In the process of machining production, any change in the shape, size, position and nature of the production object, so that it becomes a finished product or semi-finished product process is called mechanical processing process.
Machining Process can be divided into Casting, Forging, Stamping, Welding, Machining, Assembly And Other Processes, Mechanical Manufacturing Process generally refers to the parts of the machining process and the assembly process of the machine.
The formulation of mechanical processing process, must determine the workpiece to go through several processes and the sequence of the process, only list the main process name and its processing sequence of the brief process, known as the process route.
The formulation of the process route is to formulate the overall layout of the process process, the main task is to choose the processing method of each surface, determine the processing order of each surface, and the number of the number of the entire process. The process route formulation must follow certain principles.
Principles for drafting the process route of machined parts:
1. First processing datum: parts in the process of processing, as a positioning datum surface should be processed first, in order to provide fine datum for the processing of the subsequent process as soon as possible. It's called "benchmarking first."
2. Divided processing stage: processing quality requirements of the surface, are divided into processing stages, generally can be divided into rough machining, semi-finishing and finishing three stages. Mainly in order to ensure the quality of processing; It is conducive to rational use of equipment; Easy to arrange heat treatment process; As well as facilitate the discovery of blank defects.
3. First face after hole: for box body, bracket and connecting rod and other parts should be processed first plane processing hole. In this way, the plane positioning processing hole, ensure the plane and hole position accuracy, but also on the plane of the hole processing to bring convenience.
4. Finishing processing: Main surface finishing processing (such as grinding, honing, fine grinding, rolling processing, etc.), should be in the last stage of process route, after processing the surface finish in Ra0.8 um above, slight collision will damage the surface, in countries such as Japan, Germany, after finishing processing, with a flannelette, absolutely no direct contact with the workpiece or other objects with the hand, To protect finished surfaces from damage due to transshipment and installation between processes.
Other principles for drafting the process route of machined parts:
The above is the general situation of process arrangement. Some specific cases can be dealt with according to the following principles.
(1) In order to ensure the processing accuracy, rough and finish machining is best carried out separately. Because of rough machining, cutting quantity is large, the workpiece by cutting force, clamping force, heat, and processing surface has more significant work hardening phenomenon, there is a large internal stress of the workpiece, if the rough and rough machining continuous, the precision of the finishing parts will be lost quickly because of the redistribution of stress. For some parts with high machining accuracy. After rough machining and before finishing, low temperature annealing or aging process should be arranged to eliminate internal stress.
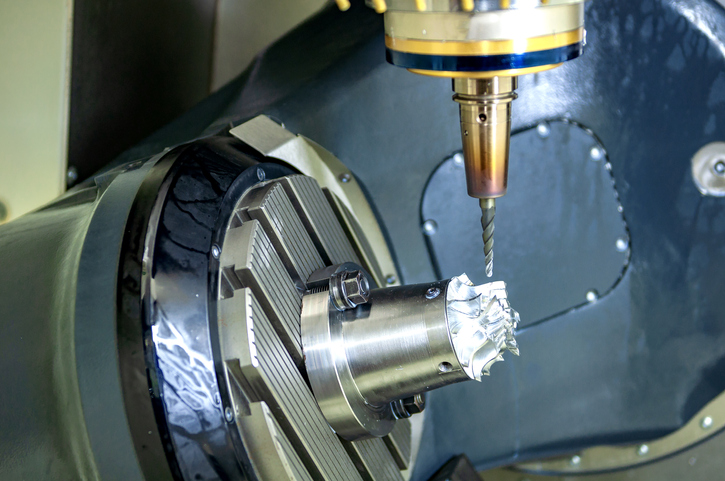
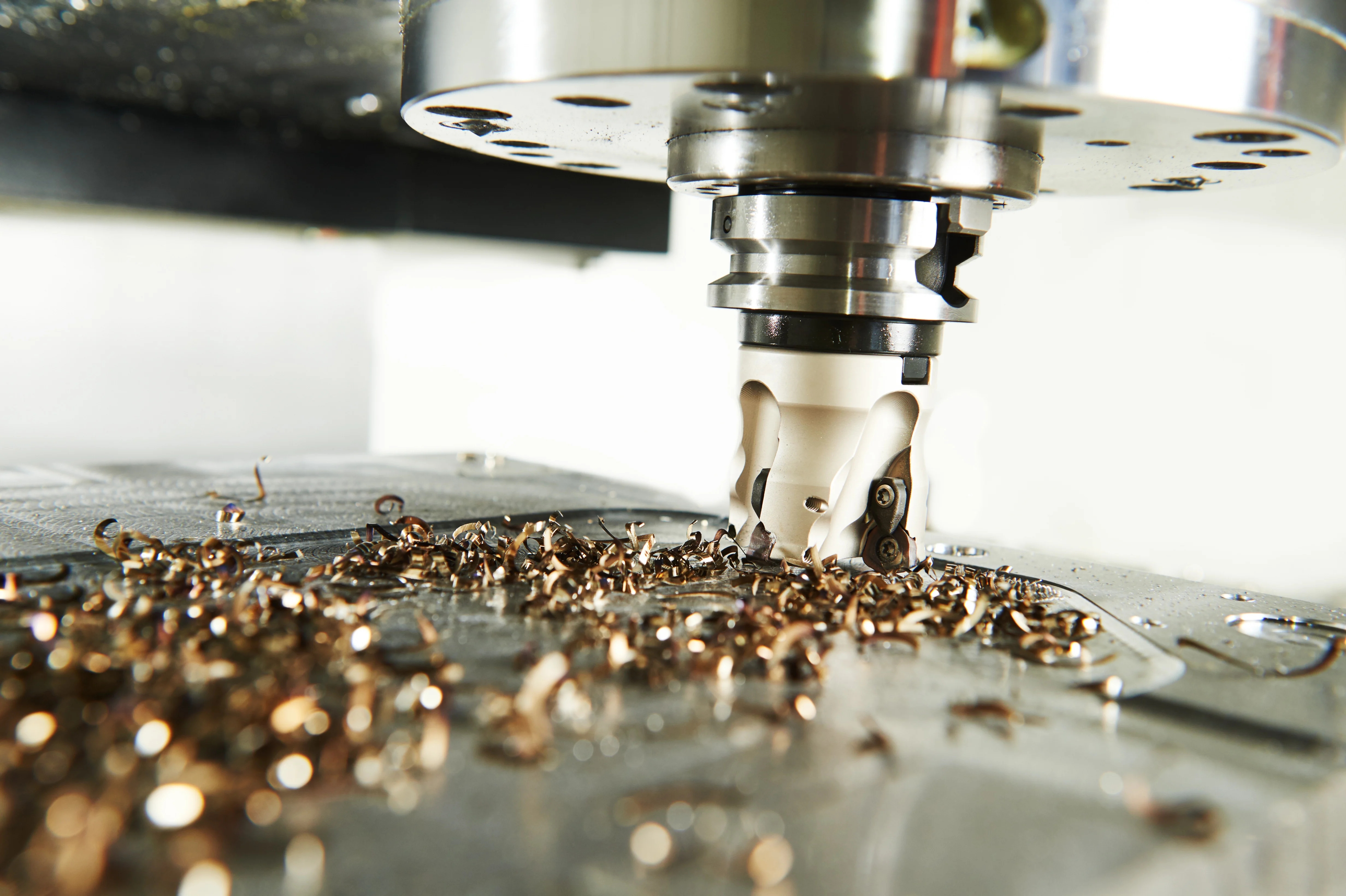
(2) Heat treatment process is often arranged in the mechanical processing process. The positions of heat treatment processes are arranged as follows: in order to improve the machinability of metals, such as annealing, normalizing, quenching and tempering, etc. are generally arranged before machining. To eliminate internal stress, such as aging treatment, quenching and tempering treatment, general arrangements after rough processing, before finishing. In order to improve the mechanical properties of parts, such as carburizing, quenching, tempering, etc., generally arranged after mechanical processing. If the heat treatment after the larger deformation, must also arrange the final processing process.
(3) Reasonable selection of equipment. Rough machining is mainly to cut off most of the processing allowance, does not require a higher processing accuracy, so rough machining should be in a larger power, precision is not too high on the machine tool, the finishing process requires a higher precision machine tool processing. Rough and finish machining are processed on different machine tools, which can not only give full play to the equipment capacity, but also extend the service life of precision machine tools.
When drawing up the process of machining parts, due to the different production types of parts, the method of adding, machine tool equipment, clamping measuring tools, blank and technical requirements for workers are very different.
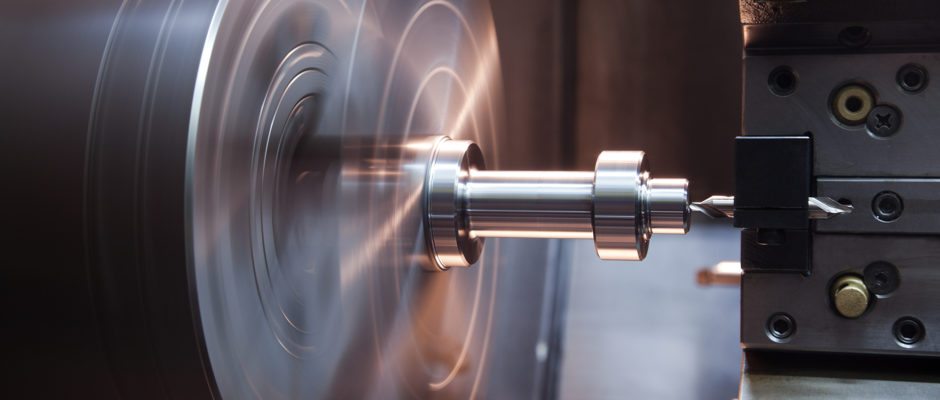
Post time: Aug-23-2021