OEM Machining Service from BMT
The Steps of Establishing the Machining Process Procedure
1) Calculate the annual production program and determine the production type.
2) Analyze part drawing and product assembly drawing, and process analysis of parts.
3) Select blanks.
4) Formulate the process route.
5) Determine the machining allowance of each process, calculate the process size and tolerance.
6) Determine the equipment and tools, fixtures, measuring tools and auxiliary tools used in each process.
7) Determine cutting dosage and time quota.
8) Determine the technical requirements and inspection methods of each main process.
9) Fill in the process documents.
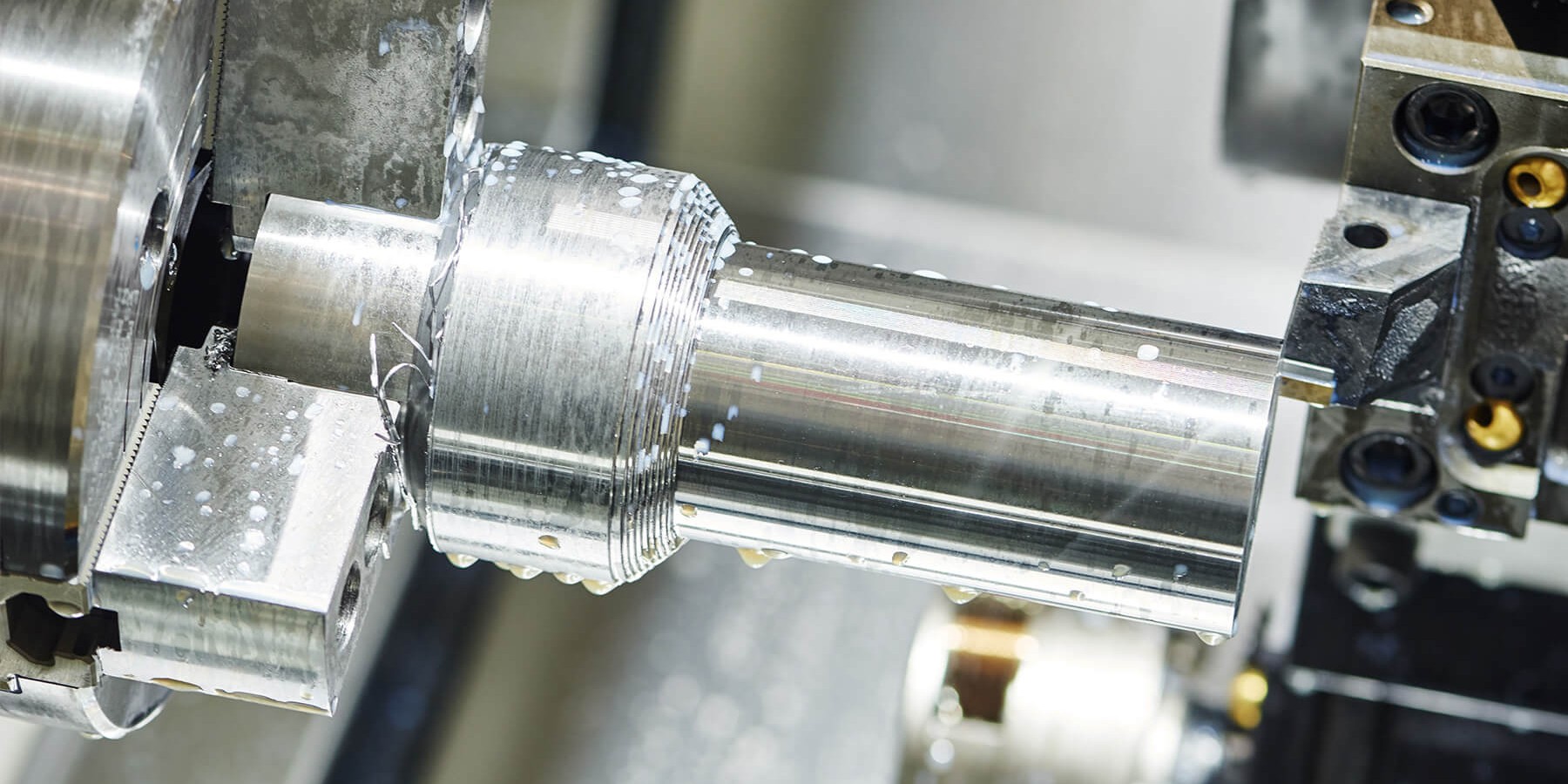
In the process of making technological procedures, it is often necessary to adjust the content that has been preliminarily determined in front, in order to improve economic benefits. In the process of implementing the process procedures, there may be an unexpected situation, such as the change of production conditions, the introduction of new technology, new technology, the application of new materials, advanced equipment, etc., all require timely revision and improvement of the process procedures.
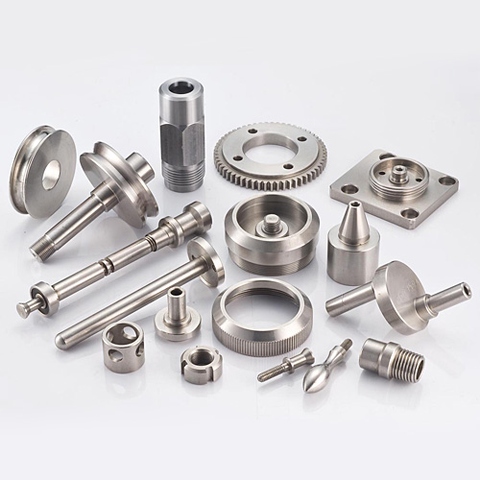
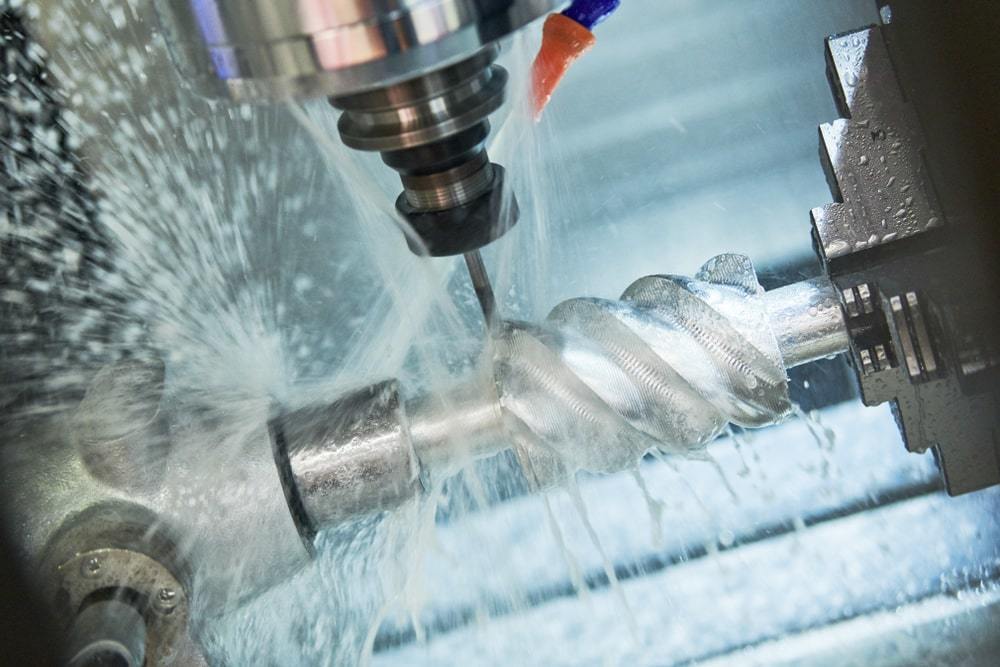
Machining error refers to the degree of deviation between the actual geometric parameters (geometric size, geometric shape and mutual position) and the ideal geometric parameters after machining. After machining, the degree of conformity between the actual geometric parameters and the ideal geometric parameters is the machining accuracy. The smaller the machining error, the higher the degree of conformity, the higher the machining accuracy. Machining precision and machining error are two formulations of the same problem. Therefore, the size of the processing error reflects the processing accuracy.
1. Machine Tool manufacturing error machine tool manufacturing error mainly includes the spindle rotation error, guide rail error and transmission chain error. The spindle rotation error refers to the actual spindle rotation axis of each moment relative to its average rotation axis of the change, it will directly affect the precision of the workpiece being processed. The main reasons for the spindle rotation error are the coaxiality error of the spindle, the error of the bearing itself, the coaxiality error between the bearings, the spindle winding, etc. The guide rail is the datum to determine the relative position relation of each machine tool part on the machine tool, also is the datum of the machine tool movement. The manufacturing error, uneven wear and installation quality of the guide rail are the important factors that cause the error of the guide rail. Transmission chain error refers to the relative motion error between transmission elements at both ends of the transmission chain. It is caused by the manufacturing and assembly errors of each component link in the transmission chain, as well as the wear and tear in the use process.
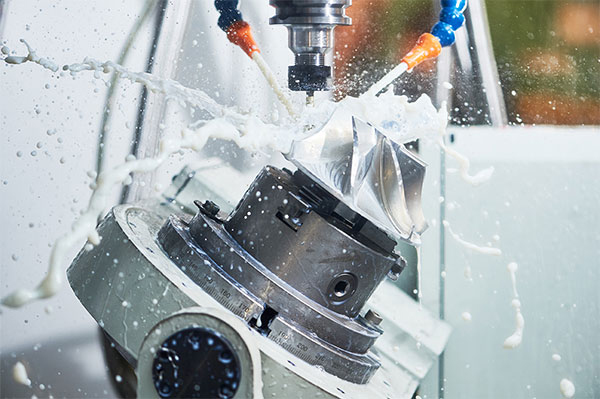
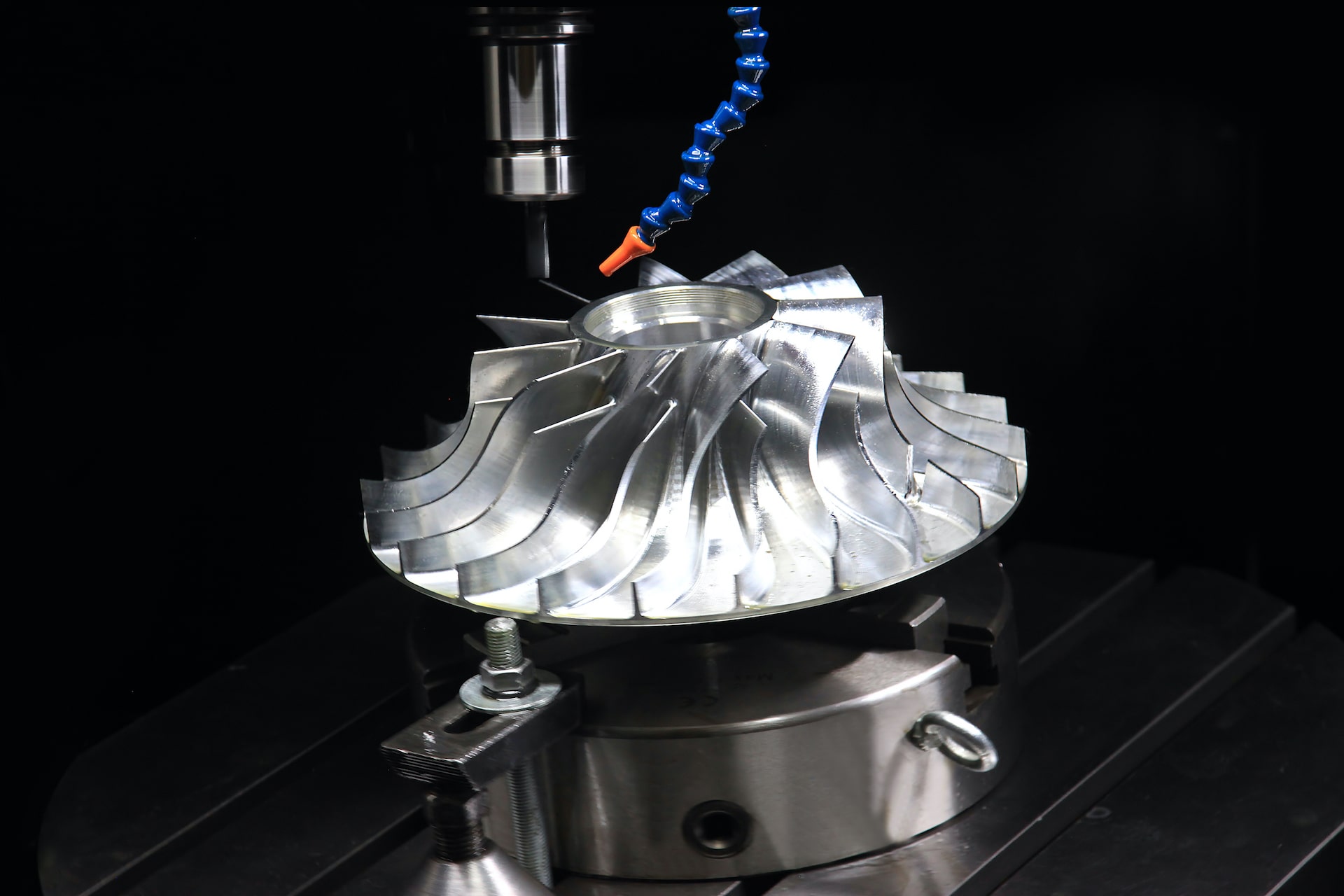
2. The geometric error of the tool any tool in the cutting process is inevitable to produce wear, and thus cause the size and shape of the workpiece to change. The influence of tool geometric error on machining error varies with different kinds of tools: when using fixed-size cutting tools, the manufacturing error of the tool will directly affect the machining accuracy of the workpiece; However, for the general tool (such as turning tool), the manufacturing error has no direct effect on the machining error.