5 Ways to Improve Sheet Metal Parts
Sheet metal fabrication is a handy set of manufacturing processes used to create parts from flat pieces of metal. Sheet metal comes in a range of materials and thicknesses, and can be used to create parts like appliances, enclosures, brackets, panels and chassis, etc.
Compared with CNC machining, sheet metal fabrication is dictated by extremely strict design specifications. For some workers who are new for sheet metal fabrication, maybe it is difficult. Sheet metal must be bent and cut in particular ways, and is only suitable for certain parts and products.
As a matter of fact, it is important to learn some basic principles of sheet metal fabrication before working. Using sheet metal fabrication, technicians can create durable, low-cost parts from different materials. These parts can be used across a wide range of industries, from aerospace to home appliance.
The sheet metal thickness used in the manufacturing process is usually between 0.006 and 0.25”, with the dimensions reliant on the given materials and end-use of the part.
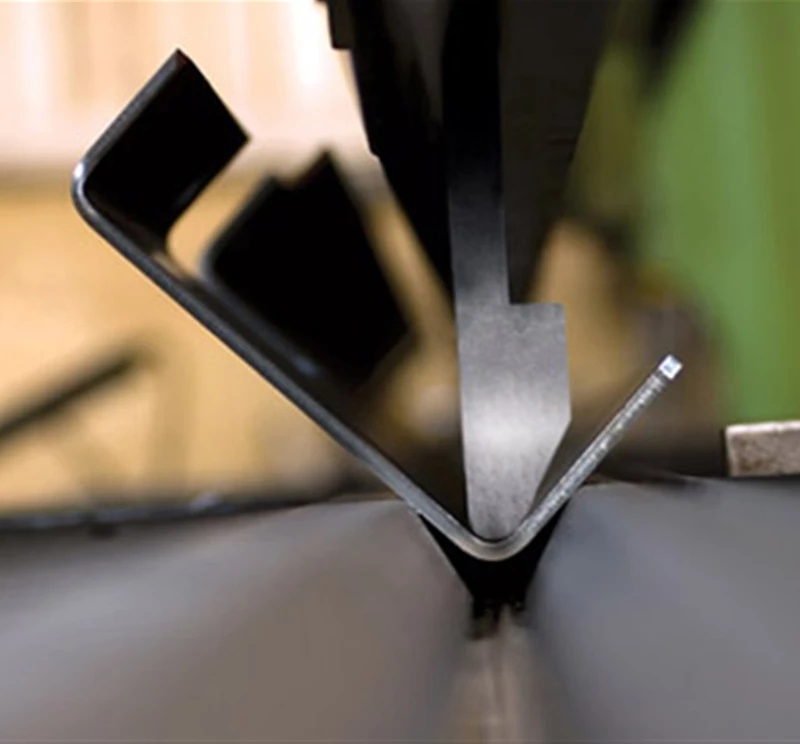
Product Description
Sheet metal fabrication is unique among the various manufacturing processes. For this reason, the technical maybe can design CNC machining parts or mold parts, but it is difficult to design sheet metal parts.
By observing the following six tips, the designers can create sheet metal parts that are strong, easy to fabricate and more resistant to breakage.
1. Holes and Slots
Since sheet metal fabrication is frequently used to create enclosures, brackets and similar items, holes and slots are often required for screws, bolts or interlocking sections. Holes are usually created with a punch and die mounted in a press, allowing for a precise circular shape to be cut out of the sheet metal. But if holes are not correctly made, the hole may deform or even cause the part itself to break.
When punching holes in sheet metal, a few important rules should be followed. Holes should be 1/8” from any wall or edge and should be spaced apart by at least 6 times the thickness of the sheet metal. Furthermore, the diameters of all holes and slots should match or exceed the thickness of the sheet metal.
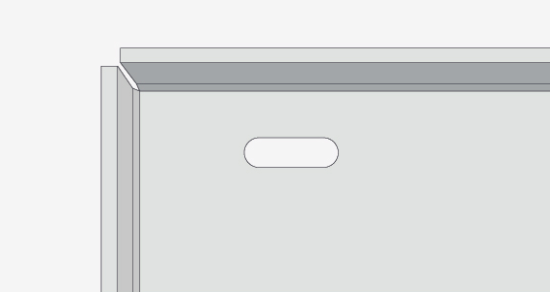
2. Hems
Hemming is a good way to make a sheet metal part safe and functional. We form both open and closed hems. The tolerance of a hem is dependent upon the hem’s radius, material thickness, and features near the hem. We recommend that the minimum inside diameter equals the material thickness, and a hem return length of 6x material thickness.
When adding a hem to a sheet metal part, a few guidelines should be followed to ensure optimum performance. For starters, it is almost always better to avoid closed hems. Closed hems risk damaging the material because of the extreme angle of the bend, so open hems, which leave a gap between the two sides of the hem, are preferable.
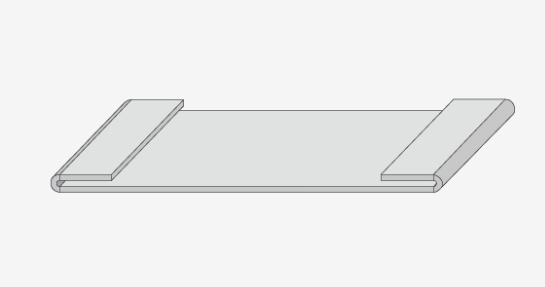
3. Bends
Bending is one of the most important forming processes in sheet metal fabrication. Using equipment like brakes and machine presses, factory is able to manipulate sheet metal into new shapes. For bending, in order to ensure the accurate and even bend, we should follow certain rules, and reduces the possibility of damage to the material.
One rule to follow is that, when designing a sheet metal part with bends, the inside bend radius should match or exceed the thickness of the sheet metal to avoid deformation. It is recommended to use the same radius across all bends. Maintaining consistency in bend direction and radius can help to reduce costs, as the part will not have to be reoriented and the bending equipment can repeat one identical procedure.
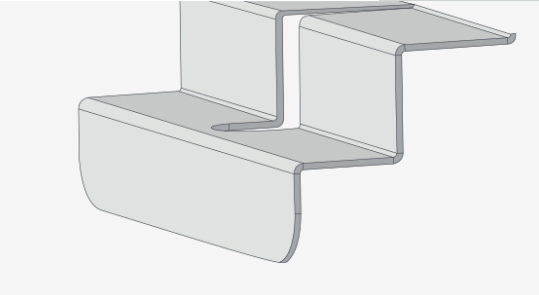
4. Notches and Tabs
Notches and tabs are the main features of sheet metal parts that are useful for adding screws or fasteners or for slotting multiple parts together. Notches are small indents in the edge of a part, while tabs are protruding features. A tab in one sheet metal part is often incorporated to fit into a notch of another part.
Like other sheet metal features, creating suitable notches and tabs also needs to follow some rules: notches must be at least the material’s thickness or 1mm, whichever is greater, and can be no longer than 5 times its width. Tabs must be at least 2 times the material’s thickness or 3.2mm, whichever is greater, and can be no longer than 5 times its width.
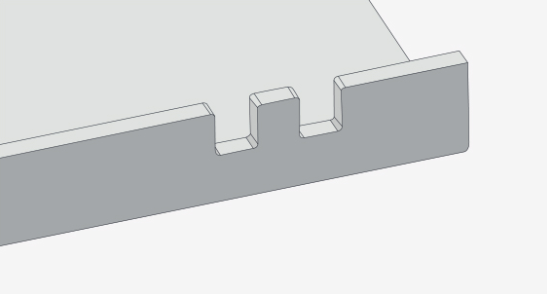
5. Offsets and Countersinks
Countersinks can be made by CNC Machining or formed by special equipment. Tolerance for formed countersink major diameter is very strict, because it maybe needs to be used with screws or fasteners. Offsets are used to create Z-shaped profiles in sheet metal parts.
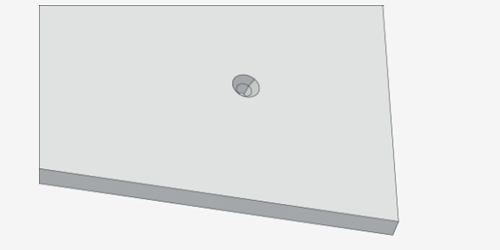
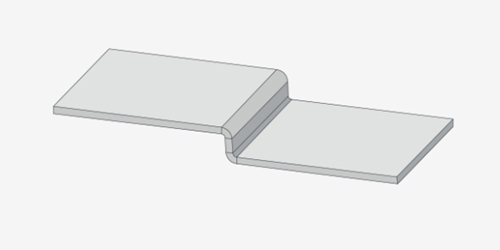
6. Finishing
Depending on the application and material used, sheet metal parts can be finished with bead blasting, anodizing, plating, powder coating and various other processes, either for functional purposes or to simply improve the appearance of the part.
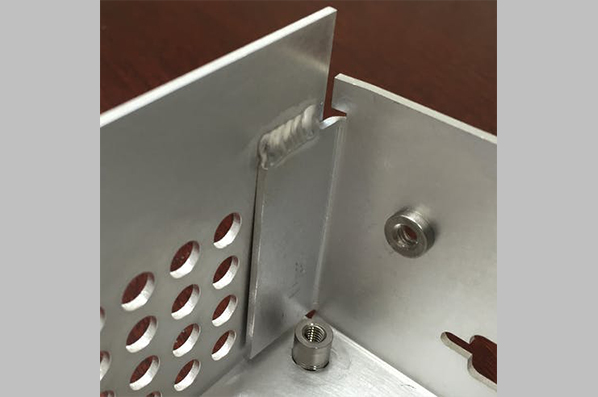

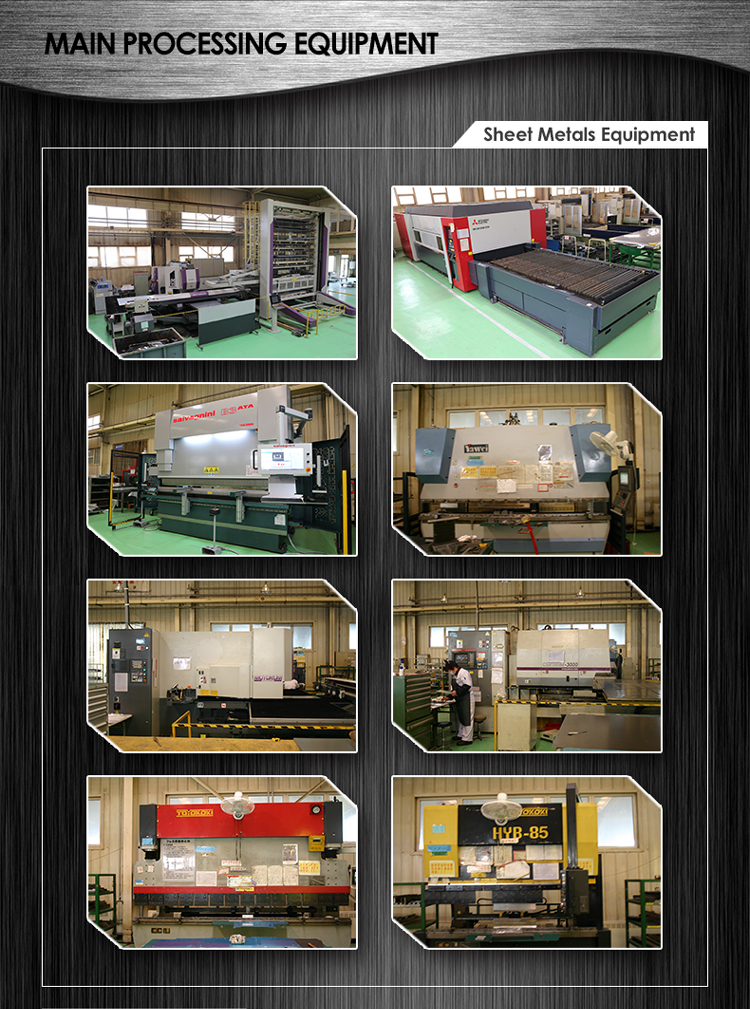
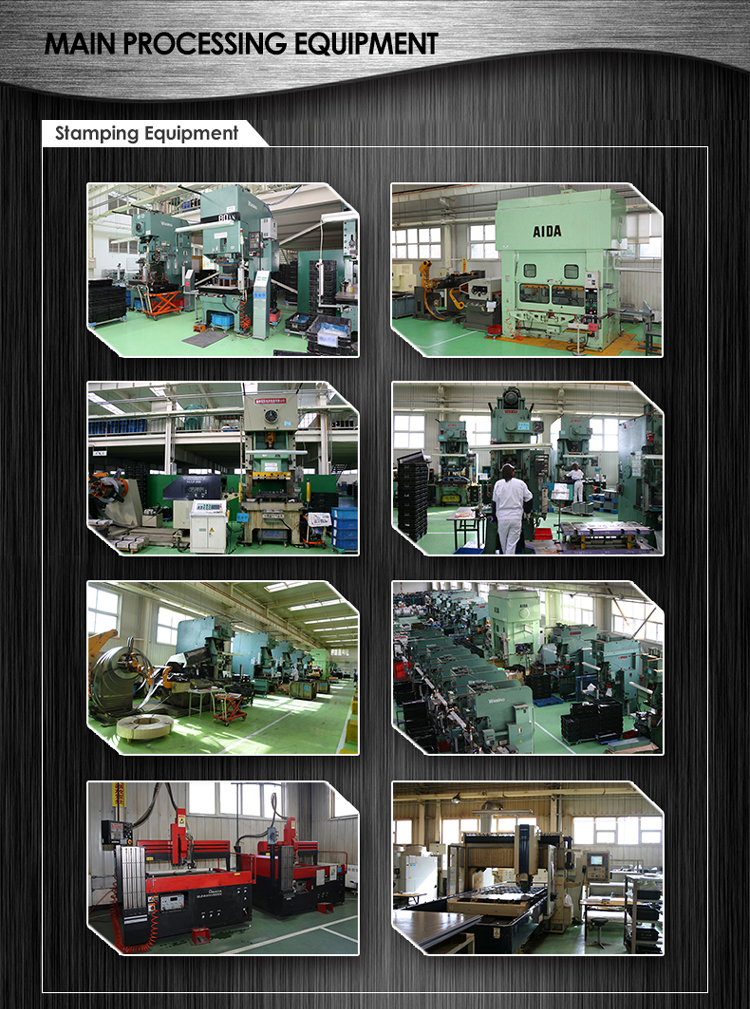