Your Precision Machining Manufacturer
PRECISION MACHINING
Precision machining is a process in which the shape or performance of the workpiece is changed by processing machinery. According to the temperature state of the workpiece to be processed, it is divided into cold processing and hot processing. Normally, processing at room temperature, and does not cause chemical or phase changes of the workpiece, it is called cold processing. Generally, processing at higher or lower than normal temperature will cause the chemical or phase change of the workpiece, which is called thermal processing. Cold processing can be divided into cutting processing and pressure processing according to the difference in processing methods. Thermal processing commonly includes heat treatment, forging, casting and welding.
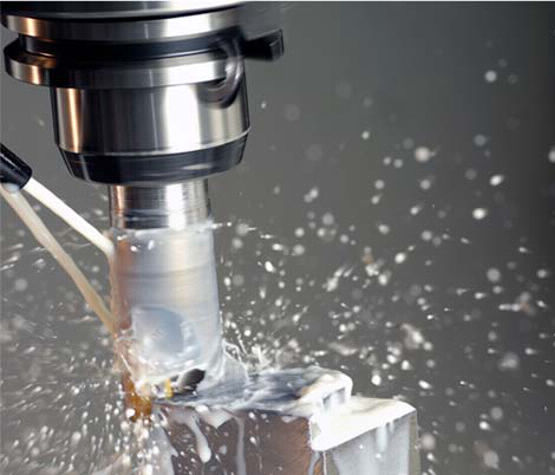
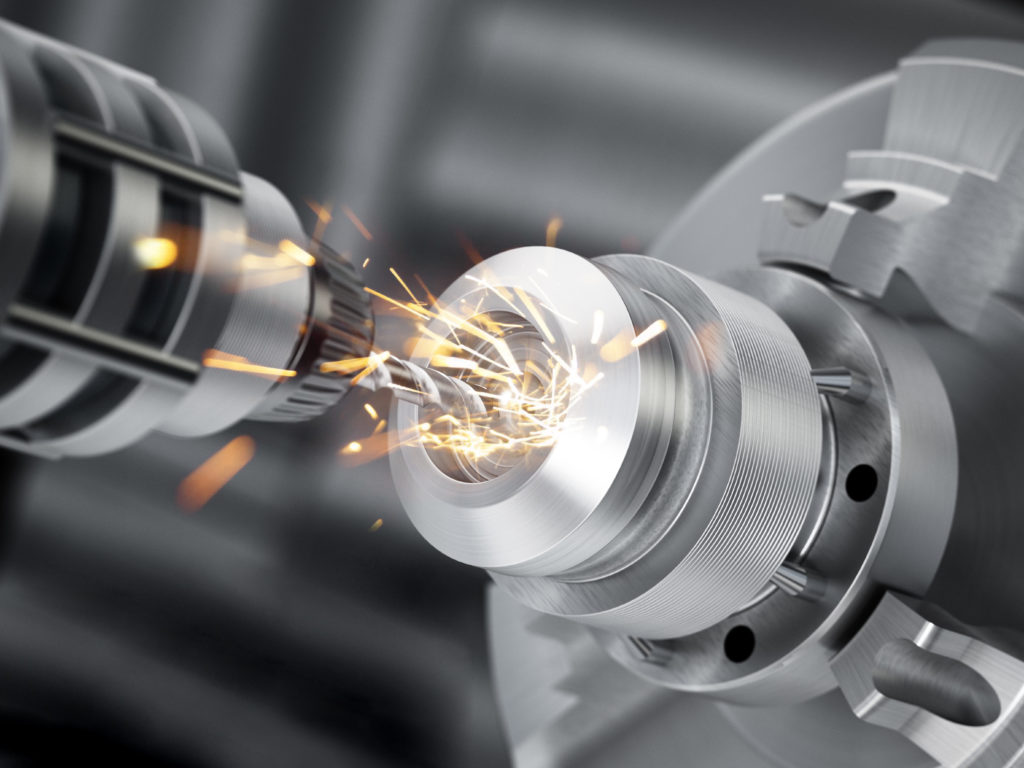
Auto parts processing is the unit that constitute the whole of auto parts processing and the products that serve the processing of auto parts. As the foundation of the auto industry, auto parts are necessary factors to support the sustainable and healthy development of the auto industry. In particular, the current independent development and innovation in the auto industry that is being carried out vigorously and in full swing requires a strong parts system to support it. Vehicle independent brands and technological innovation require parts and components as the foundation, and independent innovation of parts and components has a strong driving force for the development of the vehicle industry. They influence and interact with each other. There is no independent brand of complete vehicles, and a strong parts system. The R&D and innovation capabilities of the company are difficult to burst, and without the support of a strong component system, it will be difficult for independent brands to become bigger and stronger.
Parts refer to individual parts that cannot be separated in machinery. They are the basic components of the machine and the basic unit in the machine manufacturing process. The manufacturing process generally does not require an assembly process. Such as sleeves, bushes, nuts, crankshafts, blades, gears, cams, connecting rod bodies, connecting rod heads, etc. For our precision machining, the processing is very strict, and the processing procedures include cutting in and out. There are specific requirements for size and accuracy, such as 1mm plus or minus micrometers, etc. If the size is too large, it will be wasted. At this time, it is equivalent to reprocessing, time-consuming and laborious, and sometimes even the entire processed material is scrapped. This has caused an increase in cost, and at the same time, the parts are definitely unusable.
Some common equipment cannot finish mold processing, such as some cavities with small R angles; electrodes are processed by electric pulse. These are usually made of copper or graphite. The rapid development of mold manufacturing technology has become an important part of modern manufacturing technology. Modern mold manufacturing technology is developing in the direction of accelerating information drive, improving manufacturing flexibility, agile manufacturing and system integration. It is specifically manifested in the CAD/CAM technology of the mold, the laser rapid prototyping technology of the mold, the precision forming technology of the mold, and the ultra-precision processing technology of the mold. The mold design uses the finite element method and the boundary element method to carry out the flow, cooling and heat transfer process. Dynamic simulation technology, mold CIMS technology, advanced manufacturing technologies such as mold DNM technology and numerical control technology have been developed.
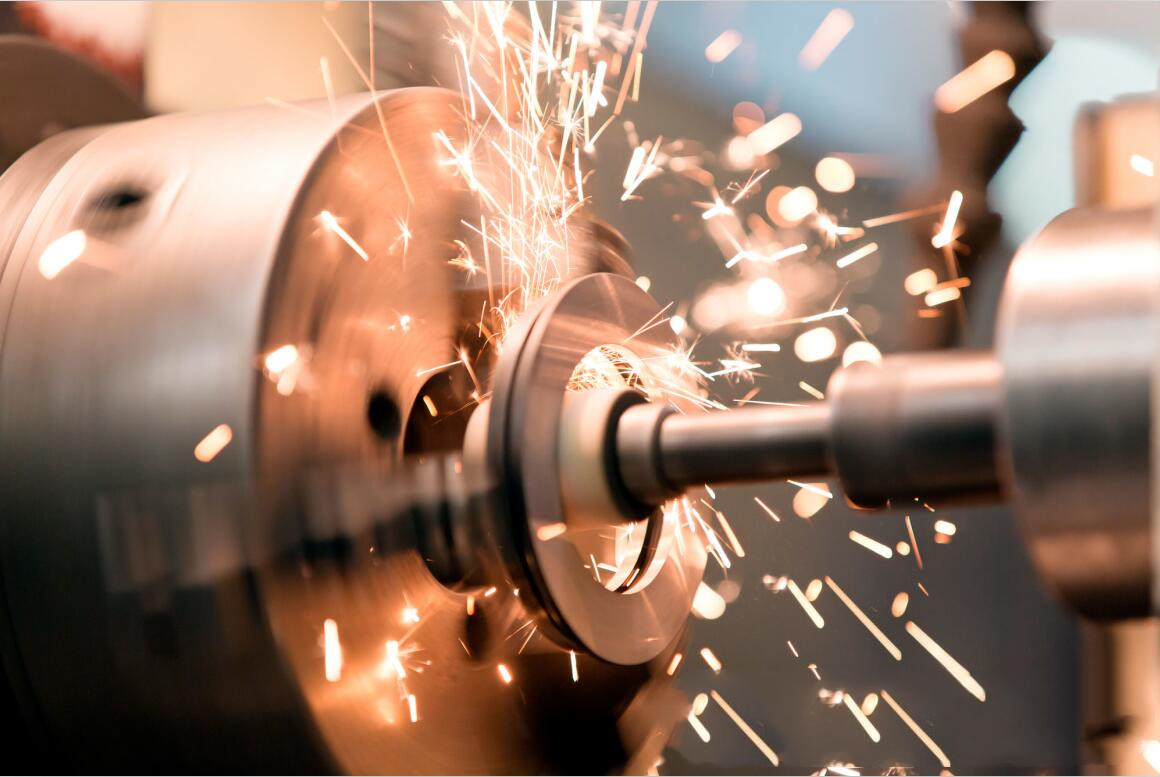
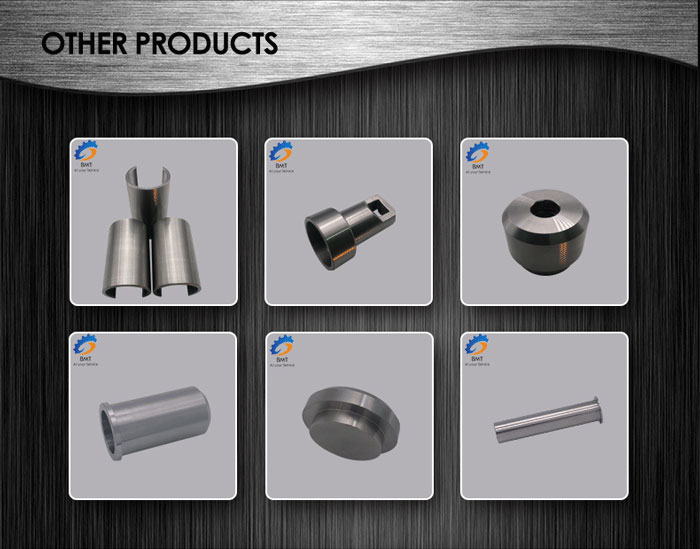
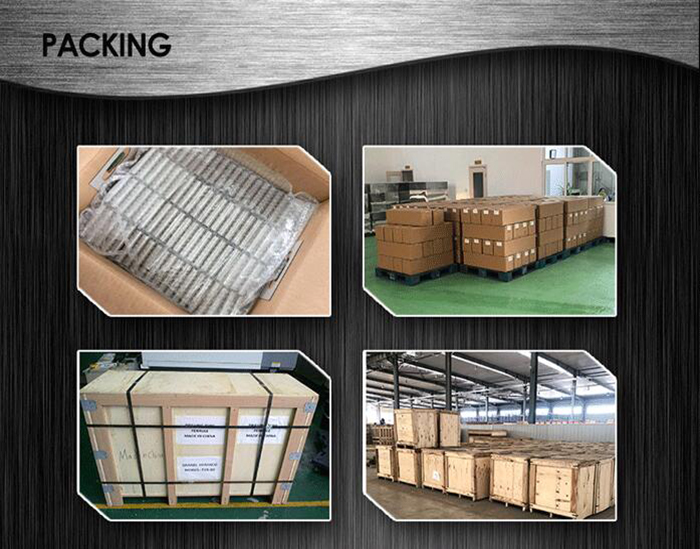