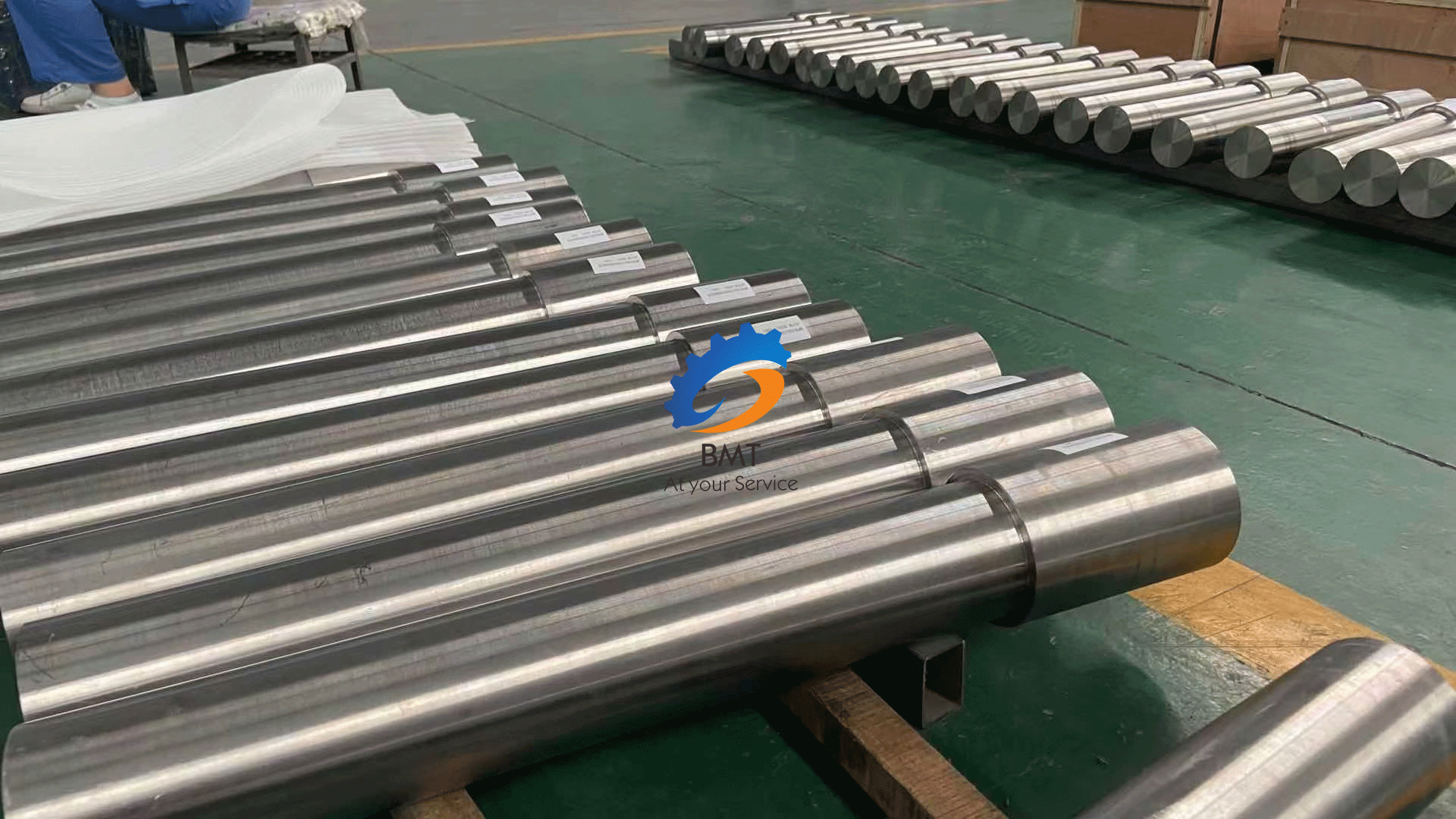
Innovative machining techniques in the field of custom titanium shafts have taken a significant leap forward with the introduction of CNC machining. Amalgamating versatility and precision, this cutting-edge technology has revolutionized the manufacturing process and enhanced the quality of titanium shafts, making them increasingly popular across multiple industries. The titanium Gr2 shafts, specifically engineered using CNC machining, offer unparalleled strength, durability, and corrosion resistance. Titanium, already well-known for its lightweight properties, is now further optimized by advanced machinery for enhanced performance.
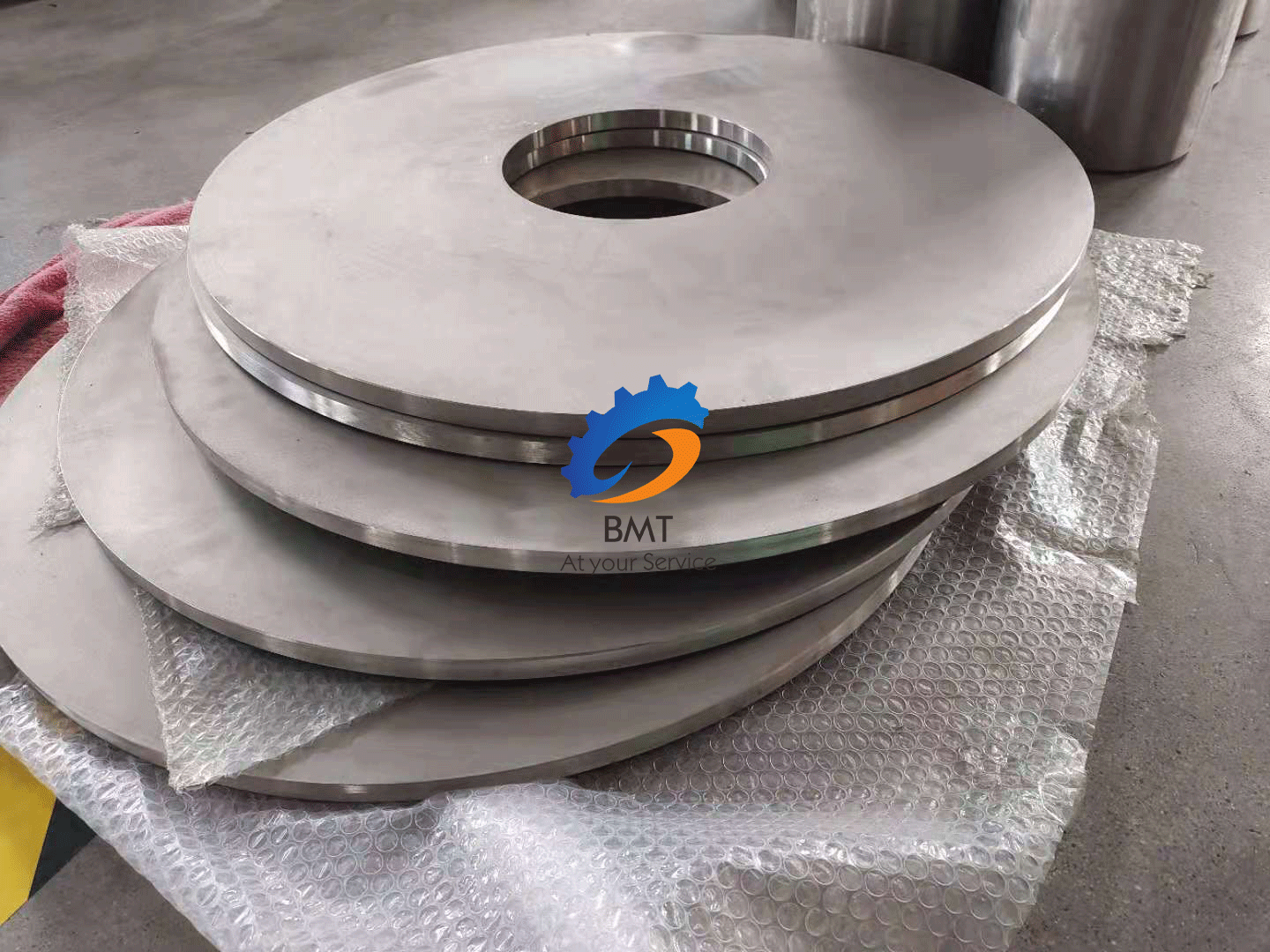
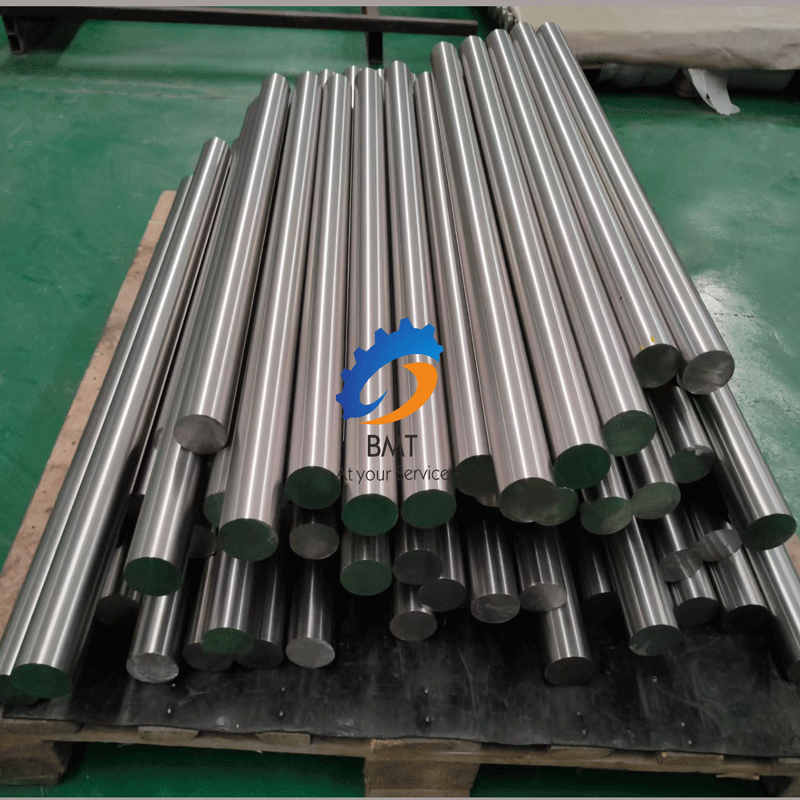
This has opened up new avenues for industries seeking to improve their products and processes, such as aerospace, automotive, medical, and defense. One of the key advantages of CNC machining is its high level of accuracy. The computerized system can produce titanium Gr2 shafts with incredibly tight tolerances, ensuring a consistent and precise end product.
This accuracy is particularly crucial for applications that demand seamless integration, such as aerospace components or surgical tools. CNC machining eliminates human error, resulting in shafts that fit perfectly into complex systems, ultimately increasing overall efficiency and reducing the risk of failure.
Additionally, the customizability of CNC machining allows for the production of titanium Gr2 shafts in a wide range of intricate shapes and sizes. Previously, manufacturers faced limitations in creating complex designs due to the constraints of traditional machining methods. However, CNC machining has opened up endless possibilities, enabling the creation of shafts with intricate geometries, internal threads, and even hollow cores. This versatility allows designers and engineers to push the boundaries of innovation, resulting in products that are optimized for their specific applications. The impact of custom titanium Gr2 shafts extends far beyond improved performance. By utilizing CNC machining, manufacturers can achieve significant cost savings and reduced lead times.
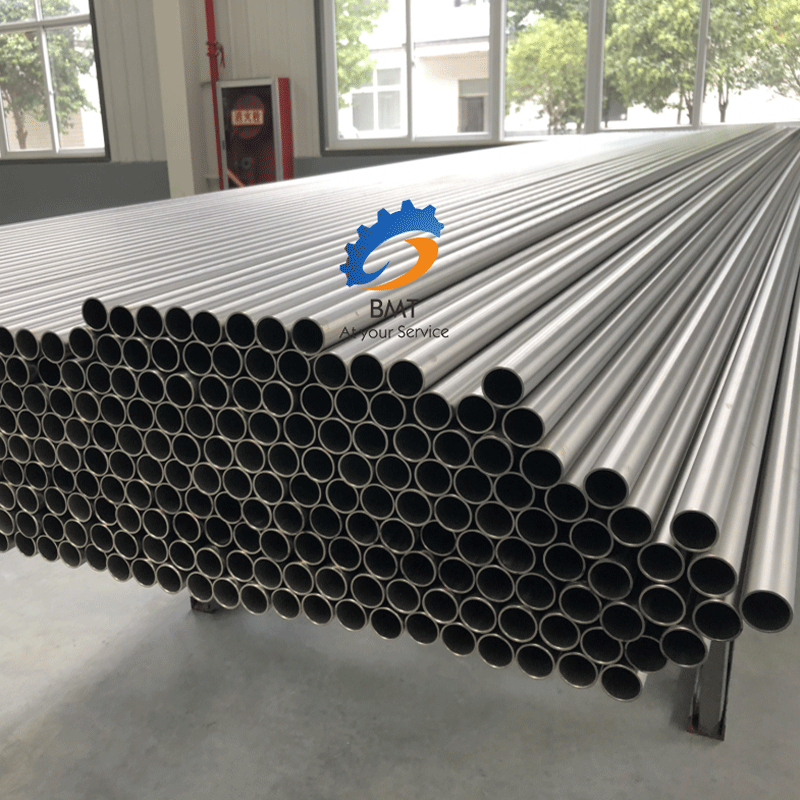
The automated nature of CNC machines eliminates time-consuming manual processes, resulting in faster production cycles. Additionally, the precision of these machines minimizes material wastage, leading to cost-effective production. This affordability, combined with the increased demand for lightweight and durable components, has led to a surge in titanium Gr2 shafts. Furthermore, the introduction of CNC machining has also had a positive environmental impact. Traditional machining methods generate a considerable amount of waste material, leading to increased environmental pollution and resource depletion. CNC machining reduces this waste significantly, as it requires precise material removal, only leaving behind the finished product. This reduction in waste not only minimizes environmental harm but also supports sustainable manufacturing practices, aligning businesses with stringent environmental regulations.
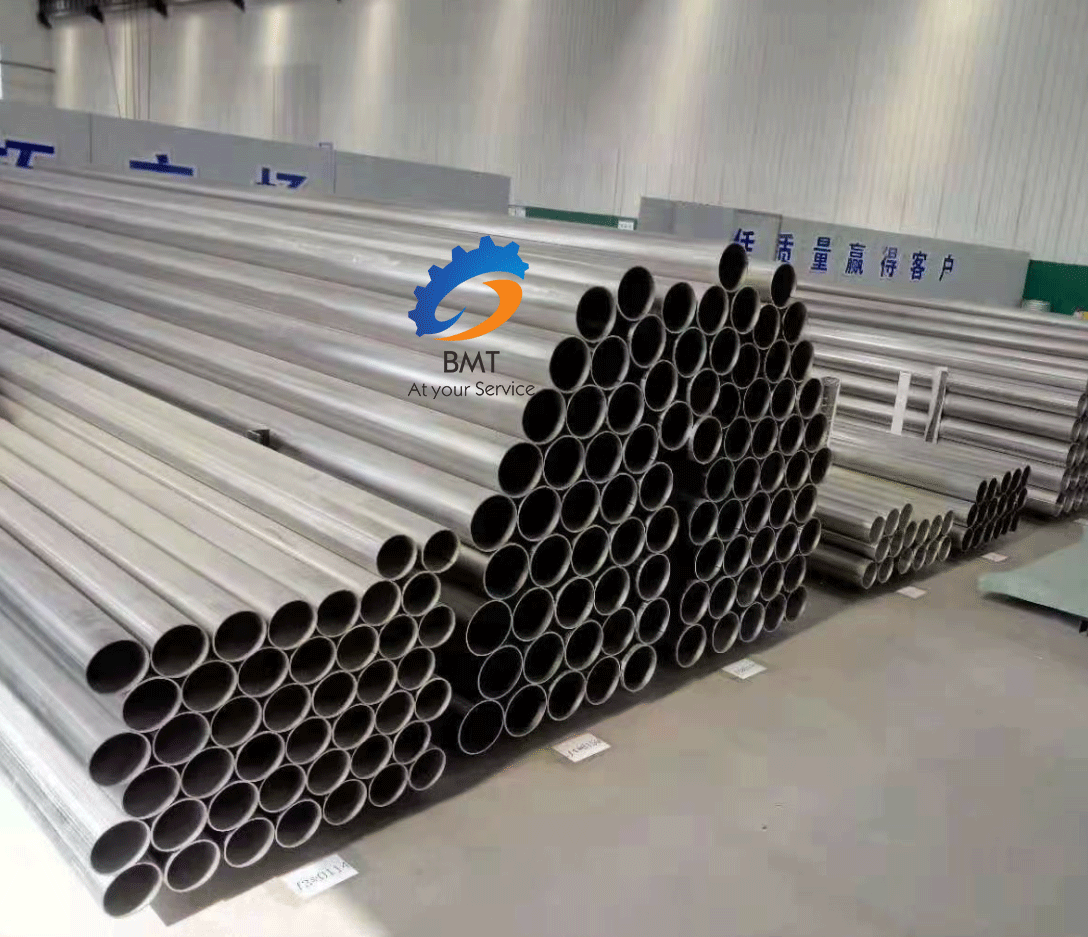
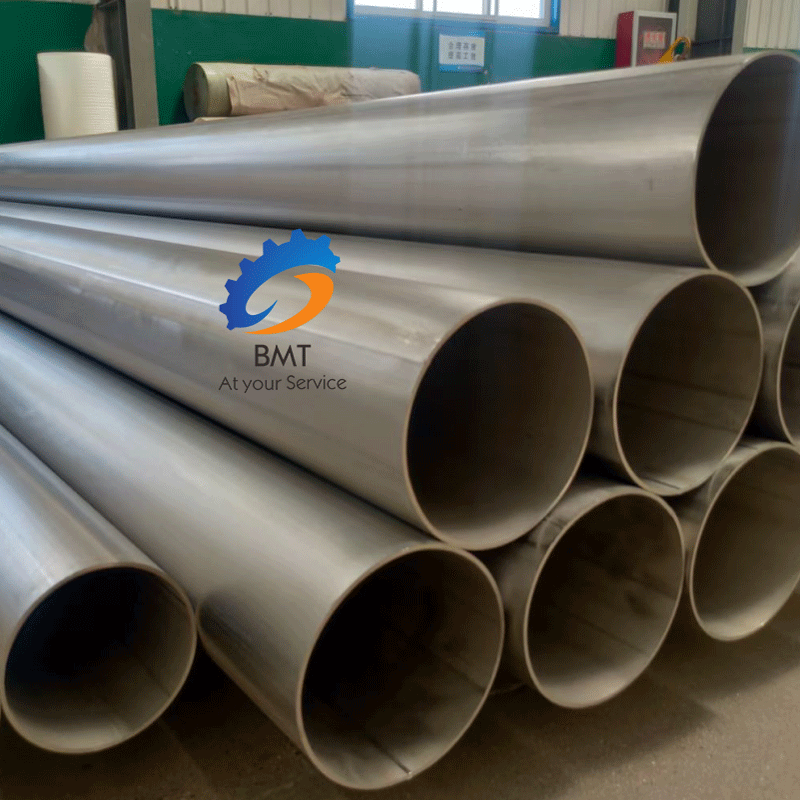
Overall, the integration of custom titanium Gr2 shafts and CNC machining has paved the way for enhanced performance, improved efficiency, and reduced costs in multiple industries. These cutting-edge shafts offer exceptional strength, durability, and corrosion resistance, making them an ideal choice for applications where precision and reliability are paramount. As manufacturers continue to explore the boundless possibilities of CNC machining, the utilization of custom titanium Gr2 shafts is expected to become even more prevalent, driving innovation and redefining industry standards.
Post time: Aug-07-2023