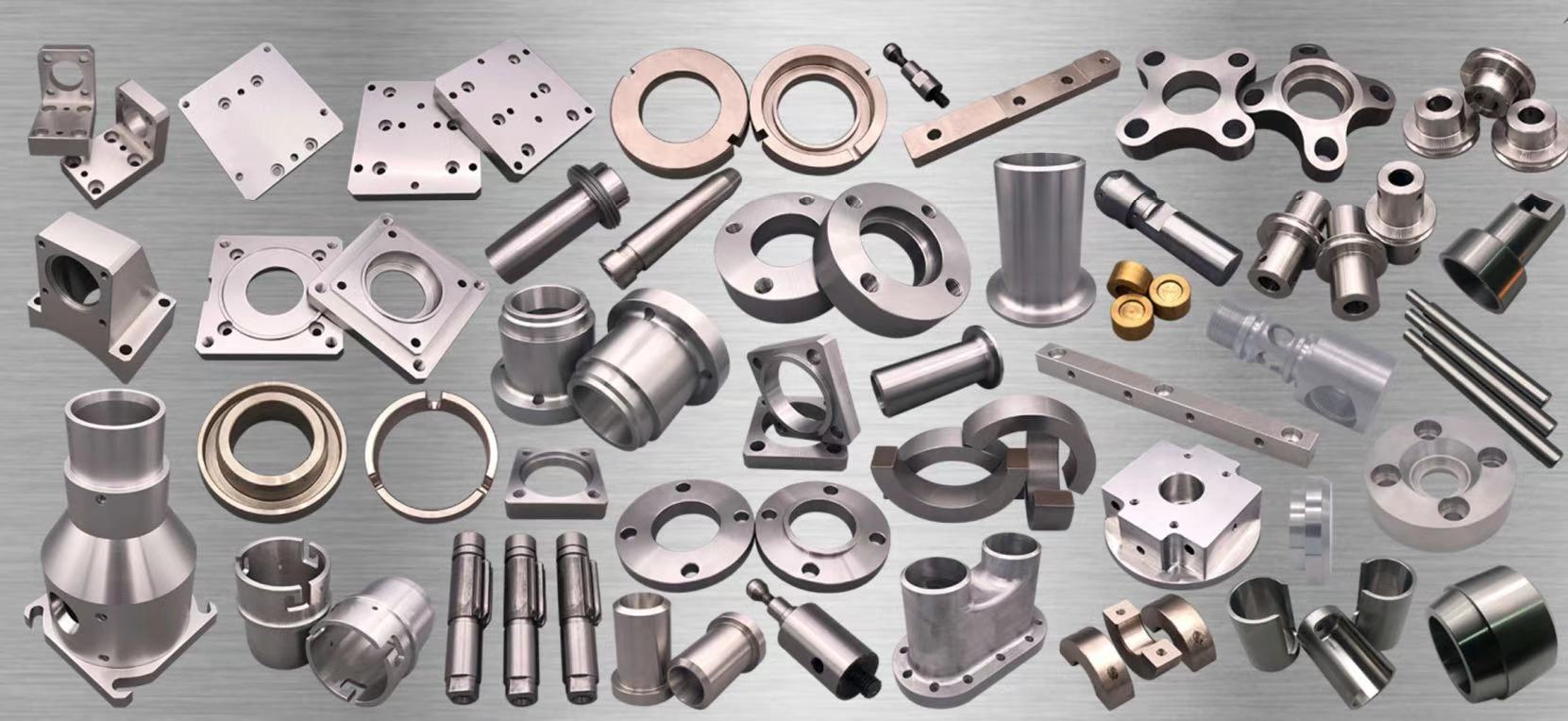
Post time: Nov-22-2021